¿Qué es la línea de llenado de botellas Count?
Línea de llenado de botellas de conteo Es una línea de producción automatizada que se utiliza en las industrias farmacéutica, nutracéutica y alimentaria para contar y llenar con precisión productos, como tabletas, cápsulas, gomitas o geles blandos, en botellas.
¿En qué consiste la línea de llenado de botellas Count?
La línea de llenado de botellas incluye: posicionador de botellas, alimentador elevador, contador de cápsulas, controladora de peso, insertador de desecante, tapadora, selladora de papel de aluminio y etiquetadora. ¿Cómo funciona la máquina?
Desenredador de botellas
Desenredador de botellas Es una máquina diseñada para orientar y posicionar automáticamente las botellas correctamente en la línea de conteo de cápsulas. El principio de funcionamiento de un posicionador de botellas suele consistir en los siguientes pasos:
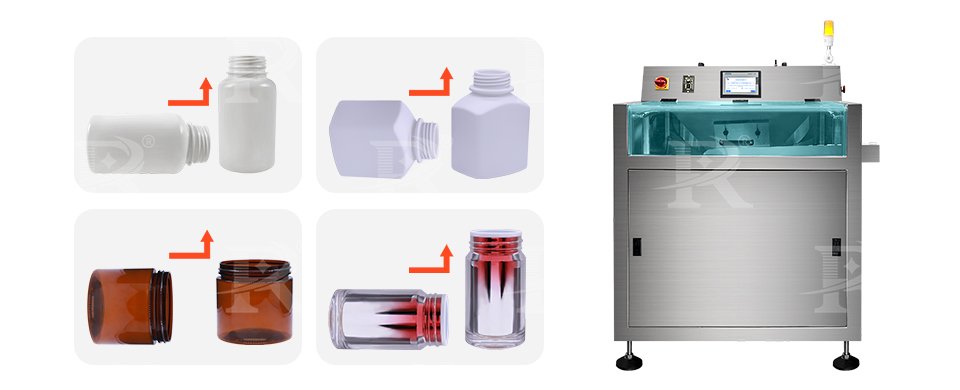
Carga de botellas: Las botellas vacías se cargan en una tolva o alimentador a granel, a menudo en una orientación aleatoria.
Mecanismo de clasificación: Las botellas se transfieren de la tolva a un disco giratorio, donde se clasifican y se guían hacia canales específicos. Este mecanismo utiliza la gravedad, la fuerza centrífuga o la vibración para mover las botellas a la siguiente etapa.
Orientación y alineación: A medida que las botellas avanzan por los canales, se enderezan mediante rieles, guías o embudos. Las botellas desalineadas se corrigen o se devuelven a la tolva de granel para un nuevo paso por el sistema.
Detección y ajuste: Los sensores o detectores mecánicos garantizan que solo pasen las botellas correctamente orientadas. Las botellas que no estén correctamente alineadas se redirigen a la etapa de clasificación.
Descarga y transferencia: Una vez que las botellas están orientadas correctamente, se liberan en una cinta transportadora en una sola fila, listas para ser llenadas o procesadas más adelante en la línea de producción.
Control de velocidad: El posicionador funciona a velocidades ajustables para adaptarse al ritmo de los procesos de llenado y envasado posteriores, lo que garantiza un flujo continuo de botellas.
