- Home
- Blister Card Packing Machine
Blister Card Packing Machine
Blister card packing machine, often called cardboard packaging machine or blister card machines, automate the process of securely sealing products to pre-printed paperboard cards, typically combined with clear alu pvc blister, alu alu blister, or formed plastic trays. The main function is to protect the blister plate from being damaged. Key applications span diverse industries: pharmaceuticals (tablets, capsules), consumer goods (toys, electronics accessories, batteries), hardware & tools (fasteners, small hand tools), health & beauty (razors, cosmetics, oral care) and automotive parts. These machines efficiently handle product loading, card folding, blister sealing (heat or ultrasonic), and final closure. They are essential for creating tamper-evident, shelf-appealing packaging that enhances brand presence, provides product information, and protects items during shipping and handling. Ideal for medium to high-volume production of durable and display-oriented packages.
Application:
Paper card packing machine can pack tablet blisters, capsule blisters and other items.

Working Principle
Paperboard Packaging Machine uses an automated process to place the blister sheet containing the tablets between two cardboards and then seals them, mainly to protect the blister sheet from being damaged.
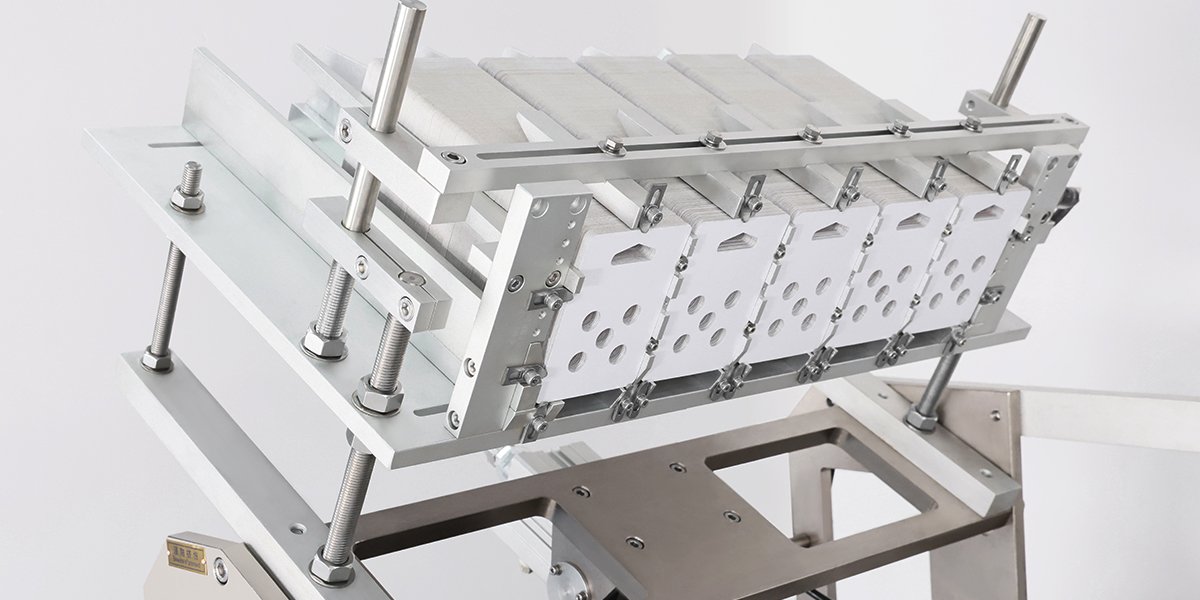
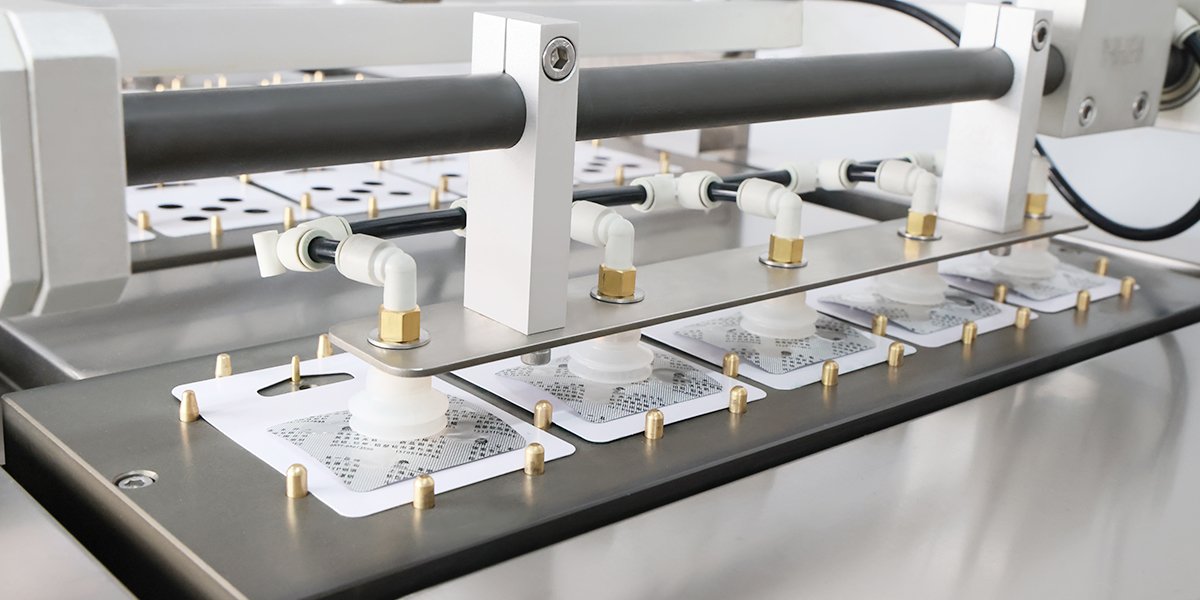
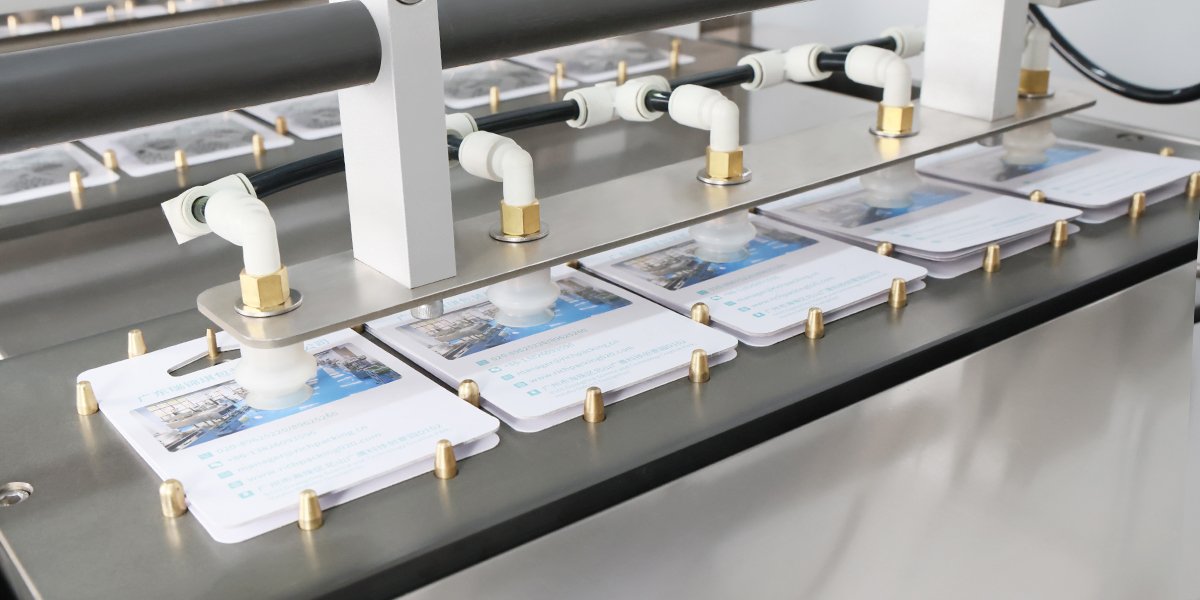
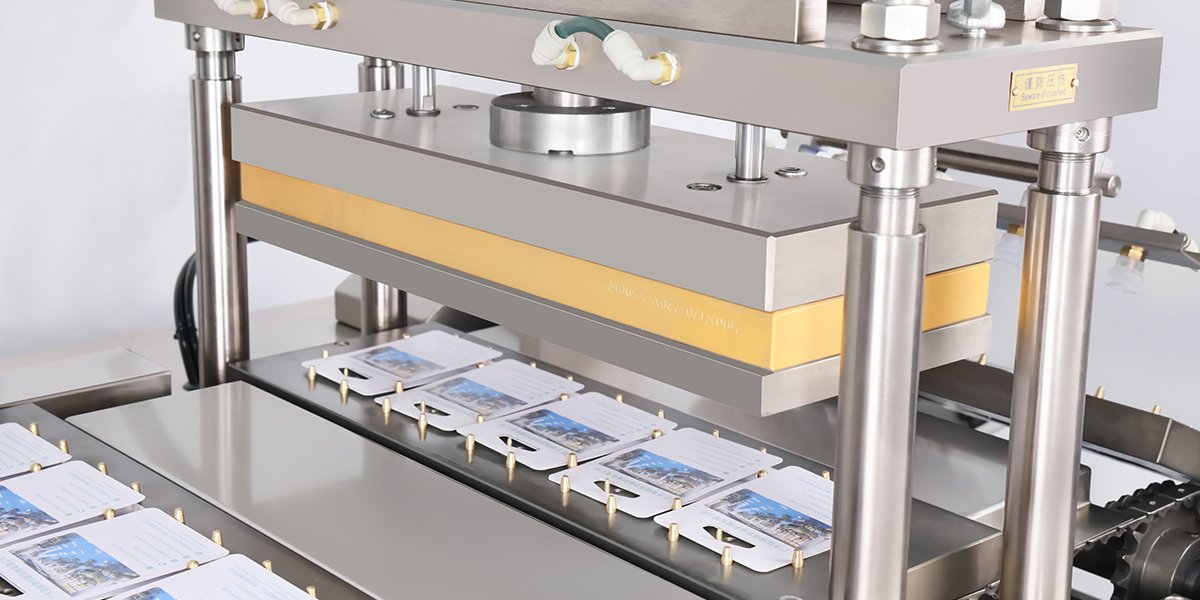
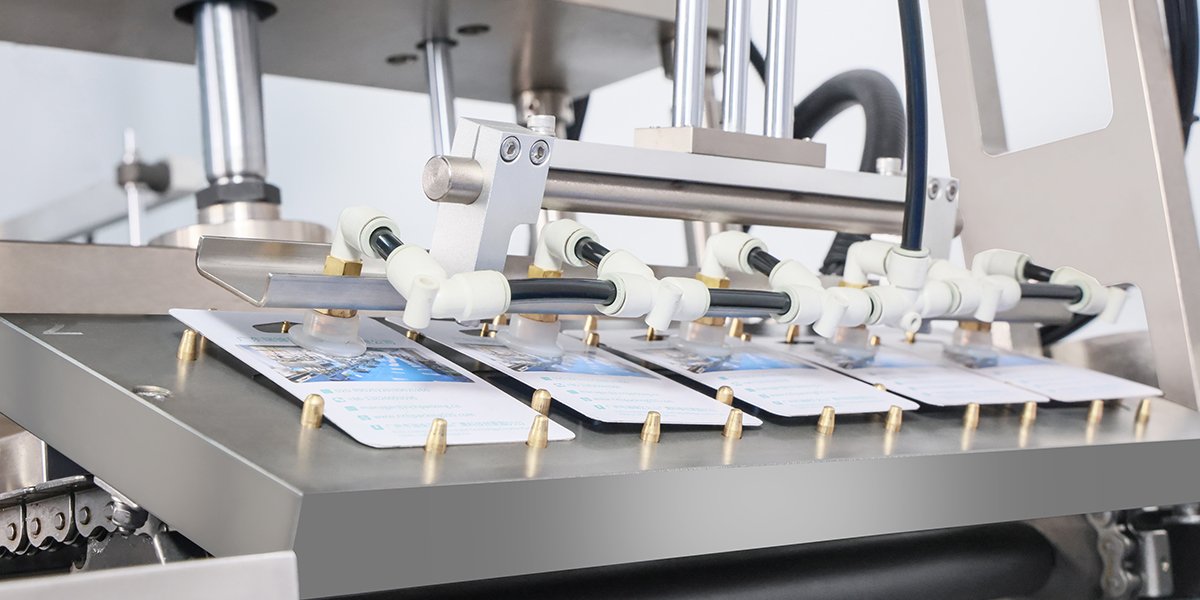
Technical Parameters
Choose the best machine according to the size of the pouches.
