Dans emballage pharmaceutiqueLe bon doseur joue un rôle crucial dans le maintien d'une ligne de production efficace et fiable. Différents produits et configurations d'emballage nécessitent des types de doseurs spécifiques pour garantir un fonctionnement fluide, un dosage précis et minimiser les dommages aux produits fragiles comme les comprimés et les gélules. Comprendre les fonctions et les applications de chaque doseur peut vous aider à choisir la meilleure option pour votre ligne de production. Nous allons explorer ci-dessous six doseurs couramment utilisés dans l'emballage pharmaceutique et détailler comment ils répondent à différents besoins opérationnels.
1. Alimentateur vibrant à disque
Le doseur vibrant à disque est conçu pour assurer un flux régulier et contrôlé de produits, grâce aux vibrations, pour transporter efficacement les comprimés ou les gélules. Son principal avantage réside dans la précision qu'il apporte au processus de conditionnement, car il assure un flux régulier évitant les goulots d'étranglement et l'agglutination.
Comment ça marche
Le dispositif d'alimentation vibrant à disque place les produits sur un disque vibrant qui les propulse doucement vers l'avant. Ce mouvement contrôlé est particulièrement important pour les articles fragiles susceptibles de se briser sous une force excessive. En minimisant les impacts, ce type de dispositif réduit le risque d'endommagement des produits tout en assurant la fluidité de la chaîne d'approvisionnement.
Cas d'utilisation idéaux
Le doseur vibrant à disque est particulièrement adapté aux lignes de production compactes où l'espace est limité. Son efficacité dans la gestion des produits délicats, tels que les comprimés enrobés, en fait un choix populaire pour les fabricants soucieux de préserver l'intégrité de leurs produits.
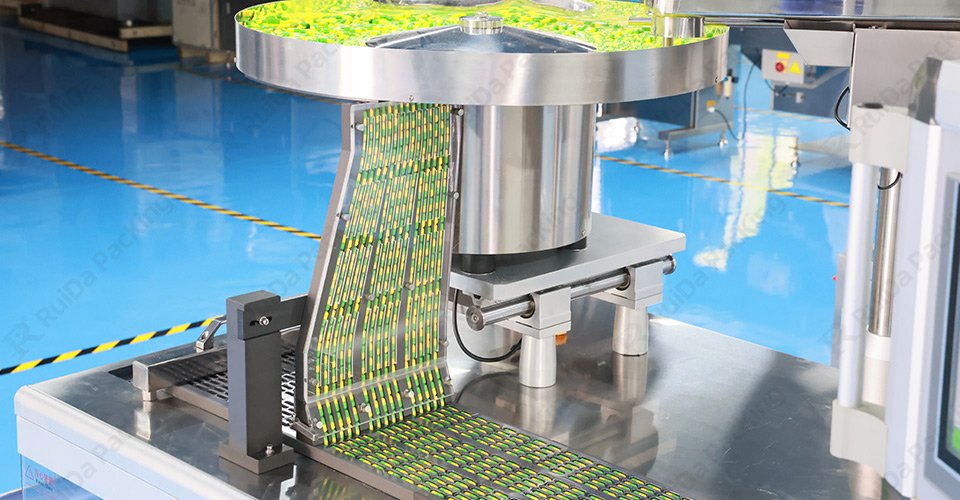
2. Alimentateur à brosse à disque
Le doseur à brosses à disque est réputé pour sa manipulation délicate des produits, ce qui en fait un excellent choix pour les articles nécessitant un alignement précis. Équipé de brosses qui guident les articles le long d'un disque rotatif, ce doseur sépare et organise les produits, garantissant leur positionnement précis pour la suite du traitement.
Comment ça marche
L'alimentateur à brosses à disque utilise des brosses qui tournent avec le disque, guidant délicatement les comprimés ou les gélules. Ce système réduit les risques de blocage et permet d'éviter les interruptions de production. Les brosses servent également à séparer les produits, évitant ainsi les chevauchements ou les désalignements lors de leur passage vers la phase de conditionnement.
