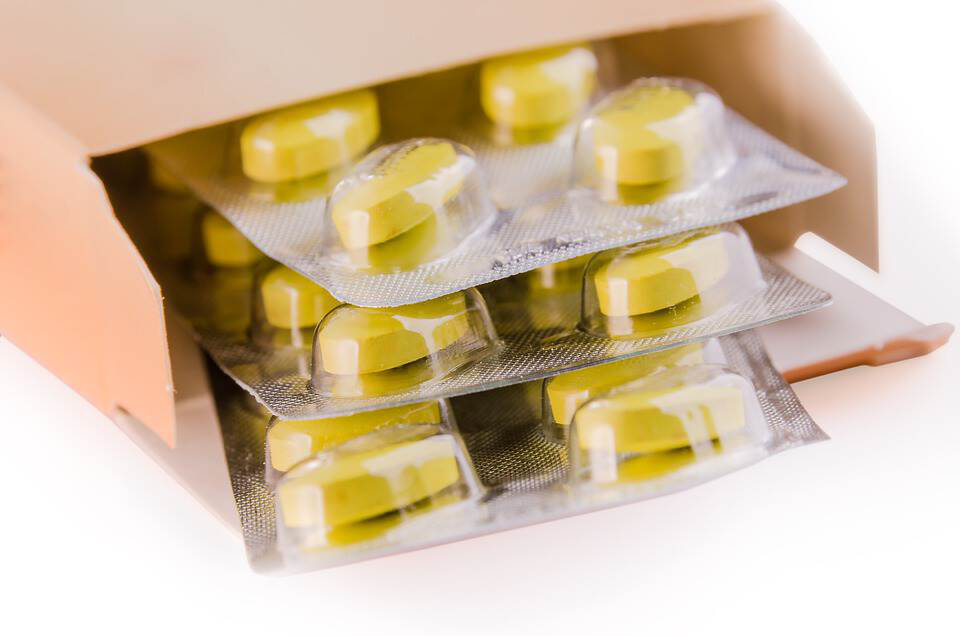
Source: Pixabay
The pharmaceutical packaging industry faces a multitude of challenges due to the sensitive nature of its products. Poor packaging can have dire consequences, resulting in chemical alterations to the product, rendering it ineffective and compromising its efficacy. This essay will explore six challenges facing pharmaceutical packaging.
To ensure the safety and efficacy of pharmaceutical products, it is essential to overcome these challenges when using medicine packaging machines, capsule filling machinery, tablet press machines, and medicine secondary packaging solutions.
Child-resistant Packaging
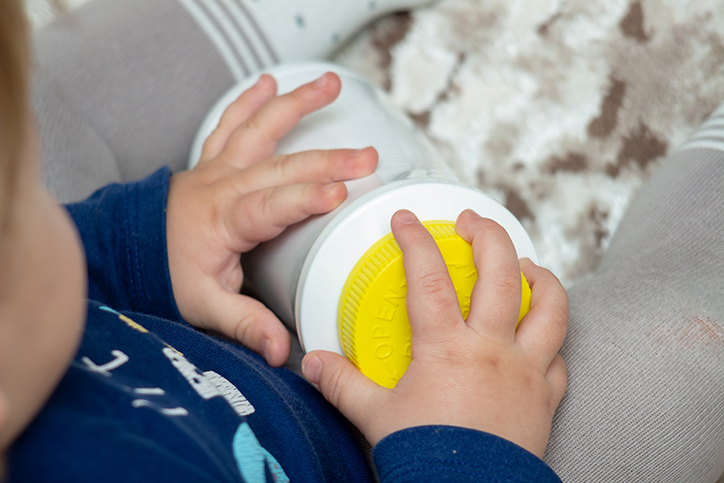
Source: Istock
Child-resistant packaging is designed to help protect children from the dangers of accidentally ingesting hazardous items, like certain prescription and over-the-counter (OTC) medications. It is designed in a way that is difficult for young children to open or gain access to, while still being easy enough for adults to use. Examples of products available OTC and requiring C-R packaging include acetaminophen, aspirin, diphenhydramine, ibuprofen, iron-containing drugs and dietary supplements, imidazolines, methyl salicylate, mouthwash, naproxen, and OTC switch drugs.