Máquina alimentadora elevadora
El alimentador elevador es una máquina que se utiliza para elevar y alimentar materiales, como tabletas, cápsulas, gomitas u otros artículos pequeños, desde un nivel inferior a uno superior en una línea de producción. El principio de funcionamiento de un alimentador elevador generalmente implica los siguientes pasos:
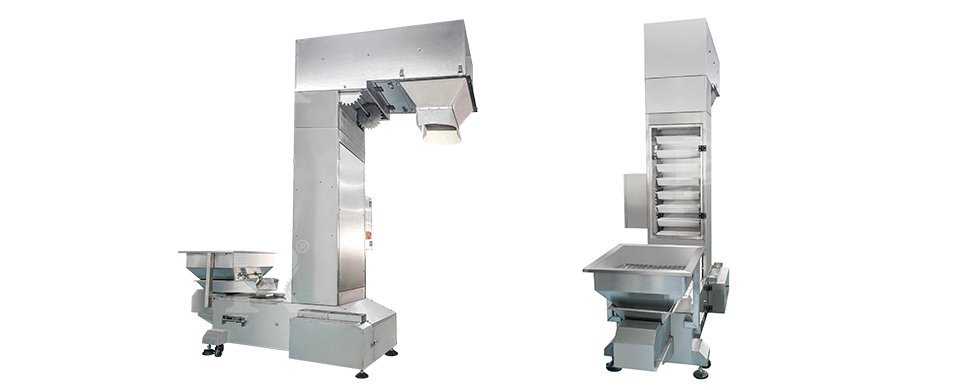
Carga de material: Los materiales (tabletas, cápsulas, gomitas u otros artículos pequeños) se cargan en una tolva o bandeja de alimentación ubicada en la base del alimentador elevador. Esto suele realizarse de forma manual o automática desde una etapa previa del proceso de producción.
Mecanismo de transporte: El alimentador de elevación utiliza un mecanismo de transporte, como una cinta transportadora, un cangilón o un sistema vibratorio, para mover los materiales hacia arriba. En un transportador de cangilones, por ejemplo, los materiales se recogen en pequeños cangilones unidos a una cinta transportadora o cadena, que gira para elevar los materiales a la altura deseada.
Elevación y elevación: El mecanismo de transporte, al funcionar, eleva los materiales desde la tolva a un nivel superior. La velocidad y el ángulo de elevación suelen ajustarse para controlar el caudal y adaptarse a las necesidades del equipo aguas abajo.
Descarga: En la parte superior del elevador, los materiales se descargan desde el transportador a una tolva de recepción, un conducto o directamente a una máquina embotelladora de conteo.
Retorno y recarga: El mecanismo de transporte regresa a la posición inicial, listo para recoger más materiales de la tolva y repetir el proceso.
Sistema de control: El alimentador elevador generalmente está equipado con sensores y un sistema de control que monitorea el nivel de material en la tolva y ajusta la velocidad de alimentación para garantizar un suministro continuo y constante.
Máquina contadora de cápsulas y tabletas
Máquina contadora de cápsulas para tabletas Puede contar tabletas, cápsulas y gomitas de 3 a 40 mm en botellas. El principio de funcionamiento de una máquina embotelladora con contador implica los siguientes pasos:
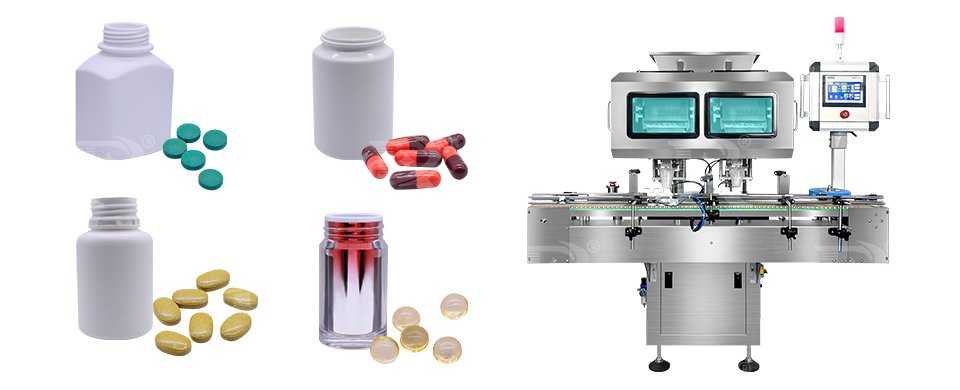
Alimentación: Las tabletas o cápsulas se introducen en la máquina desde una tolva o alimentador. Los productos suelen dirigirse a una placa vibratoria o transportador que los distribuye uniformemente.
Orientación y separación de productos: Los productos se distribuyen y alinean en la cinta transportadora o placa vibratoria. Se guían en filas individuales, lo que garantiza la separación de cada artículo para un conteo preciso.
Mecanismo de conteo: La máquina utiliza sensores, generalmente ópticos o infrarrojos, para contar cada artículo al pasar por un punto designado. Estos sensores detectan y registran cada producto, garantizando un conteo preciso antes de dispensarlo en la botella.