Machine Mold | RD-BCP-350Pro | RD-BCP-500Pro | RD-BCP-650Pro |
Production Capacity | 3,600 Plates/h | 5,400 Plates/h | 6,400 Plates/h |
Max. Forming Area | 330*210*65mm | 470*220*65mm | 630*220*65mm |
Paper Card Size | 350*220*0.5mm | 500*300*.05mm | 650*300*0.5mm |
Total Power | 11.8 kW | 12.8 kW | 15.8 kW |
Supporting Products
NJP-3800D Automatic Capsule Filling Machine
NJP-3800D automatic capsule filling machine works by automatically feeding empty capsules, filling them with powder, closing, and output for packaging.
Blister Packing Machine Manufacturer
Blister packing machine manufacturer offer various type machines that boosts output while lowering labor costs and material waste.
Tablet Compression Machine
Tablet compression machine is essential equipment for producing solid tablets by compacting powdered or granular materials.
Fortune 500 Quality Supplier
Features Advantage
Ruidapacking are committed to manufacture machines with superior quality to meet GMP standards while with efficient and utility features.
Full Servo Control
The stroke can be accurate to 0.1mm, which is convenient for the alignment of paper cards and aluminum-plastic panels. The adjustment of the pulling distance of the product can be completed with one click on the touch screen.
Stronger Pressure Resistance
The heat sealing station mold is treated with Teflon, with better surface smoothness and pressure exceeding 100 kN.
Hard Anodized Molds
The 28-piece mold is made of high-grade aluminum alloy, the draw-out slot design allows mold changes within 15 minutes.
We've Got Your Back with Comprehensive Service
Stand by you through the whole process, from choosing the suitable machine to taking good care of it for life.
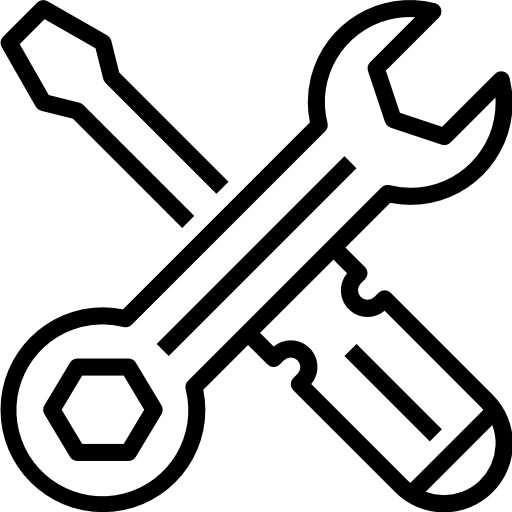
Life-time Guarantee
To ensure premium performance for a long time, we offer free repairment within 3 years and free spare parts within 1 year. After that, we promise a free technical consultation for a lifetime.
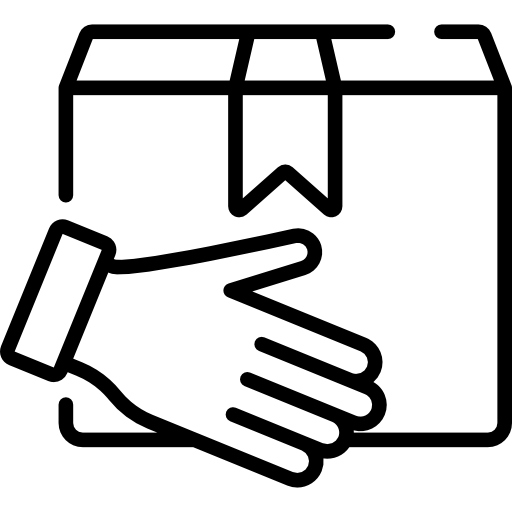
Fast Delivery in 7 Days
95% of our standard machines are in stock. In such case, the shipping can arrive within 7 days. As for in-depth customized products, it is only 20 days for delivery.