Cas d'utilisation idéaux
Ce type d'alimentateur est idéal pour la manipulation d'articles petits et délicats, comme les gélules ou les comprimés non enrobés, qui nécessitent une manipulation minutieuse. En minimisant les frottements et en maintenant l'espacement des produits, l'alimentateur à brosses à disques réduit efficacement les dommages tout en optimisant la précision.
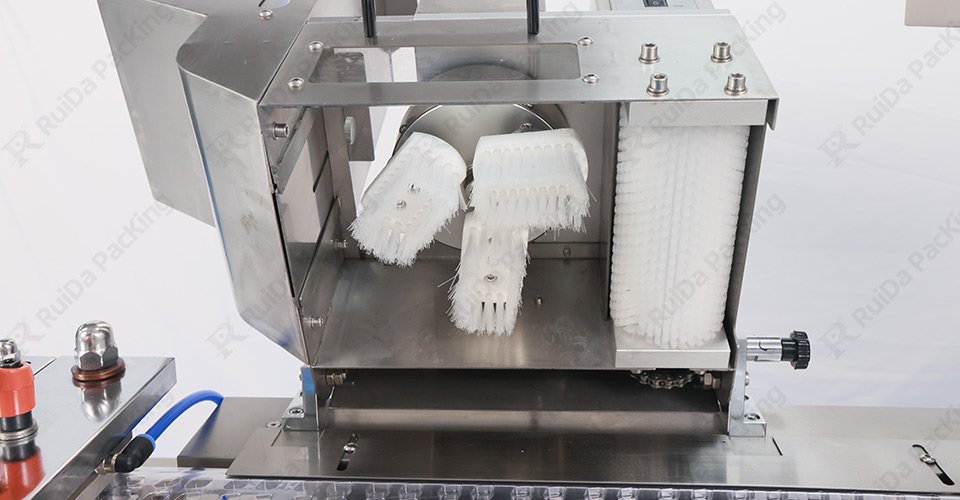
3. Alimentateur à brosse à rouleau incliné
Le système d'alimentation à rouleaux et brosses inclinés combine un plan incliné et des brosses rotatives, assurant un flux contrôlé qui maintient l'alignement et prévient les obstructions. Cette conception unique permet de déplacer les produits en angle, ce qui est avantageux pour les lignes nécessitant un flux assisté par gravité.
Comment ça marche
La conception inclinée de ce doseur permet aux comprimés ou aux gélules de descendre à un rythme régulier, grâce à des rouleaux et des brosses qui les guident. Les rouleaux et les brosses garantissent l'orientation et l'espacement des produits, créant ainsi un flux constant, essentiel pour les lignes de conditionnement à grande cadence.
Cas d'utilisation idéaux
Si vous avez besoin d'un doseur garantissant un alignement précis et minimisant les blocages, le doseur à rouleaux et brosses inclinés est un excellent choix. Ce type de doseur est particulièrement utile dans les applications pharmaceutiques où le maintien de l'orientation est essentiel, comme pour les produits ovales ou en forme de capsule.
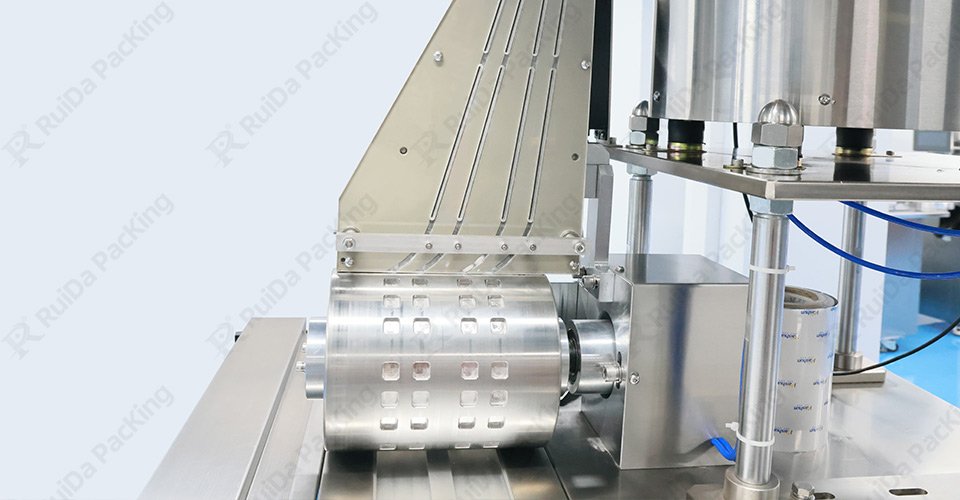
4. Alimentateur à brosse à rouleau
L'alimentateur à brosses rotatives est conçu pour des opérations à grande vitesse, ce qui en fait un choix idéal pour les lignes de conditionnement exigeant un flux de produits rapide et continu. Il fonctionne grâce à une série de brosses rotatives qui font avancer les produits tout en garantissant un espacement et un alignement réguliers.
