Maintaining automatic tablet press machine is crucial for ensuring its longevity, optimal performance, and consistent production quality. Regular maintenance not only prevents unexpected breakdowns but also ensures that the automatic pill press machine operates at peak efficiency, thus maintaining product quality and compliance with regulatory standards. This comprehensive guide will walk you through the best practices for maintaining your pill press machine automatic, including daily, weekly, and monthly maintenance routines, troubleshooting tips, and the importance of staff training.
Understanding the Importance of Maintenance
Before diving into the specifics of maintenance, it’s essential to understand why maintaining your tablet press machine is vital:
1. Enhanced Performance: Regular maintenance ensures that all components of the rotary tablet press machine are functioning correctly, which enhances overall performance and efficiency.
2.Consistency in Quality: A well-maintained tablet making machine produces tablets of consistent size, shape, and weight, which is crucial for dosage accuracy.
3.Reduced Downtime: Preventative maintenance helps identify small issues before they become big problems, reduce the possibility of tablet press downtime.
4.Longevity: Proper care and maintenance extend the life of the machine, providing a better return on investment.
5.Compliance: Regular maintenance ensures that the machine operates within the regulatory standards set by health authorities.
Daily Maintenance Checklist
Daily maintenance is indispensable for tablet press machine very important. The following is our daily routine:
1.Cleaning:
Exterior Cleaning: Wipe down the exterior surfaces of the machine with a clean, lint-free cloth to remove dust and debris.
Interior Cleaning: Clean the die table, turret, and punch guides to prevent powder build-up. Use industrial vacuum cleaner to remove excess powder from the turntable.
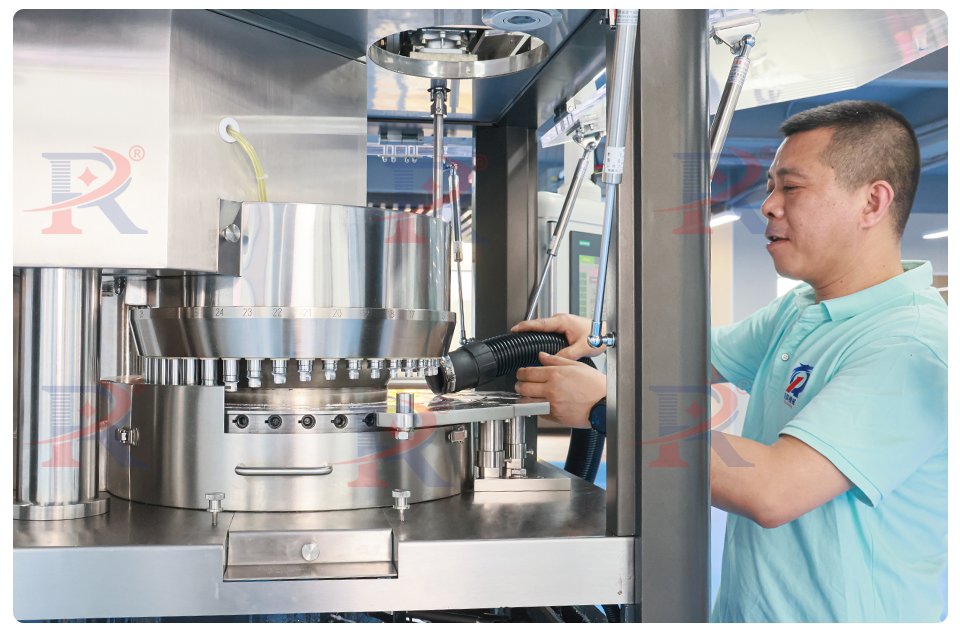
Lubrication: Apply food-grade lubricant to the upper molds, lower molds, bearings and other positions, and operate slowly. Be careful not to apply too much grease, this may cause some of the powder to stick to it and make it harder to clean.
2.Inspection:
Visual inspection: Check whether the molds, turntable, etc. have wear, cracks, chips or deformation.
Operational Check: Run the machine for a few minutes and listen for any unusual noises or vibrations. These could indicate a problem with the machine.
3.Calibration:
Tablet Weight: Check the weight of a few sample tablets to ensure they meet the desired specifications. If necessary, adjust the machine settings.
Tablet Hardness: Measure the hardness of the tablets and make adjustments if needed to ensure they meet the required standards.
