Cos'è la macchina confezionatrice blister?
Confezionatrice blisteratrice Può confezionare in blister medicinali, miele e ketchup, sigarette elettroniche ecc., con un'area di stampaggio massima di 270x270 mm e una capacità produttiva massima di 30.000 blister/h. Può essere collegata a una comprimitrice, a una riempitrice di capsule e astucciatrice per formare una linea di produzione automatizzata ad alta efficienza.
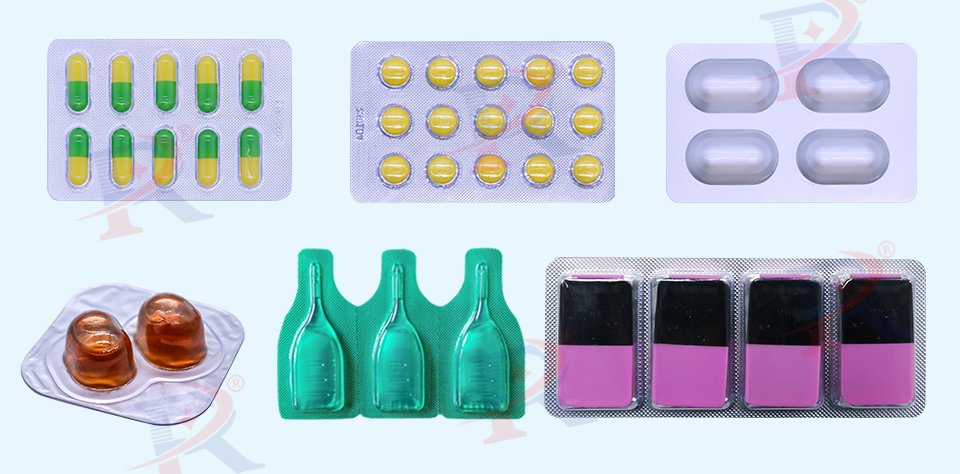
Tipo di macchina confezionatrice blister
In base al grado di automazione, le blisteratrici possono essere suddivise in confezionatrici manuali, confezionatrici a piastra piana e confezionatrici a rulli ad alta velocità. Il loro compito principale è caricare i materiali nei blister in alluminio-PVC o alluminio-alluminio per la successiva fase di confezionamento. La differenza tra l'imballaggio in alluminio-PVC e quello in alluminio-alluminio è la seguente: il materiale in alluminio-PVC è più economico, l'imballaggio in alluminio-alluminio può essere protetto dalla luce, e la scelta del metodo di confezionamento più adatto dipende principalmente dalle proprie esigenze.
Confezionatrice blister manuale
Confezionatrice blister manuale: è necessario completare manualmente una serie di azioni.
Preparativi preliminari: collegamento elettrico, collegamento gas, alluminio pvc, foglio di alluminio
Formatura: quando la temperatura raggiunge la macchina, impostare la temperatura di stampaggio, premere il pulsante di stampaggio, tirare manualmente il pvc di alluminio, stampando un tiro indietro un po'
Alimentatore: aggiungere le compresse o le capsule che si desidera confezionare nel blister stampato.
Saldatura a caldo: impilare il blister con le compresse e il foglio di alluminio sopra e sotto, premere il pulsante di saldatura a caldo, la macchina sigillerà automaticamente il blister.
Taglio: posizionare il blister in alluminio-pvc termosaldato sulla stazione di taglio, premere il pulsante di punzonatura e taglio e uscirà un blister in alluminio-plastica.
Macchina confezionatrice blister a piastra piana
Con il progredire dei tempi, la domanda di medicinali e prodotti sanitari è in aumento e, a causa della bassa produttività, le blisteratrici manuali non riescono più a soddisfare la domanda del mercato. Le blisteratrici a piastra piana sono diventate le macchine preferite per il confezionamento. Ecco il suo principio di funzionamento:
Preparazione: preparare le materie prime, indossare la pellicola, collegare il refrigeratore, collegare l'elettricità, collegare il gas, stampare, sigillare a caldo la temperatura della postazione di lavoro fino al valore impostato.
Alimentazione: per gli imballaggi in alluminio-PVC, si preferisce generalmente un alimentatore a spazzola, più economico; per gli imballaggi in alluminio-alluminio, si preferisce un alimentatore con guida per evitare graffi sulla lamina di alluminio. Inserire le compresse o le capsule nell'alimentatore, aprirlo e le compresse verranno inserite automaticamente nel blister.