Comment ça marche
Les rouleaux à brosses séparent délicatement les produits et maintiennent un débit constant, évitant ainsi leur agglomération. Cette action permet d'éviter les arrêts de production, car la conception du rouleau à brosses assure un déplacement régulier des produits, sans frottement ni impact inutiles.
Cas d'utilisation idéaux
Ce type d'alimentateur est idéal pour la manutention de produits fragiles, tels que les comprimés mous ou les gélules. Il est également parfaitement adapté aux lignes à grande vitesse qui nécessitent un espacement rapide et uniforme des produits. L'efficacité de l'alimentateur à brosses rotatives, qui maintient un flux constant et sans rupture, constitue un atout majeur pour le conditionnement pharmaceutique.
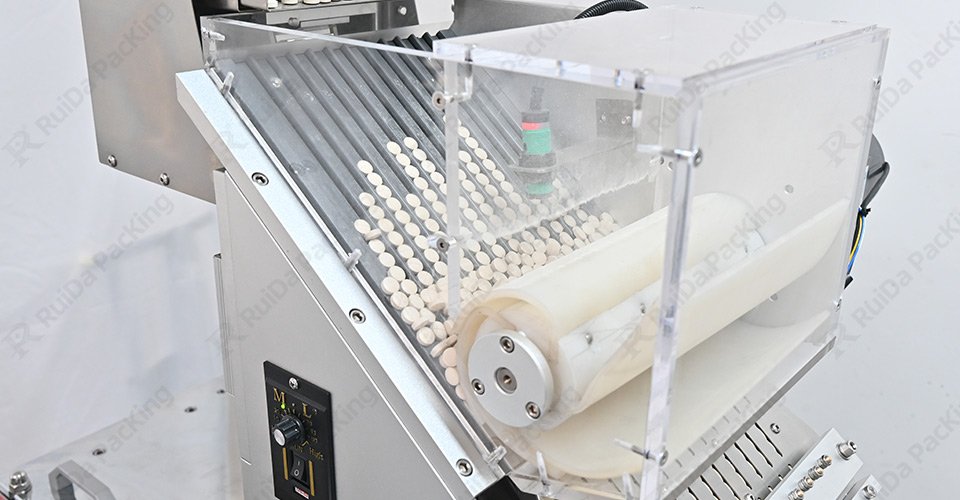
5. Rouleau d'alimentation à brosse à disque
Le rouleau d'alimentation à brosses à disque est une option hybride qui combine les avantages d'un disque rotatif et de brosses à rouleau, offrant une solution flexible pour divers produits. Sa conception en fait un choix polyvalent pour les lignes de conditionnement exigeant un équilibre entre vitesse et précision.
Comment ça marche
Les produits sont déplacés le long d'un disque rotatif, guidés par des rouleaux et des brosses qui les maintiennent espacés et alignés. Ce système hybride offre une plus grande flexibilité dans la manipulation de différents types de produits, car la combinaison du mouvement du disque et des rouleaux minimise les bourrages tout en garantissant un positionnement constant.
Cas d'utilisation idéaux
Le doseur à rouleaux et brosses à disques est idéal pour les applications pharmaceutiques exigeant flexibilité et capacité à traiter diverses formes de comprimés et de gélules. Son adaptabilité en fait un excellent choix pour traiter plusieurs produits sur une même ligne de conditionnement, permettant des transitions fluides entre différents formats.
