The efficient tablet production plays a crucial role in the pharmaceutical and manufacturing industries, where the demand for high-quality and consistent tablets is paramount. Rotary tablet press machines have revolutionized production, increasing output and enhancing tablet quality. In this comprehensive guide, we will delve into the intricacies of rotary tablet press machines, exploring their components, advantages, factors influencing production efficiency, optimization techniques, and troubleshooting.
What is Rotary Tablet Press Machines?
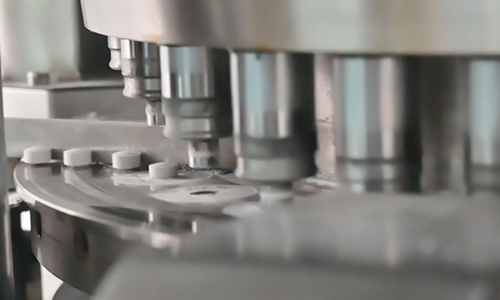
Rotary tablet press machines are an essential piece of equipment used in tablet manufacturing. It is a multi-station machine that compresses granulated powders into tablets of various shapes and sizes. With their high-speed rotation, these machines efficiently transform raw materials into tablets in a continuous manner, facilitating mass production.
Tablet making machine consist of several key components, each serving a vital role in the tablet production process. The main components include:
- Hopper: The hopper is responsible for holding and feeding the granulated powders into the tablet press. It ensures a constant and regulated flow of materials.
- Feeder System: The feeder system precisely controls the flow of powder into the compression zone, ensuring accurate tablet weight and consistency.
- Punches and Dies: These are the tools responsible for shaping the tablets. The punches press down on the granulated powders, utilizing the dies to form tablets of specific dimensions.
- Compression Zone: The compression zone is where the actual compression of the powder into tablets occurs. The punches exert force on the powder, binding it together and forming tablets.
Types of Rotary Tablet Press Machines
There are three main types of rotary tablet press machines based on their design and functionality:
- Single-sided presses: These machines have one compression station and are suitable for small-scale production or research purposes.
- Double-sided presses: Double-sided presses feature two compression stations, allowing for increased production output. They are commonly used in medium to large-scale manufacturing.
- High-speed presses: High-speed rotary tablet press machines are designed to handle high-volume production requirements. They are capable of producing tablets at a rapid rate, ensuring optimal efficiency.
Advantages of Rotary Tablet Press Machines
Higher Production Output
One of the primary advantages of tablet press machines is their ability to significantly increase production output. These machines make lots of tablets quickly, so manufacturers can meet demand and keep quality. Rotary tablet press machines run nonstop, so production stays constant and efficient.
Consistent Tablet Quality
Achieving consistent tablet quality is essential for pharmaceutical companies. Rotary tablet press machines offer precise control over tablet weight, shape, and hardness, ensuring uniformity across the entire batch. Manufacturers can rely on these machines to deliver tablets that meet strict quality standards, bolstering their reputation in the market.
Increased Efficiency in the Tablet Manufacturing Process
Efficiency is a key factor in modern tablet production. Rotary tablet press machines streamline the manufacturing process by automating various stages, reducing manual labor, and eliminating repetitive tasks. This automation enhances efficiency, reduces the risk of errors, and enables manufacturers to optimize their production lines.
Factors Influencing Tablet Production Efficiency
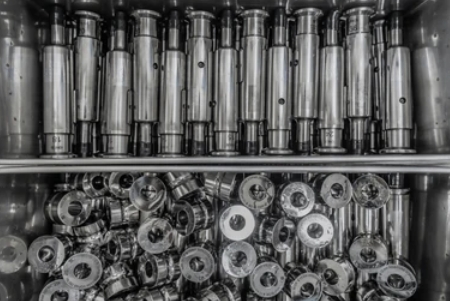
The Design of Automatic Feeder Systems
The efficiency of the feeding system significantly impacts tablet production. Rotary tablet press machines have automatic feeder systems for a smooth flow of powders. This prevents clogging and material irregularities.
Pre-Compression Options
Pre-compression is a crucial step in the tablet manufacturing process. It involves applying a low force to remove air and ensure uniform powder distribution before the main compression stage. Rotary tablet press machines equipped with pre-compression options enhance tablet quality and reduce the risk of defects such as lamination.
Right Tooling System
The tooling system of a rotary tablet press machine plays a crucial role in tablet production efficiency. Choosing the right punches and dies makes tablets more consistent in weight, reduces waste, and improves their strength.
Powder Flow Properties
The flow properties of the raw materials used in tablet formulation directly impact production efficiency. Powders with poor flowability may lead to problems such as powder bridging or erratic tablet weights. By selecting materials with excellent flow properties, manufacturers can optimize tablet production and minimize downtime.