Posicionamiento de Botellas: Las botellas vacías se introducen en la cinta transportadora y se posicionan bajo el tubo de dispensación. La máquina garantiza que cada botella esté correctamente alineada para recibir los productos contados.
Proceso de llenado: Una vez contabilizada la cantidad correcta de productos, estos se dosifican en la botella. La máquina controla el flujo para garantizar que solo se llene la cantidad exacta de artículos en cada botella.
Máquina controladora de peso
La controladora de peso es una máquina que se utiliza en las líneas de producción para garantizar que el peso de los productos envasados cumpla con los estándares especificados. Su principio de funcionamiento consiste en los siguientes pasos:
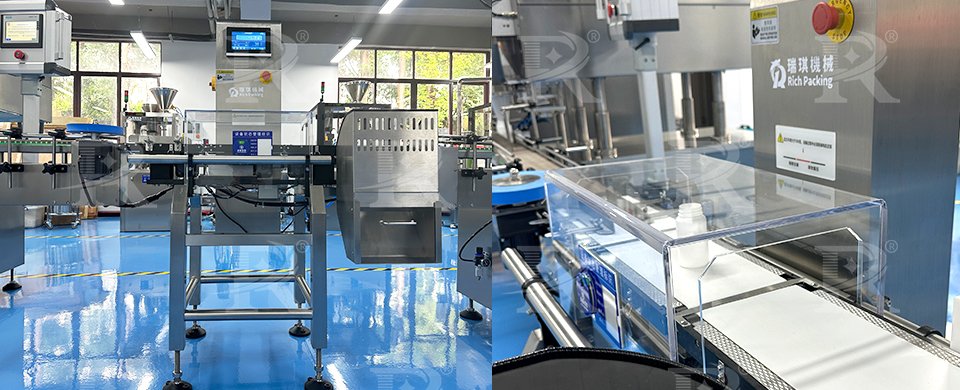
Alimentación del producto: Una vez contado el producto por la embotelladora, las botellas pasan por la cinta transportadora y entran en la controladora de peso. La cinta transportadora mueve los productos a una velocidad constante.
Mecanismo de pesaje: A medida que cada botella pasa por la plataforma de pesaje o báscula integrada en la cinta transportadora, la controladora de peso mide su peso. Esto se realiza generalmente mediante una celda de carga de alta precisión, que convierte el peso en una señal eléctrica para su procesamiento.
Procesamiento de datos: El sistema de control de la controladora de peso compara el peso medido de cada producto con los límites de peso preestablecidos. Estos límites definen el rango de peso aceptable (p. ej., pesos mínimo y máximo permitidos).
Clasificación o rechazo: Si el peso del producto se encuentra dentro del rango aceptable, continúa por la cinta transportadora hasta el insertador de desecante. Si el producto tiene un peso inferior o superior al normal, el empujador lo desvía automáticamente a una zona de rechazo.
Retroalimentación y Ajuste: La controladora de peso proporciona retroalimentación en tiempo real a la línea de llenado de botellas, lo que permite realizar ajustes en el proceso de llenado o envasado si se detectan inconsistencias en el peso. Esto ayuda a mantener una calidad constante del producto y reduce el desperdicio.
Registro de datos e informes: La controladora de peso suele registrar los datos de peso y generar informes para el control de calidad. Estos datos pueden utilizarse para supervisar las tendencias de producción, garantizar el cumplimiento normativo y optimizar el proceso de producción.
