- Dom
- Maszyna do pakowania w blistry
Maszyna do pakowania w blistry
Blister card packing machine, often called cardboard packaging machine or blister card machines, automate the process of securely sealing products to pre-printed paperboard cards, typically combined with clear alu pvc blister, alu alu blister, or formed plastic trays. The main function is to protect the blister plate from being damaged. Key applications span diverse industries: pharmaceuticals (tablets, capsules), consumer goods (toys, electronics accessories, batteries), hardware & tools (fasteners, small hand tools), health & beauty (razors, cosmetics, oral care) and automotive parts. These machines efficiently handle product loading, card folding, blister sealing (heat or ultrasonic), and final closure. They are essential for creating tamper-evident, shelf-appealing packaging that enhances brand presence, provides product information, and protects items during shipping and handling. Ideal for medium to high-volume production of durable and display-oriented packages.
Aplikacja:
Paper card packing machine can pack tablet blisters, capsule blisters and other items.

Zasada działania
Paperboard Packaging Machine uses an automated process to place the blister sheet containing the tablets between two cardboards and then seals them, mainly to protect the blister sheet from being damaged.
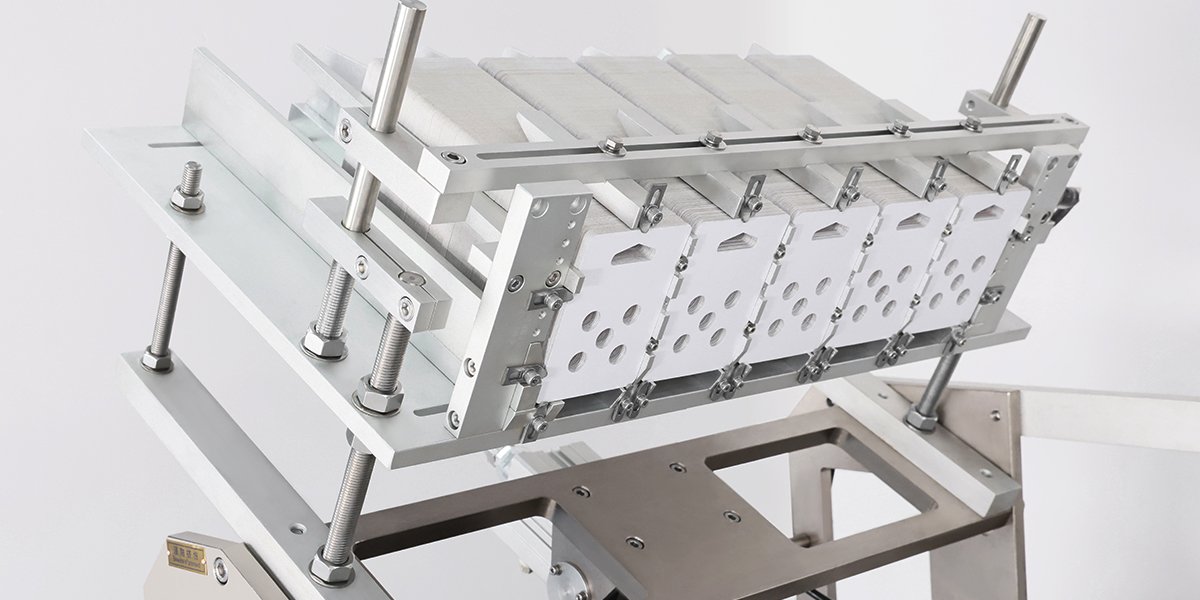
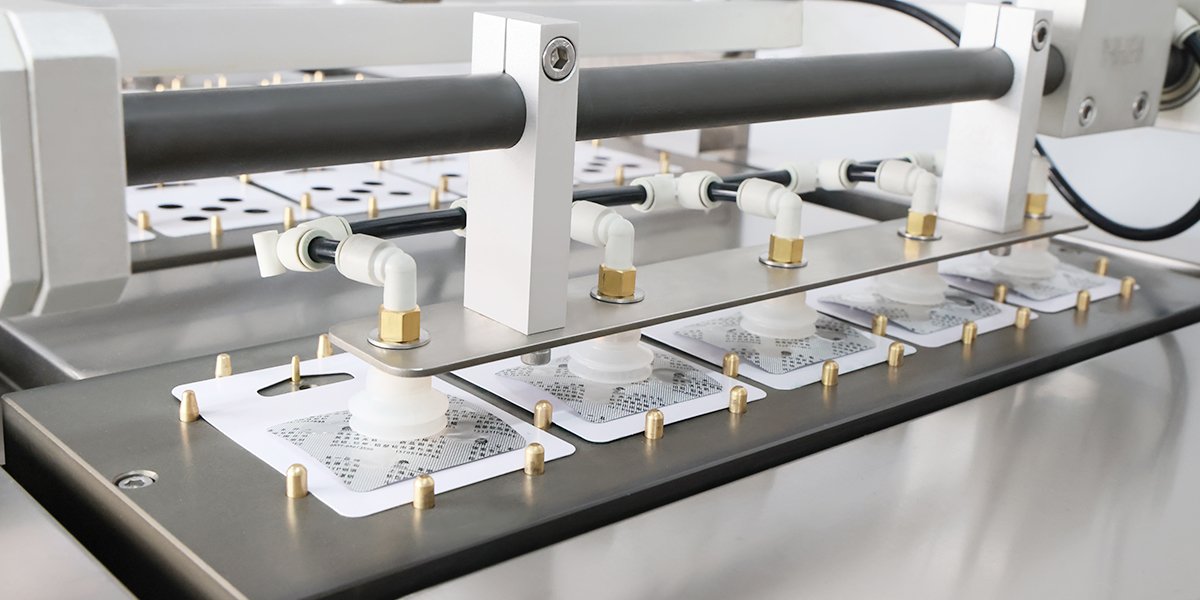
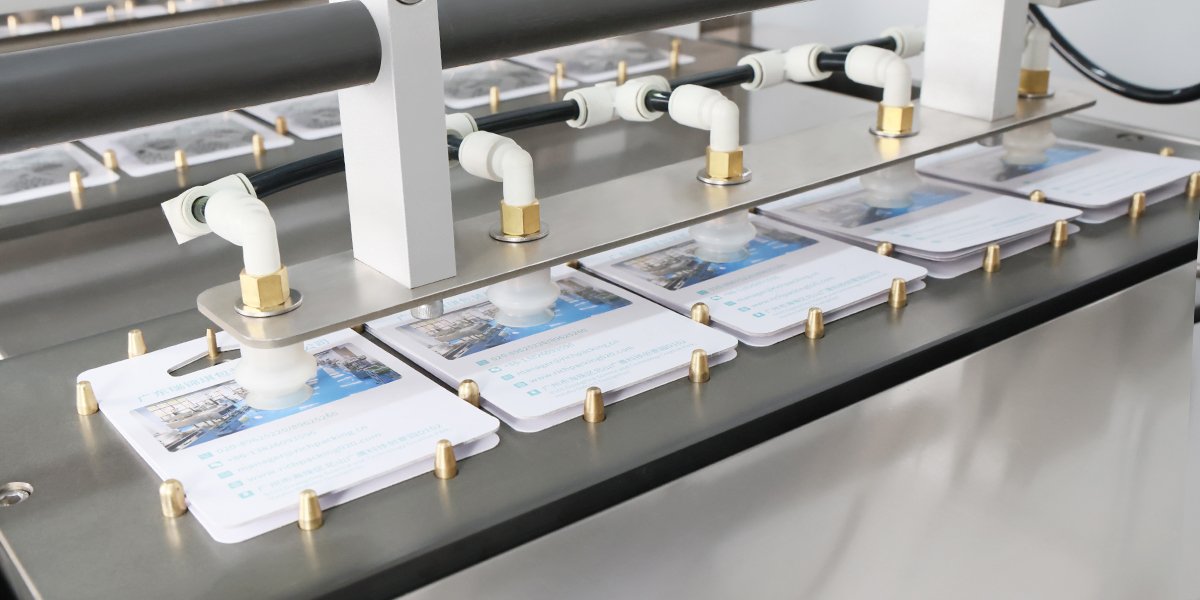
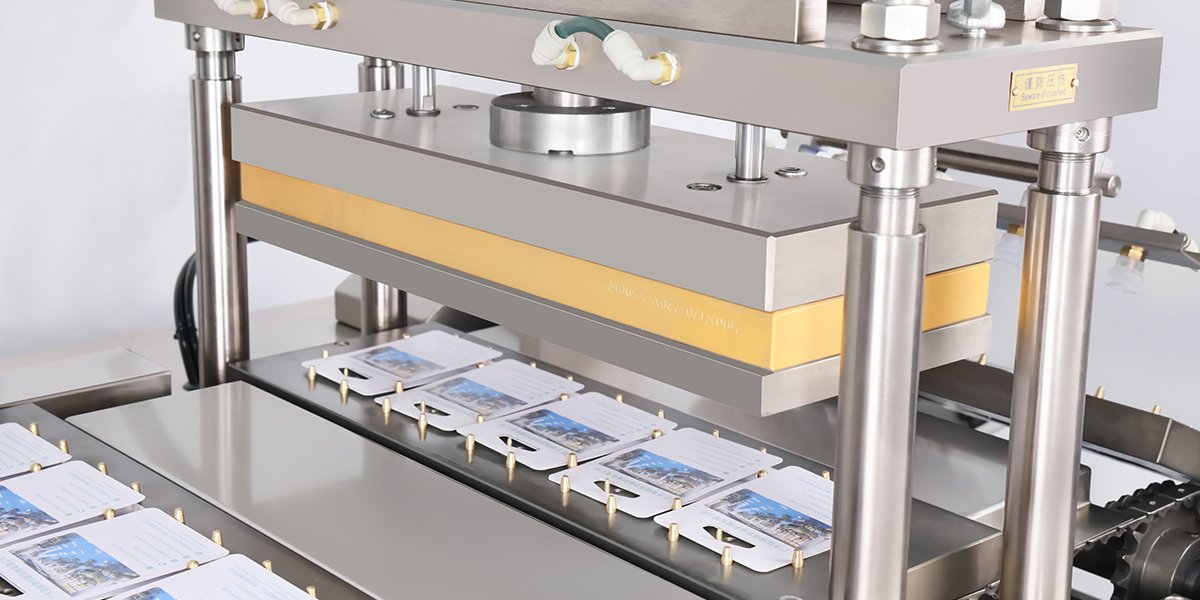
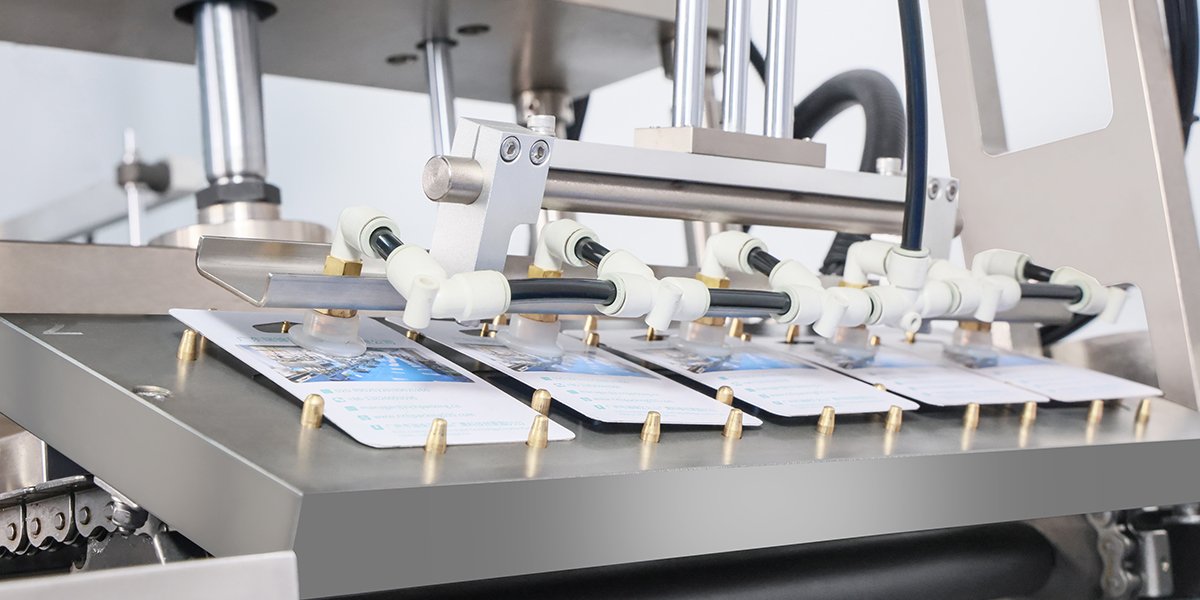
Parametry techniczne
Wybierz najlepszą maszynę biorąc pod uwagę rozmiar saszetek.