Tensile Strength Requirements
Tablets must possess the required tensile strength to withstand various handling, transportation, and packaging processes. Choosing the right ingredients for tablet formulas makes sure the tablets stay strong and durable. This is important for the tablets to last a long time.
Lubricant Selection
Lubricants are essential in tablet manufacturing as they prevent sticking and ensure smooth tablet ejection from the punches and dies. Choosing and using the right lubricants helps make tablet production efficient by preventing delays and ensuring consistent quality.
Optimizing Tablet Production with Rotary Tablet Press Machines
Controlling Tablet Weight Variation
Controlling tablet weight variation is crucial for maintaining consistent tablet quality. Tight weight control ensures that each tablet contains the specified amount of active ingredients, meeting regulatory requirements. Manufacturers can achieve this by implementing accurate feeder systems and precise dosing techniques.
Ensuring Uniform Tablet Hardness
Uniform tablet hardness is vital to prevent issues such as capping, chipping, or tablet breakage during handling. Proper pre-compression and compression techniques, as well as tooling alignment, contribute to achieving uniform tablet hardness.
Minimizing Tablet Disintegration Time
Tablet disintegration time is a critical factor in drug release and absorption. By optimizing formulations and compression parameters, manufacturers can minimize disintegration time, enabling the tablet to deliver the medicine more effectively.
Tablet Press Set-up and Maintenance
Proper tablet press set-up and regular maintenance are essential for achieving optimal tablet production efficiency and prolonging the machine’s lifespan. Key considerations include:
Correct Alignment of Tooling Components
Regular inspection and alignment of tooling components such as punches and dies are crucial for minimizing tablet defects and ensuring consistent tablet quality. Misalignment can result in weight variation, inconsistent tablet hardness, and reduced tablet integrity.
Regular Cleaning and Lubrication
Cleaning and lubricating the tablet press are essential maintenance tasks. Regular cleaning prevents cross-contamination between different products, while proper lubrication reduces friction and wear, ensuring smooth operation and extending the machine’s lifespan.
Routine Inspections and Adjustments
Routine inspections of the tablet press machine allow manufacturers to identify potential issues before they affect production. Adjustments such as tightening loose screws, replacing worn-out parts, and calibrating the machine’s settings contribute to consistent production and prevent unexpected downtime.
Common Tablet Press Problems and Solutions
Even with proper maintenance and optimization, tablet press problems can still occur. Understanding and addressing these issues promptly is crucial to minimizing production disruptions. Some common problems include:
Tablet Sticking and Picking Issues
Tablet sticking occurs when the tablet adheres to the punch face or the die wall, resulting in poor tablet quality and potential equipment damage. Proper selection and application of lubricants, as well as adjusting compression force and dwell time, can mitigate this issue.
Capping or Lamination Problems
Capping and lamination refer to the separation of tablet layers or breaking of the tablet edges during compression or ejection. These issues can arise from problems such as inadequate binding, improper powder distribution, or excessive air entrapment. Adjusting formulation parameters and optimizing compression settings can help resolve these problems.
Chipping or Capping of Tablet Edges
Chipping or capping of tablet edges can occur due to excessive compression force, uneven powder distribution, or inadequate lubrication. Adjusting compression parameters, enhancing tooling alignment, and optimizing lubrication techniques can minimize these defects.
Preventive Measures for Consistent Production
To maintain consistent production and prevent issues, manufacturers must implement several preventive measures throughout the production process:
Quality Control Checks Throughout the Process
Regular quality control checks at various stages of tablet production, including material testing, in-process inspections, and final product analysis, ensure that tablets meet the required specifications. These checks identify deviations early on, allowing for prompt corrective actions.
Regular Maintenance Schedules
Adhering to regular maintenance schedules is crucial for preventing unexpected breakdowns and ensuring consistent and efficient tablet production. Scheduled maintenance tasks may include cleaning, lubrication, part replacement, and performance verification.
Operator Training and Standardization
The expertise and knowledge of machine operators significantly impact tablet production efficiency. Proper training regarding machine operation, maintenance techniques, troubleshooting, and adherence to standardized operating procedures is essential for minimizing errors and maximizing productivity.
Conclusion
Revolutionize tablet production with rotary tablet press machines, manufacturers can significantly boost production output and improve tablet quality. Understanding the intricate details of these machines, optimizing production processes, troubleshooting efficiently, and embracing industry trends and future innovations are key to achieving efficient tablet production. By harnessing the power of rotary tablet press machines, manufacturers can stay at the forefront of the industry, meeting increasing demands while maintaining high-quality standards. Embrace the revolution in tablet production and embrace a future of enhanced efficiency and innovation.