Máquina insertadora de desecante
La máquina insertadora de desecante se utiliza para insertar automáticamente sobres de desecante en botellas o contenedores, generalmente en las industrias farmacéutica, alimentaria o de envasado, para mantener el contenido seco y libre de humedad. El principio de funcionamiento de una máquina insertadora de desecante consiste en los siguientes pasos:
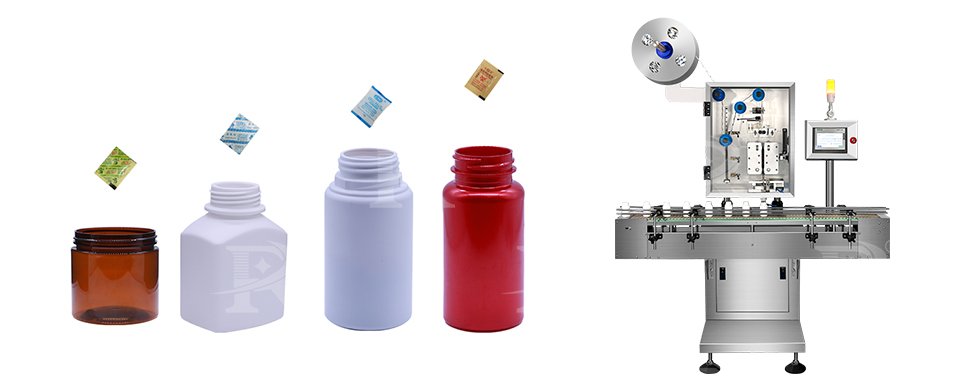
Suministro de desecante: Los paquetes de desecante se cargan en un sistema de alimentación, generalmente una tolva o un cargador, donde se almacenan y se introducen en la máquina.
Separación y Orientación: Los paquetes de desecante se separan del suministro a granel y se orientan para su inserción. Esto suele realizarse mediante un mecanismo vibratorio o rotatorio que asegura que cada paquete se introduzca individualmente en el sistema de inserción.
Posicionamiento de botellas o contenedores: Las botellas se colocan debajo del punto de inserción del desecante. Un sensor o sistema de posicionamiento garantiza que cada contenedor esté correctamente alineado y listo para recibir el paquete de desecante.
Mecanismo de inserción: Se introduce en la botella o envase. El tiempo de inserción se sincroniza con el movimiento de las botellas en la cinta transportadora para garantizar una operación precisa.
Operación continua: La máquina opera de manera continua, insertando automáticamente paquetes de desecante en los contenedores a medida que pasan por la línea, lo que garantiza que el proceso de envasado sea eficiente y consistente.
Máquina tapadora
Máquina tapadora Está diseñada para colocar y asegurar automáticamente tapas en botellas o envases como parte de una línea de producción. El principio de funcionamiento de una máquina taponadora consiste en los siguientes pasos:
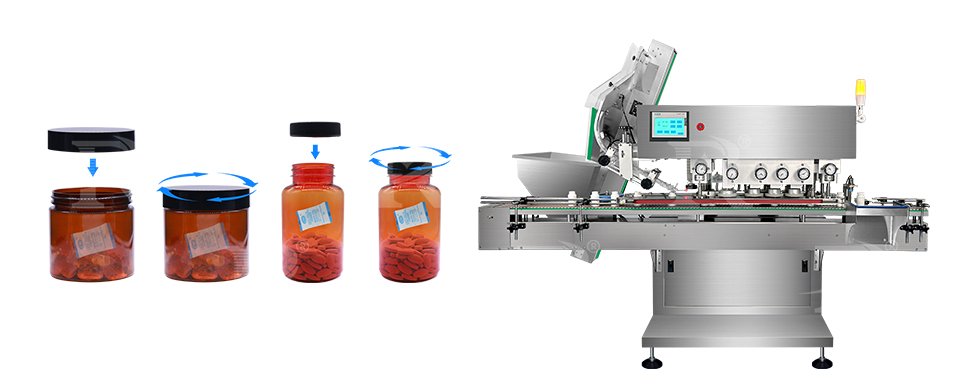
Alimentación de botellas: Las botellas se introducen en una cinta transportadora y se desplazan hacia la estación de tapado. La máquina garantiza que las botellas estén correctamente espaciadas y orientadas para el tapado.
Clasificación y alimentación de tapas: Las tapas se cargan en un alimentador o clasificador, que las organiza y alinea. A continuación, se introducen en una rampa o riel que las guía hasta el cabezal de tapado. Esto garantiza que las tapas estén correctamente orientadas antes de colocarlas en las botellas.
Colocación de la tapa: a medida que cada botella pasa por debajo del cabezal de tapado, se toma una tapa y se coloca en la abertura de la botella.