The challenge of providing child-resistant packaging in order to protect children from accessing potentially hazardous medicines is one that can be overcome with thoughtful design. Manufacturers can implement easy-open tabs and include clear instructions on proper use like using text instructions on labels, as well as consider other methods such as increasing the packaging size.
Additionally, companies should ensure their packaging is compliant with regulations by conducting routine tests with children, and consider unit-dose packaging to make it harder for young hands to open.
By taking these steps, manufacturers can ensure they are providing safe and effective packaging that puts children’s safety at the forefront.
Storage and Temperature Control
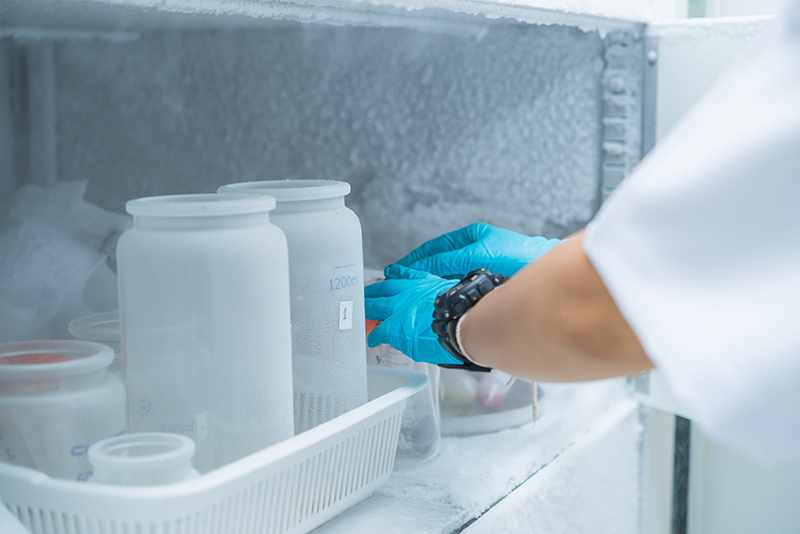
Source: Reewungjunerr
Second, the pharmaceutical industry faces the challenge of controlling and maintaining the temperature of its products during storage. Temperature is the main factor in this regard, not just in pharmacy storage but also during transit. Vaccines, in particular, are sensitive to heat and require a specific temperature range, which is why medical-grade refrigerators are a suitable investment for vaccine storage.
Drugs in solution form have a different make-up and hence a different temperature range. Therefore, it is important to follow the guidelines set by the manufacturing process in order to ensure the utmost quality of the pharmaceuticals. To ensure that the quality of the product is upheld, advanced storage systems, such as temperature-controlled warehouses and temperature-controlled packaging, must be employed.
Temperature-controlled packaging is essential for many industries that require the transport and storage of temperature-sensitive goods. There are a variety of temperature-controlled packaging solutions available to ensure that goods arrive safely and in the same condition as they left. This can include insulated shipping boxes, temperature-controlled shipping containers, refrigerated transport vehicles, and thermal packaging materials such as bubble wrap, styrofoam, and foam-in-place. Additionally, temperature-sensitive items may require the use of temperature monitoring devices, cold packs, and dry ice to ensure that the products remain at the desired temperature during transportation.
All of these solutions help to ensure that goods are transported and stored in the proper temperature conditions and make sure that products arrive in the same condition that they left.
