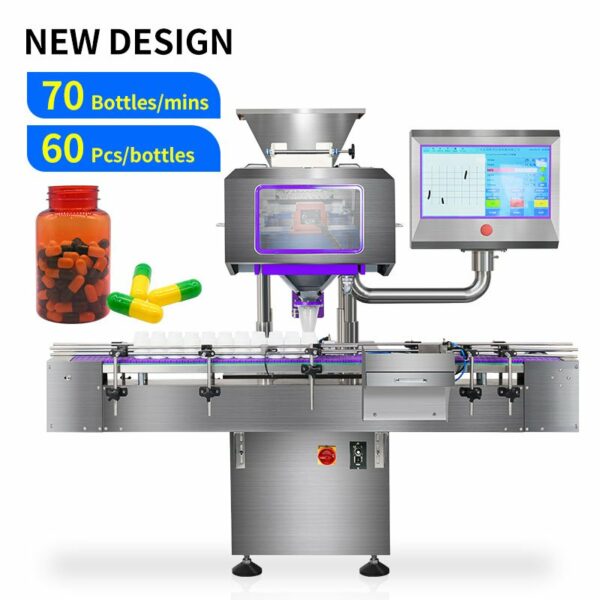
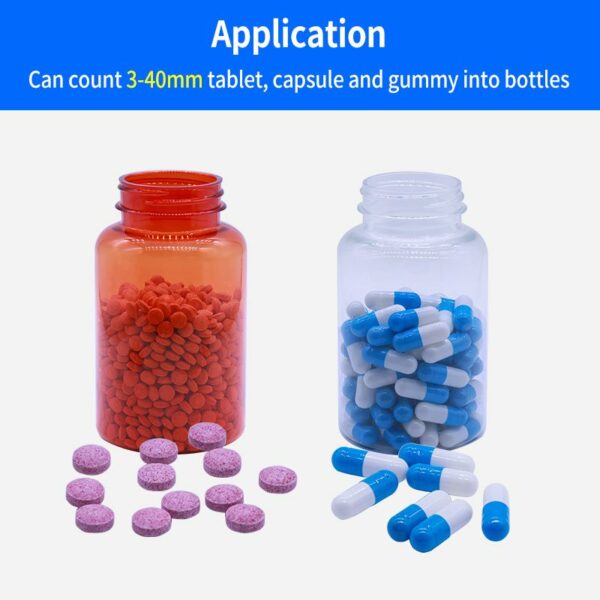
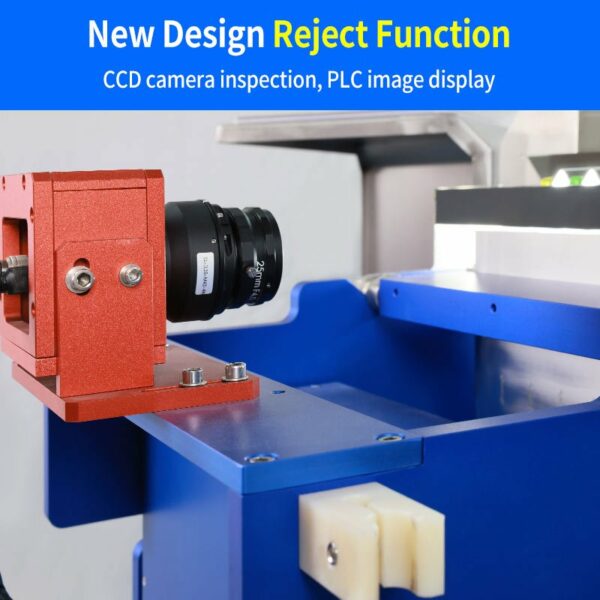
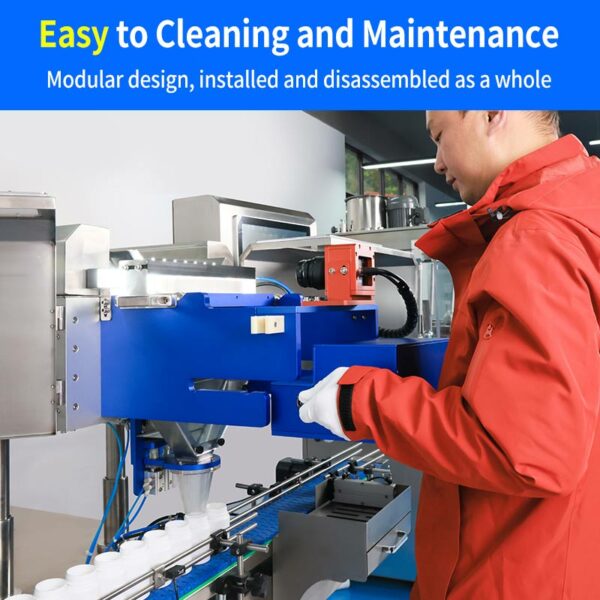
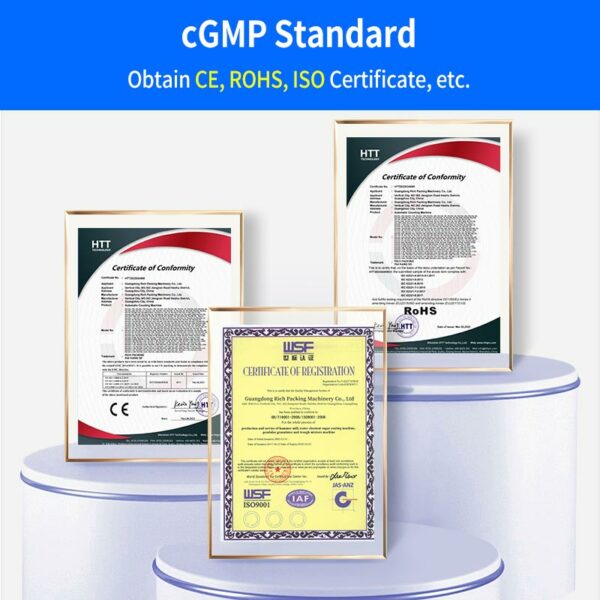
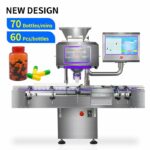
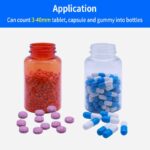
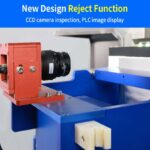
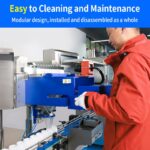
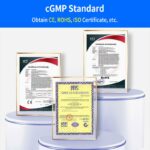
8 Lane Reject Inspection Count Bottling Machine
8 Lane reject inspection count bottling machine involves automated counting, detection, and rejection of incorrectly filled or defective bottles.
The product (tablets, capsules, soft gels, etc.) is fed into the machine using a hopper or conveyor system.
The counted items are then directed into a bottle or container. The filling process ensures that the correct number of products is placed in each bottle.
As bottles pass through the machine, sensors detect the position of each bottle to ensure it’s correctly aligned for filling.
After the products are counted and filled into the bottle, the machine uses sensors to verify the count. If the count is incorrect (either overfilled or underfilled), the bottle is flagged for rejection.
Bottles that do not meet the required specifications (e.g., wrong count, damage, contamination, etc.) are automatically removed from the production line.
Specification:
Up to 70 Bottles/mins
Accuracy rate 100%
Suitable for 3-40mm capsule/tablet/gummy…