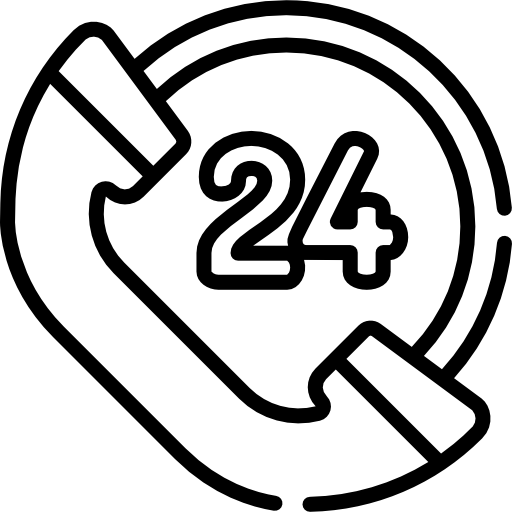
Online Service
Our knowledgeable customer experts and engineers will target your needs and solve all your problems within 24 hours, including but not limited to question answering, remote video.
Frequently Asked Questions
Finding a truly reliable pharmaceutical blister card packaging machine can be a major headache for manufacturers. Common frustrations like poor sealing, product misalignment, and electrical safety concerns lead to wasted materials, rejected batches, operational downtime, and compliance risks. At Ruidapacking, we engineer our blister card machines to eliminate these exact problems, ensuring consistent quality, maximum efficiency, and uncompromised safety. Discover how our precision design solves the industry’s top three paper card packaging challenges.
1. Weak Sealing & High Reject Rates
The Industry Pain Point: Many blister card machines struggle with inconsistent or weak heat sealing. This results in blister packs detaching from the paperboard, compromised product integrity, and unacceptably high reject rates – directly hitting your bottom line through wasted materials and lost production time.
The Ruidapacking Solution: Our machines feature a heavy-duty heat sealing station engineered for perfection:
Massive, Controlled Pressure: We apply over 100 kN (10+ tons) of precisely calibrated pressure across the sealing area.
Premium Teflon-Coated Tooling: Sealing surfaces feature advanced Teflon (PTFE) coating, ensuring exceptional smoothness, consistent heat distribution, and preventing material sticking.
Result: Bonds are exceptionally strong and uniform every time. Dramatically reduced reject rates protect your profitability and ensure batch consistency.
2. Misaligned Cards & Poor Aesthetics
The Industry Pain Point: Achieving perfect alignment between the top and bottom paperboards is critical. Misaligned cards look unprofessional, can hinder functionality (e.g., hang holes blocked), and lead to consumer complaints or retailer rejections. Manual adjustments are time-consuming and often ineffective.
The Ruidapacking Solution: Precision alignment is built into our core design:
Dowel Pin Positioning System: We utilize a robust dowel pin location system within the tooling.
Guaranteed Registration: This system securely fixes each paperboard in its exact correct position on the mold before the heat sealing station begins.
Result: Perfect, consistent overlap of top and bottom cards every single cycle. Your finished packs look professional, function flawlessly, and meet the highest aesthetic standards.
3. Electrical Safety Hazards
The Industry Pain Point: Concerns about electrical safety, including potential leakage currents or unreliable components, are serious. These hazards endanger operators, violate strict cGMP and workplace safety regulations (like CE, UL), and create significant liability risks. Downtime for electrical repairs is costly.
The Ruidapacking Solution: Safety and reliability are non-negotiable:
World-Class Electrical Components: We exclusively integrate premium, globally recognized electrical brands (e.g., Siemens, Schneider Electric) known for their reliability and stringent safety certifications.
Robust Wiring & Grounding: Our machines are built with high-grade wiring harnesses and meticulous grounding practices exceeding international safety standards.
Result: Operators work with confidence. You achieve full compliance with cGMP and essential safety directives (CE marked), eliminate electrical hazard risks, and benefit from drastically reduced electrical failure downtime.
Conclusion
Stop battling unreliable blister card machines that compromise your quality, efficiency, and safety. Ruidapacking’s pharmaceutical paper card packaging machines are engineered from the ground up to solve the most persistent problems plaguing the industry. Our commitment to robust construction (100kN+ sealing), precision alignment (dowel pin system), and absolute electrical safety (premium components) delivers:
Higher Profitability: Slash reject rates and minimize costly downtime.
Flawless Quality: Guarantee perfectly aligned, professionally sealed packs.
Uncompromised Safety & Compliance: Meet cGMP and stringent electrical safety standards with confidence.