Product Protection
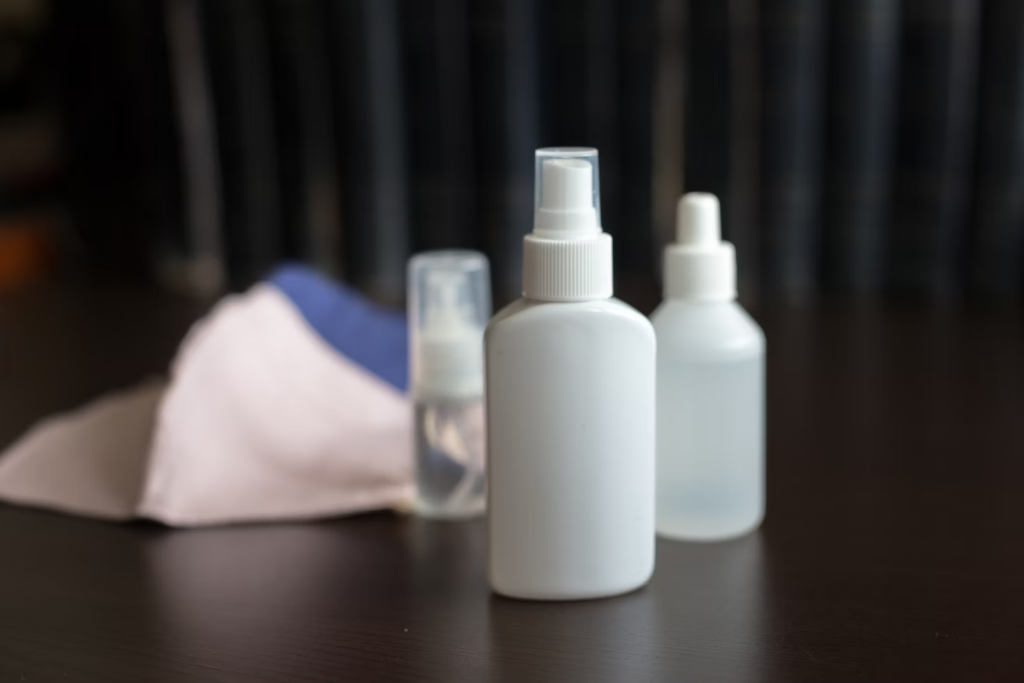
Source: Unplash
The third challenge facing the pharmaceutical industry is product protection. To ensure that products are not damaged in transit, pharmaceutical companies must invest in appropriate packaging designs and materials to protect their products. This will help to prevent any potential damage during transport and help to ensure that products arrive safely and securely. Protective packaging solutions can include things like robust outer packaging, additional padding and cushioning, and moisture-resistant materials.
By taking this extra step, companies can rest assured that their items will reach their destination in the best condition possible.
Regulatory Compliance
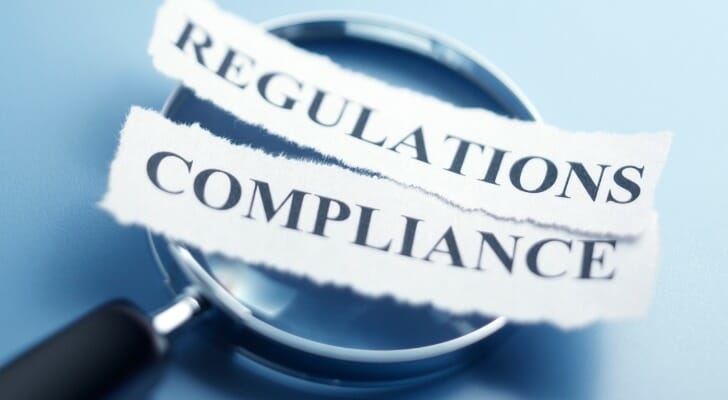
Source: Istock
How to stay up to date with regulatory compliance is a major challenge for operators of medical packaging machines, capsule filling machines, medicine secondary packaging, and tablet presses. The pharmaceutical industry is exacting, requiring not only product quality but also proper packaging and labeling to prevent contamination, tampering, and incorrect information.
To make the process more efficient, companies should aim to address key challenges related to packaging design and implementation. Anti-tampering specifications are essential following the Tylenol tragedy and include features like blister packaging, shrink wrap, HIS liners, and tape seals. Multi-layered label regulations are also highly detailed and must include product name, ingredients, intended use, storage instructions, expiration date, drugs facts table, dosage instructions, warnings or side effects, and allergy information. It is essential to ensure proper labeling and avoid costly recalls that can occur due to incorrect information. Finally, different countries and regions can modify the World Health Organization’s pharmacopeia standards, which means pharmaceutical products may require multiple labels or types of packaging depending on their destination.