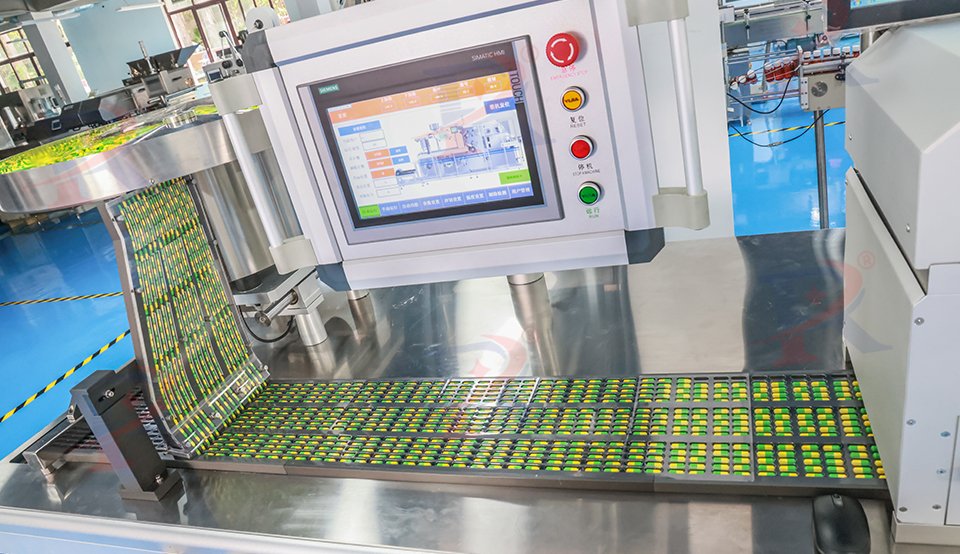
Tutti gli stampi possono essere personalizzati in base alle dimensioni e alla forma del materiale, con stampi per formatura, termosaldatura, punzonatura e taglio personalizzati. Dotati di sistema di controllo PLC Siemens, produzione automatizzata, nessun intervento manuale, aggiunta di materiale solo in caso di esaurimento.
La macchina blisteratrice per liquidi serve principalmente a mettere il liquido nel blister in alluminio e PVC; a seconda della viscosità del materiale si può scegliere un metodo di riempimento diverso: pompa a siringa, pompa peristaltica, pompa in ceramica, le altre stazioni sono le stesse della macchina confezionatrice blister in alluminio e PVC per pillole.
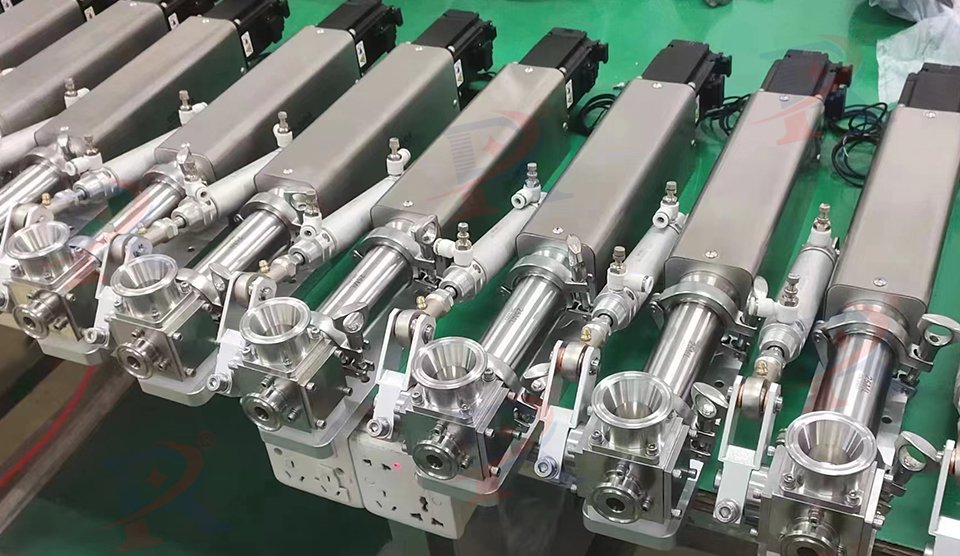
Macchina blister a rulli
La blisteratrice a rulli è un'apparecchiatura sofisticata progettata per il confezionamento efficiente di compresse, capsule e altri piccoli prodotti medicali in blister. Il principio di funzionamento di questa macchina prevede diverse fasi chiave, ciascuna delle quali garantisce il confezionamento preciso e affidabile dei prodotti farmaceutici. Ecco un'analisi approfondita del funzionamento di una blisteratrice a rulli:
Alimentazione del materiale: il processo inizia con l'alimentazione dei materiali di imballaggio. Tipicamente, vengono utilizzati due tipi di materiali: un film di base (solitamente PVC o foglio di alluminio) e un materiale di copertura (come il foglio di alluminio). Il film di base viene svolto da una bobina e immesso nella macchina, dove formerà le cavità per i prodotti. Anche il materiale di copertura viene svolto da una bobina separata e immesso nella macchina per la successiva sigillatura.
Riscaldamento e formatura: il film di base passa attraverso una stazione di riscaldamento dove viene riscaldato a una temperatura precisa, rendendolo flessibile e pronto per la formatura. Il film riscaldato viene quindi trasferito alla stazione di formatura, dove viene pressato contro un rullo con stampi a cavità. Vengono applicate tecniche di formatura sotto vuoto e/o a pressione, che consentono al film riscaldato di adattarsi alla forma degli stampi, creando tasche o blister in cui verranno posizionati i prodotti.
Alimentazione del prodotto: una volta formati i blister, la macchina trasporta il film di base alla stazione di riempimento. Qui, i prodotti farmaceutici vengono alimentati nelle singole cavità.
