Induction sealing machines play a critical role in modern packaging industries, especially within the pharmaceutical, food, and cosmetics sectors. With efficient and reliable sealing technology, these machines not only ensure product safety and quality but also boost production efficiency. This article delves into the working principles and widespread applications of induction sealing machines, helping you better understand the importance of this equipment.
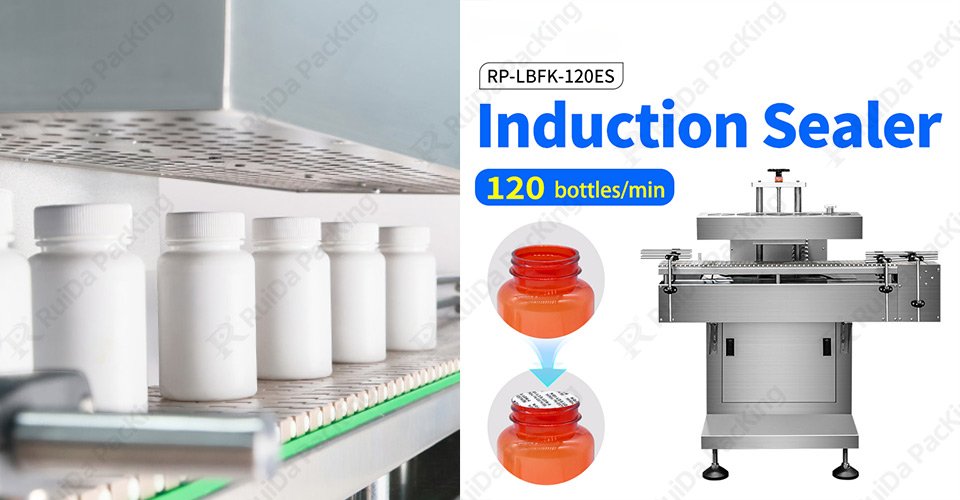
1. Working Principle of Induction Sealing Machines
1.1 Basic Structure
The main components of an induction sealing machine include the induction coil, control system, heating element, and conveyor system. The induction coil is the core component, generating high-frequency currents through electromagnetic induction to heat the sealing materials, like aluminum foil. The control system regulates the sealing temperature and time to ensure consistent sealing quality for each container.
1.2 Induction Sealing Process
The induction sealing process typically involves several steps:
– Material Preparation: Start by preparing the product and corresponding packaging materials. Ensure that the aluminum foil sealing material is tightly fitted to the container for the best seal.
– Machine Setup: Before starting, adjust the machine’s parameters—such as temperature, sealing time, and conveyor speed—according to the type of packaging material and product.
– Induction Heating and Sealing: As the packaging material passes through the induction coil, electromagnetic induction generates heat that quickly melts the aluminum foil, creating a seal. This process is extremely fast, usually taking just milliseconds, after which the foil bonds tightly to the container’s rim.
– Cooling and Inspection: After sealing, the material cools rapidly and solidifies. At this point, an inspection is necessary to ensure that each product meets the required sealing standards.
1.3 Evaluating Seal Quality
Induction sealing primarily ensures strong sealing and durability. Compared to traditional sealing methods, induction sealing provides enhanced security, protecting items such as medications and foods from moisture and oxidation while preventing contamination. A good seal helps extend the product’s shelf life and safeguards its quality.
2. Major Applications of Induction Sealing Machines
2.1 Pharmaceutical Industry
In pharmaceuticals, induction sealing machines are widely used for packaging medications. These products require storage in specific environments, and induction sealing offers an excellent sealing effect that preserves drugs from environmental impacts, maintaining efficacy. Additionally, it prevents counterfeiting, ensuring patient safety.
2.2 Food Industry
Induction sealing machines also play an essential role in food packaging. Food packaging requires effective moisture-proofing and oxidation resistance to ensure product freshness and safety. With induction sealing technology, foods remain fresh, retaining their flavor and nutrients while reducing waste and enhancing competitiveness in the market.
2.3 Cosmetics and Personal Care Products
In cosmetics packaging, induction sealing machines are crucial for maintaining product quality and stability. Many cosmetics contain active ingredients that benefit from effective sealing to prevent evaporation or spoilage, enhancing the user experience.
2.4 Other Industries
In addition to the above fields, induction sealing machines are widely used in electronics, chemicals, and other sectors. Here, induction sealing not only provides excellent sealing results but also increases production efficiency and reduces labor costs.
3. Advantages of Induction Sealing Machines
Induction sealing machines offer significant benefits. Firstly, they enhance production efficiency due to their rapid, automated sealing processes, allowing production lines to run faster with minimal manual intervention.
Additionally, induction sealing machines have low maintenance costs. With a simple structure and low failure rates, regular maintenance can extend the equipment’s life.
Furthermore, induction sealing machines are environmentally friendly. Their excellent sealing capability reduces the need for excessive packaging materials, helping lower a company’s environmental impact.
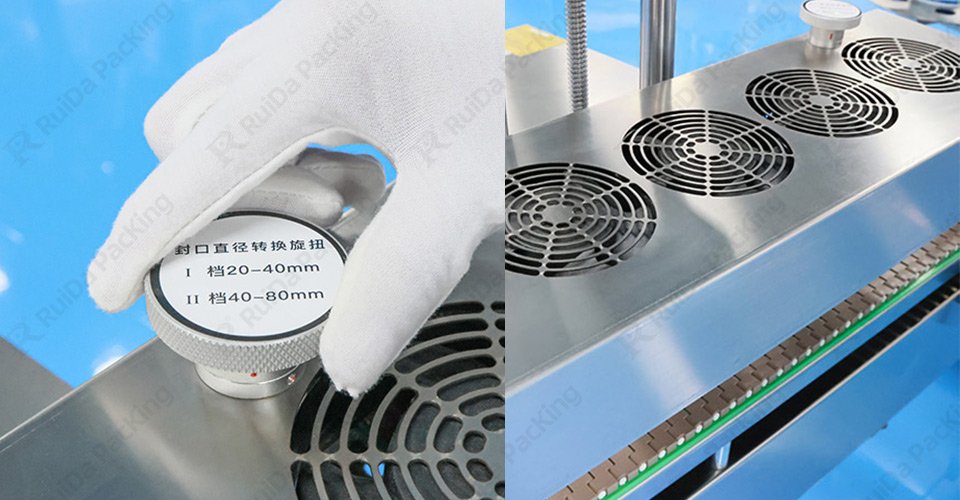
4. Choosing the Right Induction Sealing Machine
When selecting an induction sealing machine, consider a few key factors:
– Production Scale: Different production scales require different types of induction sealing machines. Small-scale production lines can opt for smaller machines, while large-scale operations need more efficient, automated equipment.
– Type of Sealing Material: Different sealing materials have specific requirements. Ensure that the equipment you choose can handle your packaging materials.
– Ease of Operation: Machines that are easy to operate and understand reduce training time and improve work efficiency.
Conclusão
Induction sealing machines are indispensable in modern packaging industries. By understanding their working principles and broad applications, you can better utilize this technology, providing safer and more efficient packaging solutions for your products. Choosing the right induction sealing machine will improve your production efficiency and product quality.