Packaging Materials
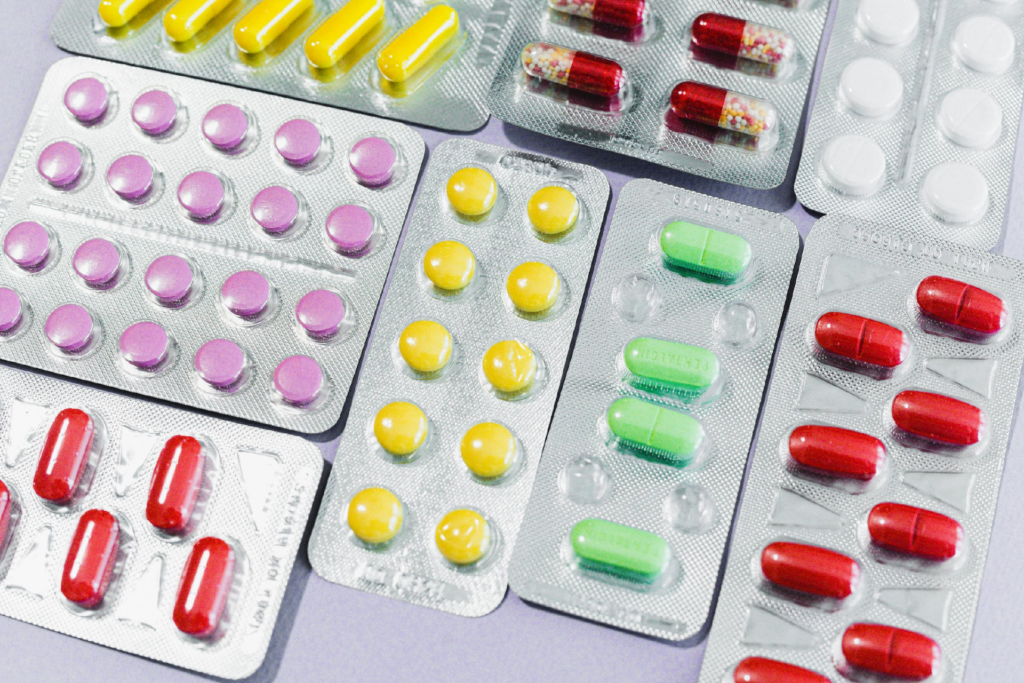
Source: Pexel
Packaging for drugs is an ever-evolving field, with new materials being developed to meet the needs of the pharmaceutical industry. Glass and plastics are the most common materials used for drug packaging, but the choice of materials is determined by a variety of factors, such as ensuring protection from contamination, facilitating the delivery of medicines through sprays, injectables, and blister packs, and reducing the environmental impact of the industry.
To this end, more sustainable materials such as paper, cardboard, plant-based plastics, glass, metal, and other reusable or recyclable containers are being considered. In addition, biodegradable adhesives, labels, and inks must also be taken into account to further reduce the environmental footprint.
It is essential to ensure that the health and safety of consumers are not compromised while striving to create a more sustainable packaging solution for the pharmaceutical industry. With the emergence of innovative and new-age drugs, it is important to take into account the potential conflicts between drug combinations and packaging materials. For instance, certain drug combinations may cause glass packaging to flake, or silicone oil used in prefilled syringes may disturb the composition of protein complexes.
By taking a holistic approach to sustainability, we can ensure that the health and safety of consumers are not compromised and the environmental impact of the industry is reduced.
Quality Control and Assurance
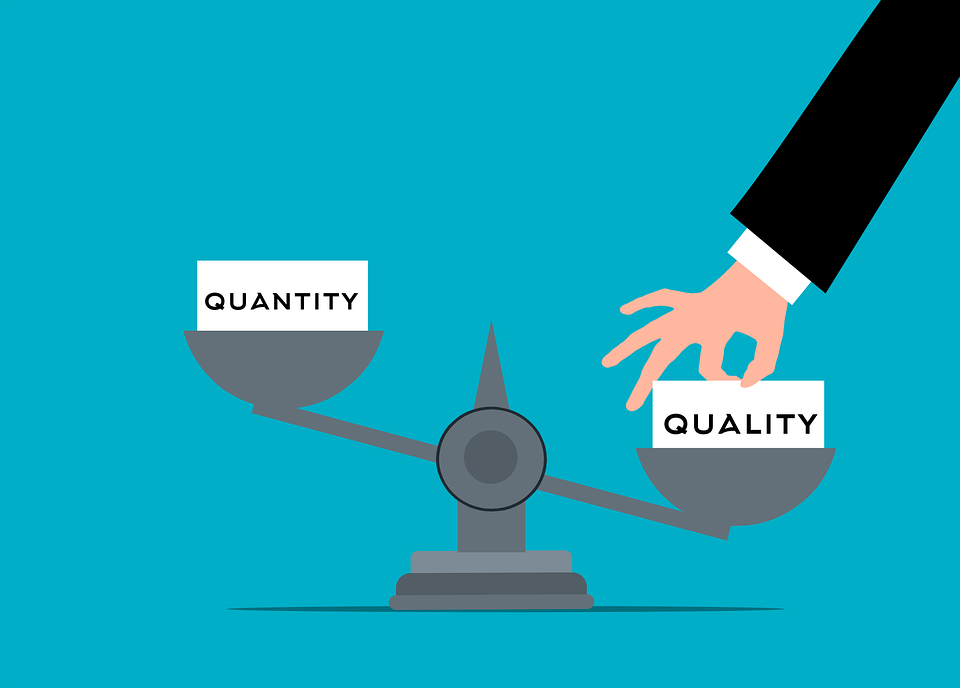
Source: Pixabay
Quality control and assurance are major challenges for medicine packaging. To ensure the highest standards, it is essential to employ reliable testing methods such as high-resolution imaging and spectroscopy to detect any potential defects. In addition, a dedicated quality assurance team should be established to carry out regular inspections of each batch of drugs before they are shipped.