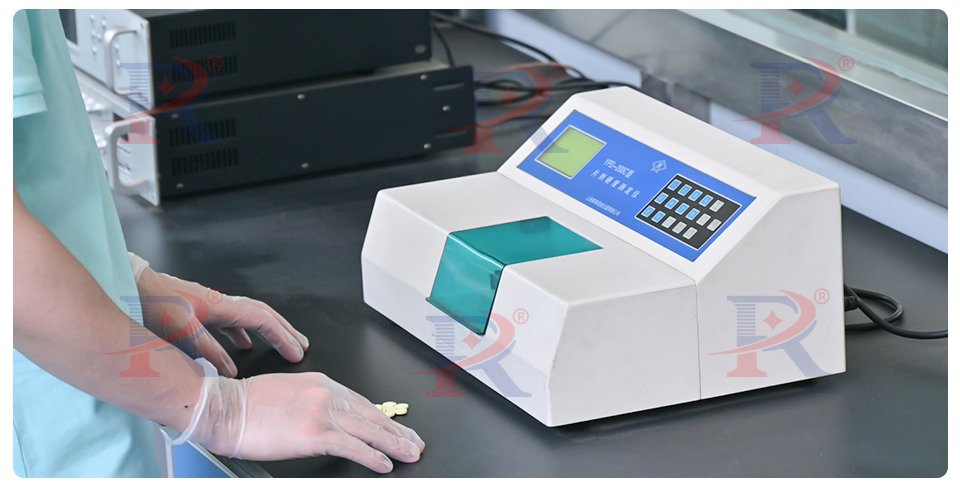
4.Operation records:
Record manual: Keep a record manual to record the operator’s actions, problems found and solutions taken, so as to facilitate how to solve the same problem next time it occurs.
Weekly Maintenance Checklist
Weekly maintenance involves more detailed inspections and tasks to keep the tablet press machine running smoothly:
1.Thorough Cleaning:
Disassemble Components: Disassemble the turret, punches, and dies for a more thorough cleaning. Use alcohol or pure water to clean each component, wipe and disinfect, dry and install correctly.
Check for Residue: Inspect the feed frame and hopper for any powder residue and clean them thoroughly.
2.Inspection and Replacement:
Punches and Dies: Inspect the punches and dies for wear and replace any that show significant signs of damage or wear. Using worn punches can lead to poor tablet quality and machine damage.
Turntable: Check the turntable for wear. Make sure it running stably and the noise < 75dBA.
3.Lubrication:
Cam Tracks: Lubricate the cam tracks with a suitable lubricant. Ensure that the grease does not cause secondary contamination to the tablets.
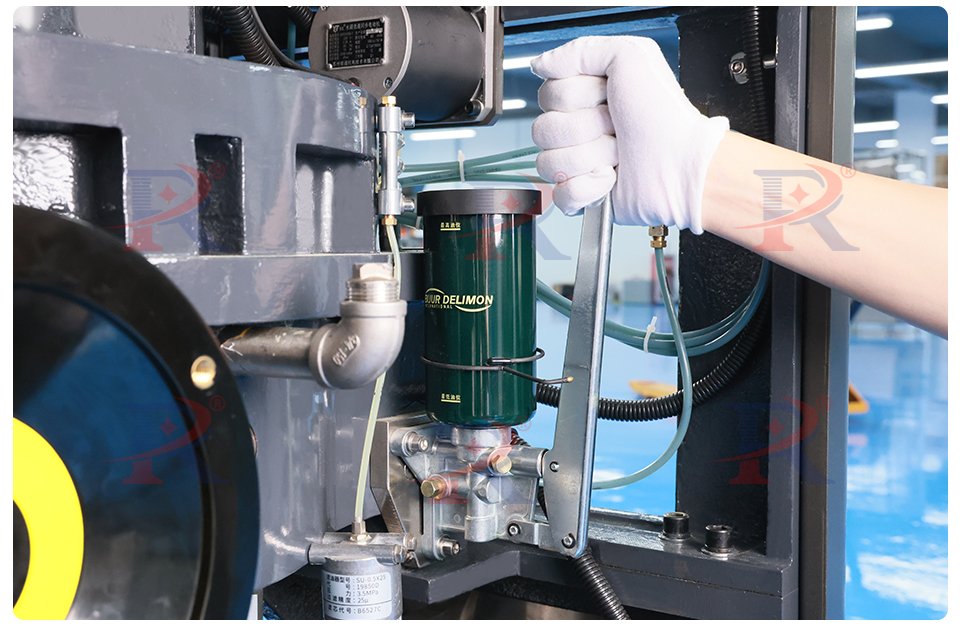
Bearings: Apply lubricating oil to all bearings to avoid wear caused by long-term work.
4.Alignment Check:
Punch Alignment: Ensure that the punches are correctly aligned with the dies. Misalignment can cause tablet defects and machine damage.
Feeder Alignment: Check the alignment of the feeder mechanism to ensure consistent and accurate filling of the dies.
6.Electrical Components:
Electrical cabinet circuit inspection: Check whether the electrical cabinet circuit is worn or the connection is loose, if so, replace it immediately.
Sensor Check: Test all sensors to ensure they are functioning correctly. Faulty sensors can lead to operational errors and safety hazards.
Monthly Maintenance Checklist
Monthly maintenance involves comprehensive checks and potential part replacements to ensure long-term reliability:
1.Deep Cleaning:
Machine Interior: Perform a deep cleaning of the machine’s interior components. Remove excess powder from the turntable.
Air filter: Clean or replace the filter element to ensure that the machine is well ventilated.
