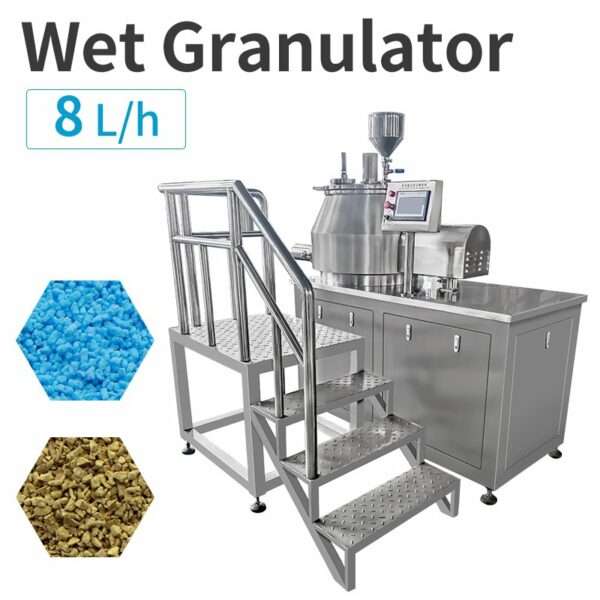
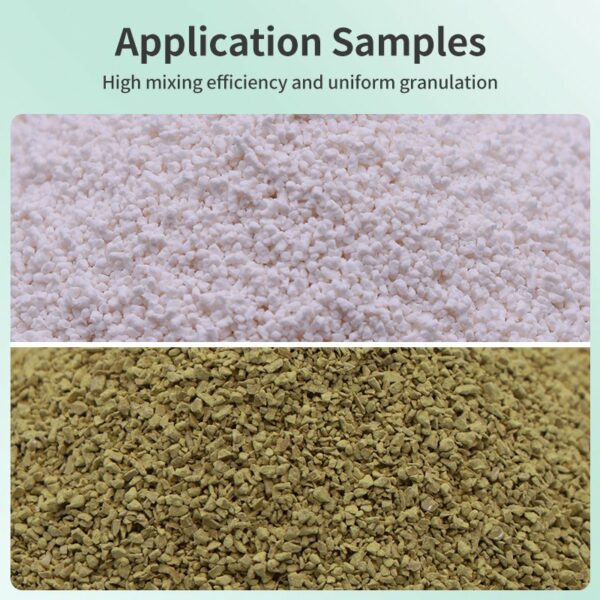
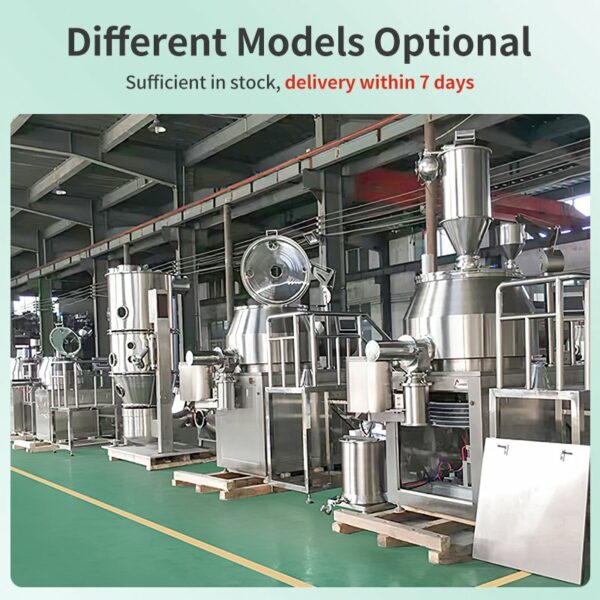
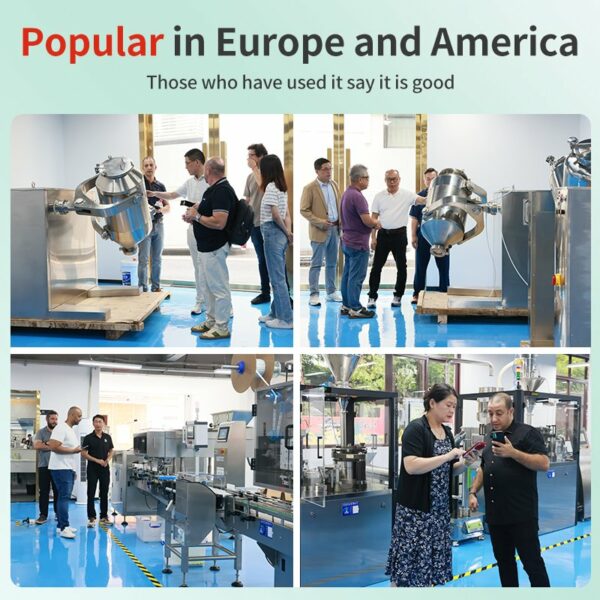

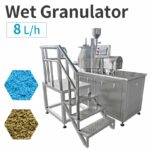
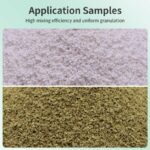
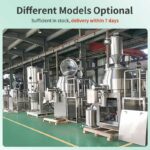
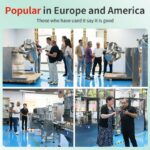
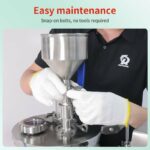
High Efficient Wet Granulator
High efficient wet granulator used fine powders are converted into granules through the use of a liquid binder. Granulation improves the flowability, compressibility, and homogeneity of powders, making them easier to process in subsequent steps like tablet compression or capsule filling.
Pharmaceutical Industry: Wet granulators are widely used to prepare granules for tablet compression, ensuring the powders have good flowability and compressibility. It is commonly used for drugs that require precise dosing and homogeneity.
Nutraceuticals: Used for granulating vitamins, minerals, and other dietary supplements.
Chemical Industry: Used in granulating chemicals and powders for various industrial applications.
Wet granulation is an essential process in the pharmaceutical and chemical industries, and the wet granulator is the central machine that makes it possible. It ensures the production of high-quality, uniform granules that meet industry standards for further processing and product development.
Specification:
Up to 8 L/h
Delivery within 7 days
Suit for powdery and paste-type materials