Mecanismo de tapado: La máquina tapadora aprieta o fija el tapón a la botella. Se pueden utilizar diferentes tipos de mecanismos de tapado, según el tipo de tapón y de botella:
Taponado de rosca: La máquina aplica fuerza de rotación para enroscar el tapón en la botella, garantizando que quede firme y seguro.
Tapado a presión: para las tapas a presión, la máquina aplica presión hacia abajo para encajar la tapa en su lugar.
Taponado con engarce: para los tapones con engarce, la máquina utiliza una herramienta de engarce para sellar la tapa en el cuello de la botella.
Control de par: En las máquinas tapadoras de rosca, el par aplicado a la tapa se puede controlar con precisión para garantizar que no quede ni demasiado flojo ni demasiado apretado. Esto es fundamental para mantener la integridad del producto y garantizar la seguridad del consumidor.
Control de Calidad y Verificación: Algunas máquinas incluyen sensores o sistemas de visión para verificar que cada tapón esté correctamente colocado y asegurado. Si falta un tapón, está mal colocado o no está bien apretado, la botella puede rechazarse automáticamente o enviarse a retapar.
Máquina selladora de papel de aluminio
La selladora de aluminio se utiliza para sellar envases con una capa de aluminio, creando un sello hermético y a prueba de manipulaciones. Se utiliza comúnmente en las industrias alimentaria, farmacéutica y cosmética. El principio de funcionamiento de una selladora de aluminio consta de los siguientes pasos:
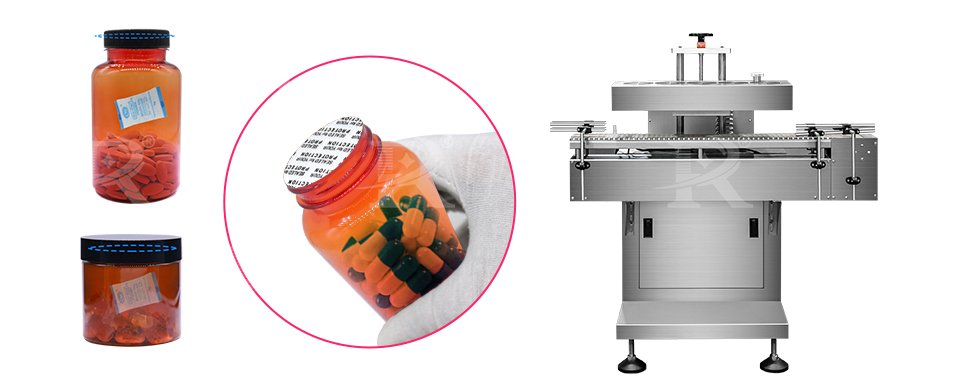
Alimentación de contenedores: Los contenedores se introducen en una cinta transportadora y se desplazan hacia la estación de sellado. La máquina garantiza que cada contenedor esté correctamente posicionado para el sellado.
Tapa con papel de aluminio: Los envases suelen tener tapas con un revestimiento de papel de aluminio en su interior. La tapa se coloca sobre el envase, con el papel de aluminio sobre la abertura.
Calentamiento por inducción: El recipiente pasa por una bobina de inducción, que genera un campo electromagnético de alta frecuencia. Este campo induce una corriente eléctrica en el papel de aluminio, provocando su calentamiento.
Transferencia de calor: El calor generado en el papel de aluminio funde el recubrimiento de polímero termosensible de su parte inferior. Esta capa de polímero se adhiere al borde del recipiente, formando un sello.
Aplicación de presión (opcional): En algunas máquinas, se puede utilizar una almohadilla o mecanismo de presión para presionar la lámina firmemente contra la abertura del contenedor durante el calentamiento, lo que garantiza un sellado uniforme y seguro.
Enfriamiento y solidificación: Tras el proceso de calentamiento, el polímero se enfría y solidifica, creando un sello hermético y de seguridad entre el papel de aluminio y el contenedor. A continuación, el contenedor se libera de la estación de sellado.
Control de Calidad y Verificación: Los contenedores sellados pueden pasar por una estación de control de calidad, donde sensores o cámaras verifican la integridad del sello. Cualquier contenedor con sellos defectuosos puede ser rechazado automáticamente.