2.Detailed Inspection:
Worn parts: Check the bearings, rollers and spring parts. Replace the seriously worn parts to ensure the smooth running of the machine.
Gaskets and Seals: Check gaskets and seals for wear or damage and replace as necessary to prevent leaks and contamination.
3.Calibration:
Pressure Calibration: Calibrate the compression force settings to ensure consistent tablet hardness and weight.
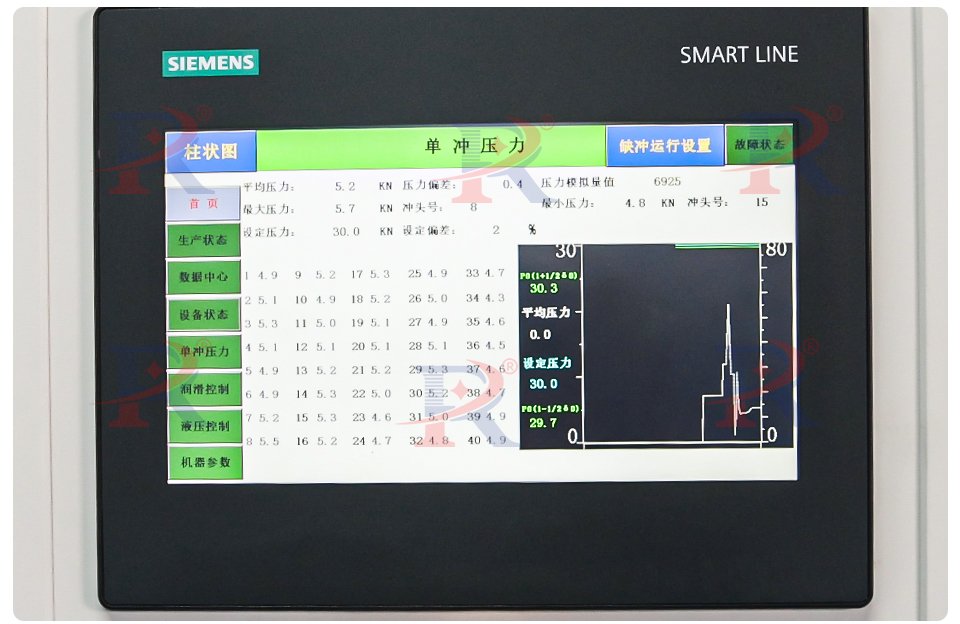
Control Systems: Verify that all control systems and software are functioning correctly. Update software if necessary to ensure optimal performance.
4.Safety Checks:
Emergency Stop: Test the emergency stop button to ensure it functions correctly. Regularly testing safety features is crucial for operator safety.
Guarding: Inspect all machine guards and safety interlocks. Make sure tablet press machine running stable.
5.Performance Testing:
Run Test Batches: Produce a test batch of tablets and evaluate their quality. Check for consistency in weight, hardness, and appearance.
Adjustment: Adjust the machine according to the test results of the tablet.
Troubleshooting Common Issues
Even with regular mainten, tablet press problems can occur. Here are some common problems and solution:
1.Tablet Weight Variation:
Cause: Inconsistent fill levels or worn punches/dies.
Solution: Check and adjust the fill mechanism. Inspect and replace worn punches and dies.
2.Tablet Capping or Lamination:
Cause: Incorrect compression force, improper granule formulation, or worn punches.
Solution: Adjust the compression force, review the granule formulation, and inspect the punches for wear.
3.Sticking and Picking:
Cause: Excessive moisture, insufficient lubrication, or dirty punches.
Solution: Ensure proper environmental controls, apply a suitable lubricant, and clean the punches regularly.
4.Machine Jamming:
Cause: Foreign objects, improper punch alignment, or worn parts.
Solution: Remove any foreign objects, realign the punches, and replace worn parts.
5.Noisy Operation:
Cause: Lack of lubrication, worn bearings, or misaligned components.
Solution: Apply lubrication, replace worn bearings, and inspect all components.
The Importance of Staff Training
Proper maintenance of an automatic tablet press machine also relies on well-trained staff. Here are some key aspects of staff training:
1.Regular Training Sessions: Conduct regular training sessions for your maintenance and production staff.
2.Detailed Manuals: Provide detailed manuals and documentation for the machine. This should include maintenance schedules, troubleshooting guides, and contact information for technical support.
3.Safety Training: Emphasize the importance of safety when performing maintenance tasks. Ensure staff are aware of the machine’s safety features and emergency procedures.
4.On-the-Job Training: Pair less experienced staff with seasoned operators and maintenance personnel for on-the-job training.
Maintaining an automatic tablet press machine requires a combination of daily, weekly, and monthly routines, along with vigilant troubleshooting and staff training. By following the comprehensive maintenance checklists outlined in this guide, you can ensure your machine operates efficiently, produces high-quality tablets, and enjoys a long operational life. Remember, regular maintenance is an important step in the safe production of pharmaceutical production lines. For any specific concerns or advanced technical support, always consult the Ruidapacking engineer.