Within pre-made pouch packaging lines, the core decision of selecting a multi-head weigher or tablet capsule gummy counting machine as the supporting equipment hinges on the attributes of the material being handled. These two technologies offer distinct advantages and are suited to specific applications. Selecting the wrong machine can lead to compromised efficiency, insufficient accuracy, high material waste, or even operational failure.
The selection criteria, strengths, and limitations of each device are analyzed in detail below, based on key material characteristics:
1. Material Properties
Physical Form
Granules, Flakes, Sticks, Chunks(Regular/Irregular Solids): Both multihead weigher and counting filling machine are possible options; final selection depends on other properties.
Fine Particle: Typically better suited for counting machine.
Powders, Pastes, Liquids, Viscous Materials: Neither multi-head weigh filler nor automatic counting machines are suitable. These require volumetric filling equipment (Auger Fillers, Piston Fillers, Liquid Fillers) or net weight scales.
Individual Weight/Size
Large & Relatively Uniform Individual Weight: (Large Biscuits, Chocolate Bars, Whole Fruit, Toy Parts) Multi-head combination weighers generally offer advantages in efficiency and cost-effectiveness.
Very Small or Highly Variable Individual Weight: (Small Pills, Seeds, gummy bear, Small Hardware) Automatic electronic counting machines excel in precision and minimizing waste. Multi-head weighers struggle with accuracy control for very lightweight items, and small items are prone to loss through “fly-away” (aeration) within the weigh buckets during operation.
2. Multi-Head Weighers
Material is distributed from a main vibration feeder into multiple (typically 8-24) independent weigh buckets (weigh hoppers). A computer system continuously reads the weight in each bucket and uses a combination weighing algorithm to rapidly identify the group of buckets whose combined weight is closest to the target weight. The selected buckets discharge simultaneously into a collection funnel below, directing the material into the packaging pouch.
Advantages
High Speed: The combination weighing principle enables exceptionally high weighing speeds (typically 100-200 pouches/minute, with high-speed models exceeding 300 pouches/minute), making it the preferred choice for maximizing production output.
High Accuracy: For free-flowing materials with moderate individual weights, multi-head weighers achieve very high weighing accuracy (±0.1g to ±1g or better, depending on material and target weight). The combination algorithm effectively compensates for individual feed variations.
Broad Weight Range: Capable of handling packaging specifications ranging from a few grams to several kilograms by adjusting the target weight and bucket size, offering strong adaptability.
Ideal for Free-Flowing Materials: Processes granules, flakes, chunks, and other free-flowing materials smoothly and efficiently.
Relatively Easy Cleaning & Maintenance: Features a relatively standardized structure; parts contacting the material (vibration feeder, buckets) are typically detachable for cleaning.
Disadvantages
Struggles with Poorly Flowing Materials: Materials prone to sticking, clumping, being oily, or moist can easily clog in the vibration feeder, buffer hoppers, or weigh buckets, leading to uneven feeding, reduced accuracy, or even machine stoppage.
Challenges with Small/Very Light Materials: Extremely small or lightweight items (tiny seeds, small pills) are susceptible to airflow dispersion (“fly-away”) within the weigh buckets, causing material loss. Accuracy advantages also diminish for very small target weights.
Potential Damage to Fragile Items: The tumbling action in the vibration feeder and bucket discharge can cause impact and friction, potentially damaging very fragile products (potato chips).
Difficulty with Irregular/Entangling Materials: Long, flat, or stringy items can become entangled or jam in the vibration feeder tracks or bucket inlets.
Provides Weight, Not Count: Outputs a target weight, not an exact piece count. Unsuitable for applications requiring precise quantities ( items sold by unit count).
3. Electric Counting Machines
Count bottling machines isolate individual items using physical separation or vision recognition technology and count them. Common types include:
Counting and filling machine: Items queue on vibrating tracks and are counted via photoelectric sensors.
CCD camera inspection counting machine: High-speed cameras capture images of falling items, and image processing software identifies and counts individual units.
Advantages
Delivers Exact Piece Count: The only solution for applications requiring precise counts (pharmaceuticals, gummy bear, candy, electronic components).
Superior Handling of Poorly Flowing Materials: Generally outperforms multi-head weighers in processing moist, oily, or sticky materials with reduced clogging risk.