Máquina etiquetadora
Máquina etiquetadora Se utiliza para aplicar etiquetas automáticamente a las botellas. Las etiquetadoras se utilizan ampliamente en industrias como la alimentaria, la farmacéutica, la cosmética y la del envasado. El principio de funcionamiento de una etiquetadora consta de los siguientes pasos:
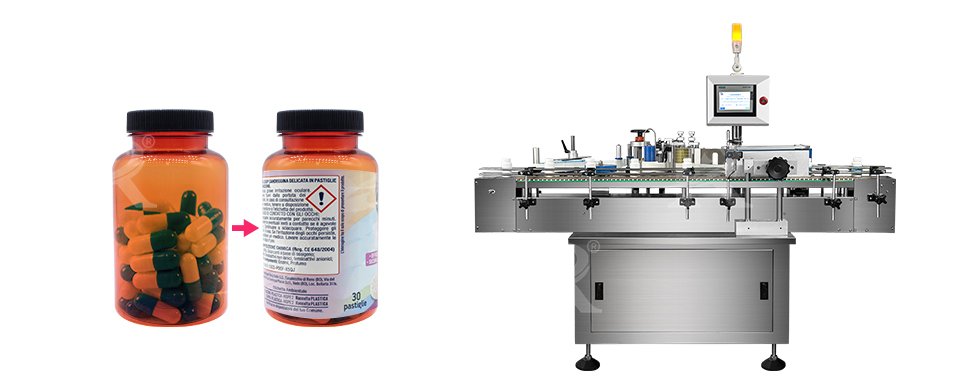
Alimentación del producto: Las botellas se introducen en una cinta transportadora que las desplaza hacia la estación de etiquetado. La máquina garantiza que cada artículo esté correctamente espaciado y orientado para una aplicación precisa de la etiqueta.
Alimentación de etiquetas: Las etiquetas se suministran en rollo o en hojas y se introducen en la etiquetadora. La máquina las desenrolla y las posiciona para su aplicación. Un sensor detecta el inicio de cada etiqueta para garantizar una colocación precisa.
Detección y alineación de etiquetas: Sensores o marcadores en la banda de etiquetas detectan la posición de cada etiqueta, garantizando su correcta alineación antes de su aplicación. Las etiquetas se despegan del soporte al llegar al punto de aplicación.
Aplicación de etiquetas: A medida que el producto pasa por la estación de etiquetado, la máquina aplica la etiqueta a su superficie. Según el tipo de etiquetadora, se utilizan diferentes métodos:
Etiquetado envolvente: La etiqueta se envuelve alrededor de productos cilíndricos o redondos, como botellas o latas. El producto puede girar durante la aplicación para asegurar una cobertura completa.
Etiquetado frontal y posterior: Se aplican etiquetas independientes en las superficies frontal y posterior del producto. La máquina coloca cada etiqueta con precisión en el lado correcto.
Etiquetado superior o inferior: las etiquetas se aplican a las superficies superiores o inferiores de productos o contenedores planos.
Etiquetado en esquinas o bordes: para paquetes o cajas, las etiquetas se pueden aplicar en esquinas o bordes, envolviendo dos superficies adyacentes.
Aplicación de presión: Un rodillo o cepillo puede aplicar una presión suave para garantizar que la etiqueta se adhiera de manera suave y segura a la superficie del producto sin arrugas ni burbujas.
Sistema de sensores y control: La máquina utiliza sensores para supervisar el proceso de etiquetado, garantizando que cada etiqueta se aplique correctamente y a la velocidad adecuada. El sistema de control puede ajustar la velocidad, la posición y la alineación de las etiquetas para adaptarse a diferentes tamaños y formas de productos.
Inspección y Control de Calidad: Tras el etiquetado, el producto puede pasar por una estación de inspección donde sensores o cámaras verifican la colocación, alineación y adherencia de las etiquetas. Cualquier producto con etiquetas mal aplicadas o faltantes puede ser rechazado o enviado para su reetiquetado.
Ya sea una máquina individual o una línea de llenado con conteo de cápsulas completas, embalaje de ruida Puede proporcionar servicios completos.