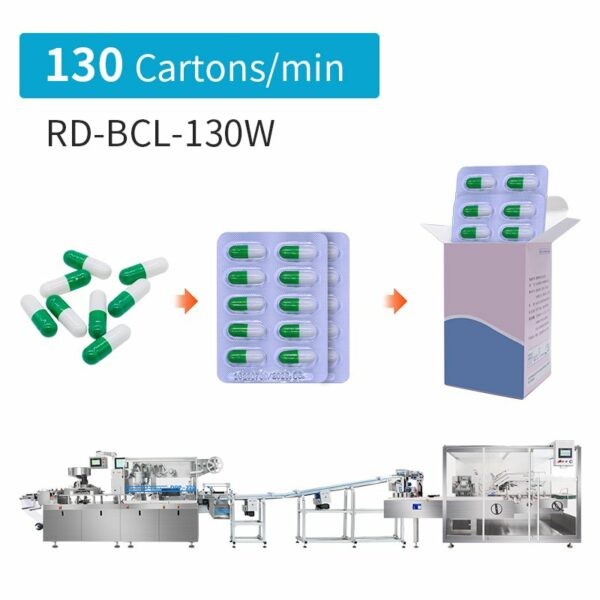
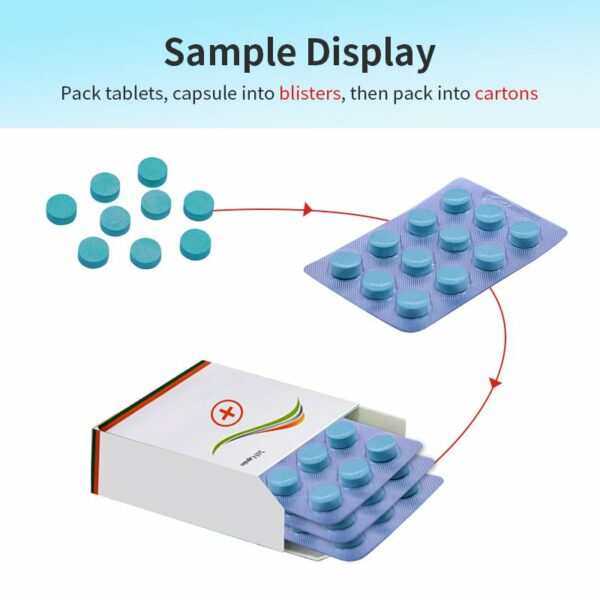
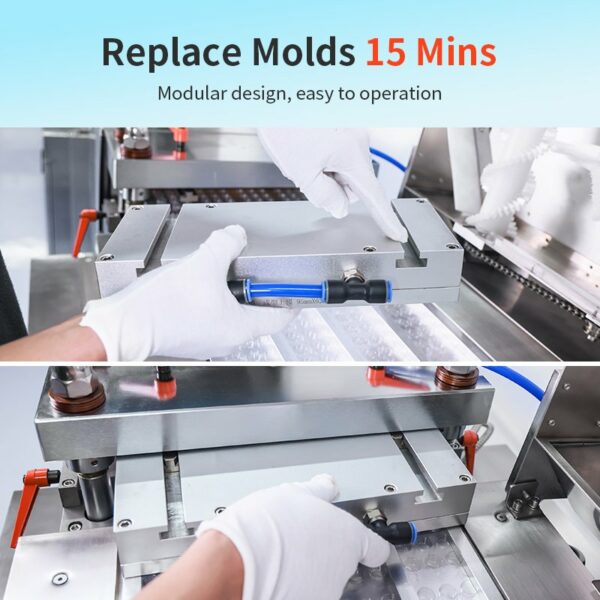
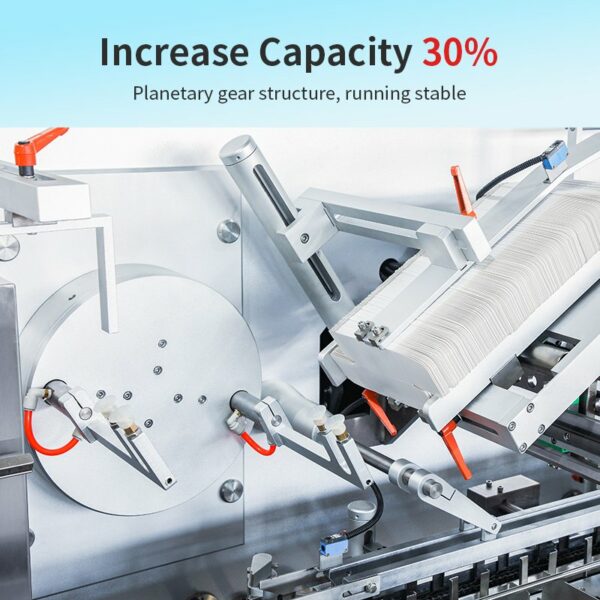
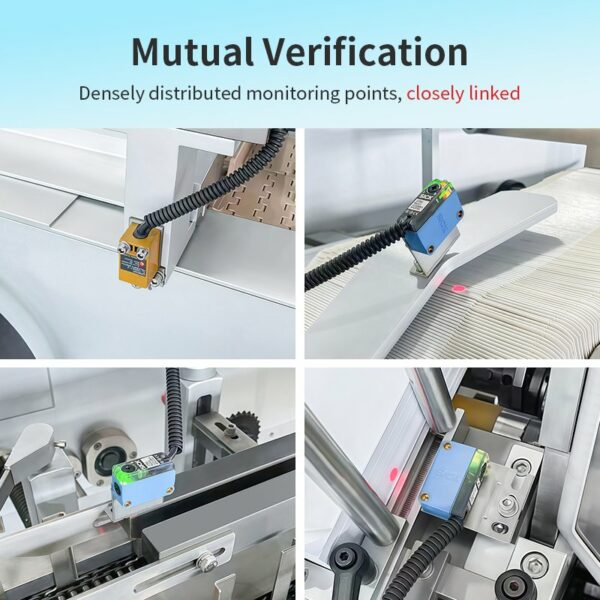
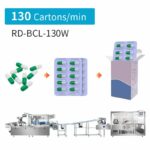
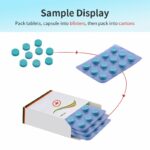
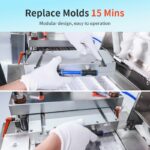
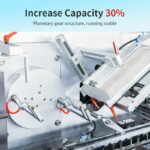
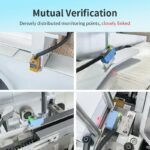
Blisterkartonier-Verpackungslinie
Die Blisterkartonieranlage automatisiert den gesamten Prozess der Blisterherstellung und des Befüllens der Kartons. Zunächst wird PVC thermogeformt und in Blistermulden eingebracht. Produkte (Tabletten, Kapseln) werden über kundenspezifische Zuführungen präzise in diese Blister eingefüllt. Anschließend wird der Blister unter Hitze und Druck mit Aluminiumfolie versiegelt, um Manipulationssicherheit zu gewährleisten.
Integrierte Bildverarbeitungssysteme prüfen auf Mängel wie leere Blister, falsch ausgerichtete Siegel oder fehlende Packungsbeilagen. Freigegebene Blister werden anschließend einem Kartoniermodul zugeführt. Dort werden vorgefaltete Schachteln aufgerichtet, mit Blistern und Beilagen (Anleitungen) befüllt und mit Einstecklaschen oder Klebstoff verschlossen. Aussortiermechanismen entfernen fehlerhafte Einheiten, während fertige Kartons zur Etikettierung oder Sekundärverpackung weitergeleitet werden.
Die Linie vereint Blisterformung, Versiegelung, Inspektion und Kartonierung in einem nahtlosen, cGMP-konformen Workflow und gewährleistet so eine schnelle Produktion, minimalen Abfall und die Anpassungsfähigkeit an unterschiedliche Produktgrößen. Sie ist ideal für Pharmazeutika, Lebensmittel und Konsumgüter und legt Wert auf Präzision, Hygiene und Skalierbarkeit.
Spezifikation:
Bis zu 130 Kartons/Minute
Geeignet für Tabletten, Kapseln, Pillen usw.
3 Jahre Garantie, 1 Jahr kostenlose Teile