6. Alimentateur à retournement de capsules
Le dispositif d'alimentation par retournement de capsules est spécialement conçu pour orienter les capsules dans la bonne position avant leur conditionnement. Cela garantit un positionnement uniforme de chaque capsule, essentiel pour un dosage et un scellage précis lors du processus de conditionnement.
Comment ça marche
Le doseur retourneur de capsules oriente les capsules de manière uniforme, les préparant ainsi pour les étapes suivantes de la ligne de conditionnement. En manipulant les capsules individuellement, ce doseur minimise le risque d'orientation incorrecte, susceptible d'entraîner des erreurs de dosage ou des problèmes de scellage.
Cas d'utilisation idéaux
Pour les lignes de conditionnement de capsules uniquement, le doseur rotatif est un composant essentiel. Sa capacité à traiter chaque capsule individuellement garantit l'uniformité, ce qui le rend indispensable dans les applications où l'orientation est cruciale, comme le conditionnement sous blister. Ce doseur est particulièrement utile pour les lignes qui privilégient une grande précision et un minimum d'erreurs dans l'alignement des capsules.
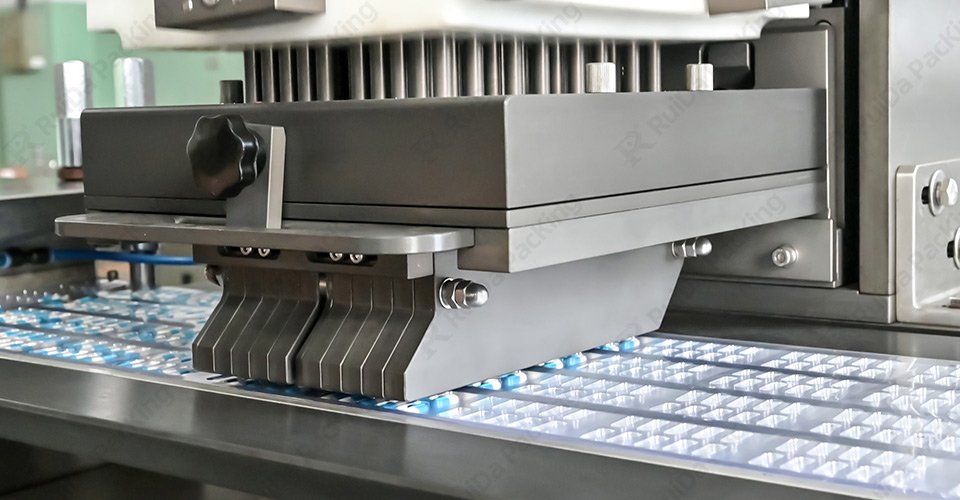
Produit recommandé : Machine d'emballage sous blister DPP-270Max
Si vous recherchez une machine fiable qui complète les alimentateurs décrits ci-dessus, le DMachine d'emballage sous blister PP-270Max est un choix exceptionnel. Réputée pour sa polyvalence et son efficacité, cette machine est conçue pour traiter avec précision diverses formes de comprimés et de capsules.
Pourquoi c'est une solution idéale pour votre ligne de production.
La DPP-270Max allie efficacité, précision et flexibilité, ce qui en fait un complément idéal à toute ligne de conditionnement pharmaceutique. Qu'elle soit destinée à des opérations à grande vitesse ou à différents types de produits, cette machine assure une intégration fluide et une production de haute qualité. Ses capacités s'harmonisent parfaitement avec les doseurs présentés dans cet article, offrant une solution cohérente qui optimise chaque étape de votre processus de conditionnement.
Conclusion
Choisir le bon doseur est essentiel pour maintenir l'efficacité et la qualité de votre ligne de conditionnement pharmaceutique. En comprenant les points forts et les applications de chaque type de doseur, vous pouvez optimiser le flux de produits, réduire les dommages et garantir la précision à chaque étape. Que vous recherchiez une manipulation délicate, une orientation précise ou des performances à grande vitesse, le choix du doseur adapté garantit un conditionnement homogène et de haute qualité. En associant ces doseurs à une machine de pointe comme la DPP-270Max, vous obtenez une ligne de production fluide, fiable et efficace, répondant aux normes les plus strictes en matière de conditionnement pharmaceutique.