Saldatura: Dopo aver inserito i prodotti nei blister, la macchina sposta il film riempito alla stazione di saldatura. Il materiale di copertura viene posizionato sopra i blister riempiti ed entrambi gli strati vengono fatti passare tra rulli di saldatura riscaldati. I rulli applicano calore e pressione, saldando il materiale di copertura al film di base e sigillando efficacemente i prodotti all'interno dei blister. Questo crea una confezione sicura e a prova di manomissione.
Raffreddamento: i blister sigillati vengono quindi fatti passare attraverso una stazione di raffreddamento. Questa fase garantisce che le aree sigillate si raffreddino e si solidifichino, mantenendo l'integrità delle saldature e prevenendo deformazioni o perdite.
Perforazione e taglio: una volta raffreddata, la striscia continua di blister viene trasferita alla stazione di perforazione e taglio. Qui, la macchina perfora e taglia la striscia in blister singoli o fogli più grandi, a seconda della configurazione finale desiderata. Questa fase include spesso linee di perforazione per facilitare lo strappo e la separazione dei singoli blister.
Ispezione ed espulsione: la fase finale prevede l'ispezione dei blister per il controllo qualità. Sistemi automatizzati verificano il corretto posizionamento del prodotto, la corretta sigillatura e l'integrità complessiva della confezione. Eventuali confezioni difettose vengono espulse automaticamente dalla linea di produzione. I blister finiti vengono quindi ritirati per il successivo confezionamento o la distribuzione diretta.
Le blisteratrici a rulli garantiscono un confezionamento ad alta velocità, efficiente e affidabile dei prodotti farmaceutici. Automatizzando il processo, dall'alimentazione del materiale al controllo finale, queste macchine migliorano significativamente la produttività e mantengono rigorosi standard qualitativi, rendendole un componente essenziale nella moderna produzione farmaceutica.
Vantaggi della macchina confezionatrice blister
Le blisteratrici offrono numerosi vantaggi, rendendole la scelta preferita nel settore farmaceutico e del confezionamento. Tra questi, efficienza, economicità, automazione e integrazione, tra gli altri vantaggi.
Produzione ad alta velocità: le macchine blisteratrici sono progettate per operazioni ad alta velocità, consentendo il confezionamento rapido di prodotti farmaceutici.
Precisione e coerenza: queste macchine garantiscono un controllo preciso sui processi di formatura, riempimento e sigillatura, garantendo un imballaggio coerente e accurato.
Versatilità: queste macchine possono gestire un'ampia gamma di materiali di imballaggio e tipologie di prodotti. Sono sufficientemente versatili da confezionare compresse, capsule e altri piccoli articoli, adattandosi a diverse dimensioni e forme.
Utilizzo efficiente dei materiali: le macchine blisteratrici ottimizzano l'utilizzo dei materiali di imballaggio, riducendo gli sprechi e abbassando i costi dei materiali.
Automazione e integrazione: le moderne macchine blisteratrici possono essere integrate con altre apparecchiature nella linea di produzione, come macchine astucciatrici e sistemi di ispezione. Questa automazione semplifica il processo di confezionamento, riducendo il lavoro manuale e aumentando l'efficienza complessiva.
Applicazione della macchina confezionatrice blister
Le blisteratrici sono fondamentali in diversi settori grazie alla loro versatilità ed efficienza. Il loro utilizzo principale è il settore farmaceutico, ma svolgono un ruolo cruciale anche in altri ambiti.
industria farmaceutica
Compresse e capsule: garantiscono dosaggi precisi e li proteggono dall'umidità e dalla contaminazione.
Fiale e fiale: confezione sicura e a prova di manomissione.
Industria nutraceutica
Anche i prodotti nutraceutici come integratori alimentari e vitamine vengono comunemente confezionati utilizzando blisteratrici a rulli. Queste macchine offrono una soluzione di confezionamento affidabile e visivamente accattivante, che migliora la presentazione del prodotto e la fiducia dei consumatori.
Dispositivi medici
Questi macchinari confezionano piccoli dispositivi e componenti medici, come siringhe, aghi e strisce diagnostiche. Il confezionamento garantisce sterilità e facilità di manipolazione, offrendo al contempo una barriera protettiva contro i fattori ambientali.
Cosmetici e cura della persona
Le blisteratrici a rulli vengono utilizzate nell'industria cosmetica per confezionare prodotti come prodotti per la cura della pelle, piccoli contenitori per cosmetici e applicazioni monouso. Il confezionamento aiuta a mantenere la freschezza del prodotto e offre pratici formati monodose.
Cibo e dolciumi
Nell'industria alimentare, le blisteratrici a rulli vengono utilizzate per confezionare piccoli prodotti dolciari, gomme da masticare e altri prodotti commestibili. Il confezionamento garantisce la sicurezza del prodotto e ne prolunga la durata di conservazione, offrendo al contempo interessanti opzioni di presentazione.
Le affermazioni sopra riportate riflettono la mia limitata conoscenza delle macchine blisteratrici. Se avete prospettive o opinioni diverse, non esitate a contattarmi. Ingegnere di imballaggio Ruida.