Furthermore, meticulous records must be kept of every stage of the packaging process, so any discrepancies can be quickly identified and rectified. In order to meet the necessary requirements, medical packaging bags must possess certain mechanical properties to protect the product, as well as barrier performance to keep out moisture, water vapor, gas, light, aroma, odor, heat, etc.
Additionally, safety is of paramount importance, so the toxicity of the packaging material must be kept to a minimum, and it must be non-corrosive and have anti-insect, anti-moth, and anti-rat properties. It should also be suitable for processing and easy to mechanize and automate for large-scale industrial production, as well as being economical and environmentally friendly.
Finally, for effective quality management, the pharmaceutical packaging material manufacturing enterprise must be equipped with a quality management department, run by the person in charge, and staffed by suitable personnel with the right resources and equipment.
Conclusion
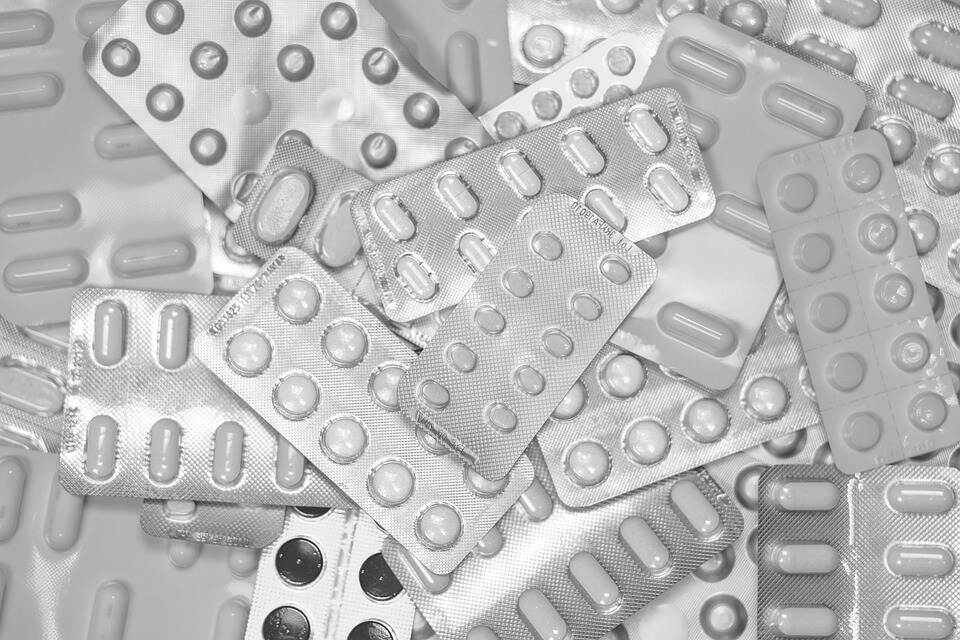
Source: Pixabay
In conclusion, the pharmaceutical packaging industry faces a variety of challenges in order to ensure the safety and efficacy of its products. These challenges include child-resistant packaging, temperature control, product protection, regulatory compliance, packaging materials, and quality control and assurance.
By addressing each challenge in a thoughtful and comprehensive manner, manufacturers can ensure their products remain safe and effective, while also reducing their environmental impact. By investing in advanced storage systems, protective packaging solutions, and eco-friendly materials, companies can rest assured that their products will arrive in perfect condition and meet all regulatory requirements.