Excels with Small Pellets: Ideal for high-precision, low-waste counting of small pills, seeds, and candies.
Handles Irregular Shapes Effectively: Advanced vision counters can accurately identify and count items with diverse and challenging geometries.
Low Material Loss: Counting typically avoids weigh bucket inversion, minimizing loss from “fly-away” or product residue.
Low Noise: Fewer vibratory components compared to multi-head weighers typically results in lower noise levels.
Disadvantages
Slower Speed: Absolute speed is generally lower than multi-head weighers (especially for tiny items). High-speed vision counters may reach 100-150 pcs, but this translates to lower packaging speeds (60-90 pouches/minute for 100 piece packs) compared to high-speed weighers.
Weight Accuracy Depends on Unit Uniformity: Counting accuracy is 100%, but package weight accuracy relies entirely on consistent individual item weight. Significant weight variation (irregular-sized dried fruits, nuts) causes large package weight fluctuations.
Sensitivity to Item Clumping: If two or more items stick together and are counted as one, under-counting occurs. (Solution Example: Our specialized candy counter tackles clumping via 4 key features:)
Spiked Hopper Agitator: Prevents gummies from stacking vertically.
Anti-Clumping Distribution Roller: Ensures even batch dispersion by preventing adhesion.
Teflon Dimple Panels: Fully separate gummies and enable smooth, fast sliding.
Enlarged PTFE Discharge Port: Reduces clogging, increasing speed by 58%.
Complex Equipment Selection: Different counter types vary significantly in material suitability, requiring expert knowledge and testing for optimal selection.
High Cost of Vision Counters: Initial investment for high-performance vision counting systems can be substantial, often exceeding multi-head weigher costs.
Limited Capability for Large/Heavy Items: Counting very large chunks (whole chocolate bars, large toys) is often structurally impractical, slower, and less cost-effective than using multi-head weighers.
4. Summary & Equipment Selection Guide
Feature | Recommend Multi-Head Weigher | Recommend Auto Counting Machine |
Core Requirement | Target weight is the priority; pursue maximum speed & efficiency | Precise piece count is essential; or material properties make weighing unsuitable |
Material Flowability | Good(Dry, free-flowing) | Poor/Average(Oily, moist, sticky, prone to bridging) |
Material Form | Primarily granules, flakes, chunks | Primarily fine particles, micro-pellets, irregular shapes, flat, elongated items |
Individual Weight | Medium to large, or small but uniform particles | Very small, or items with high weight variation requiring piece counting |
Packaging Accuracy | High weight accuracy(±0.1g – ± 1g) | 100% count accuracy (Weight accuracy depends on individual piece uniformity |
Speed | Very High(100-300+ pouches/minute) | Medium-High(Depends on item size & counting tech; typically lower than weighers |
Applications | Snacks (potato chips/nuts/candy), frozen food, pet food, coffee beans, hardware, chemical granules | Pharmaceuticals (tablets/capsules), supplements, seeds, gummy candy, electronic components, high-value items sold by count |
5. Best Practice Recommendations for Supporting Products Selection
Conduct Rigorous Material Testing: Submit actual material samples to ruidapacking for testing. See firsthand the equipment’s processing capabilities, accuracy, speed, and material loss with your specific product.
Plan for Future Production Needs: If you might package materials with different properties in the future, prioritize equipment with compatibility or flexibility to handle diverse products.
Ensure Seamless Production Line Integration: Guarantee your chosen dosing equipment integrates smoothly with both upstream feeding systems (elevators, storage bins) and the downstream packaging machine.
Match performance: Verify compatibility in speed and mechanical/physical interfaces to prevent bottlenecks.
Prioritize Supplier Support & Service: Select a supplier with strong technical expertise and a proven track record of responsive, high-quality after-sales service and support.
By carefully evaluating your material’s key properties and thoroughly understanding the core strengths and limitations of multi-head weighers and automatic bottle counting machines, you can confidently select the most suitable, efficient, and cost-effective dosing solution for your pre-made pouch packing line.
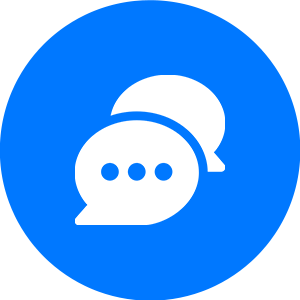