Machine Mold | RD-BCP-350Pro | RD-BCP-500Pro | RD-BCP-650Pro |
Zdolność produkcyjna | 3,600 Plates/h | 5,400 Plates/h | 6,400 Plates/h |
Max. Forming Area | 330*210*65mm | 470*220*65mm | 630*220*65mm |
Paper Card Size | 350*220*0.5mm | 500*300*.05mm | 650*300*0.5mm |
Całkowita moc | 11.8 kW | 12.8 kW | 15.8 kW |
Produkty wspomagające
NJP-3800D Automatic Capsule Filling Machine
NJP-3800D automatic capsule filling machine works by automatically feeding empty capsules, filling them with powder, closing, and output for packaging.
Blister Packing Machine Manufacturer
Blister packing machine manufacturer offer various type machines that boosts output while lowering labor costs and material waste.
Tablet Compression Machine
Tablet compression machine is essential equipment for producing solid tablets by compacting powdered or granular materials.
Dostawca jakości Fortune 500
Features Advantage
Firma Ruidapacking zobowiązuje się do produkcji maszyn o najwyższej jakości, spełniających standardy GMP, a jednocześnie charakteryzujących się wydajnością i użytecznością.
Full Servo Control
The stroke can be accurate to 0.1mm, which is convenient for the alignment of paper cards and aluminum-plastic panels. The adjustment of the pulling distance of the product can be completed with one click on the touch screen.
Stronger Pressure Resistance
The heat sealing station mold is treated with Teflon, with better surface smoothness and pressure exceeding 100 kN.
Hard Anodized Molds
The 28-piece mold is made of high-grade aluminum alloy, the draw-out slot design allows mold changes within 15 minutes.
Zapewniamy kompleksową obsługę
Będziemy towarzyszyć Ci w całym procesie – od wyboru odpowiedniej maszyny po dbanie o nią przez cały okres jej użytkowania.
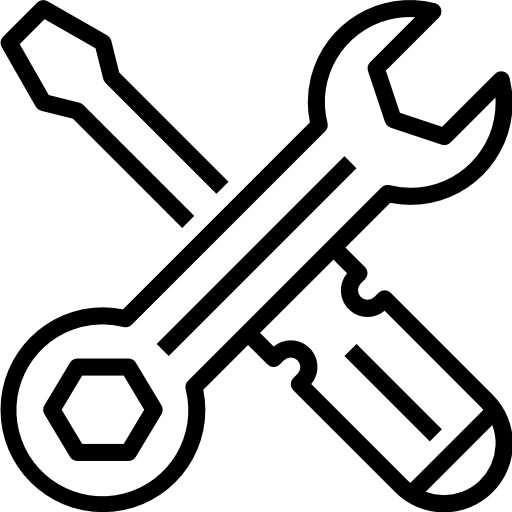
Gwarancja dożywotnia
Aby zapewnić najwyższą wydajność przez długi czas, oferujemy bezpłatną naprawę w ciągu 3 lat i bezpłatne części zamienne w ciągu 1 roku. Po tym czasie obiecujemy bezpłatną konsultację techniczną przez całe życie.
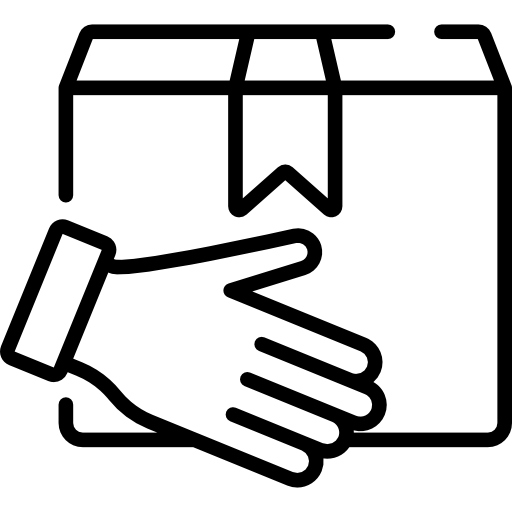
Szybka dostawa w ciągu 7 dni
95% naszych standardowych maszyn jest w magazynie. W takim przypadku przesyłka może dotrzeć w ciągu 7 dni. Jeśli chodzi o dogłębnie dostosowane produkty, dostawa trwa tylko 20 dni.
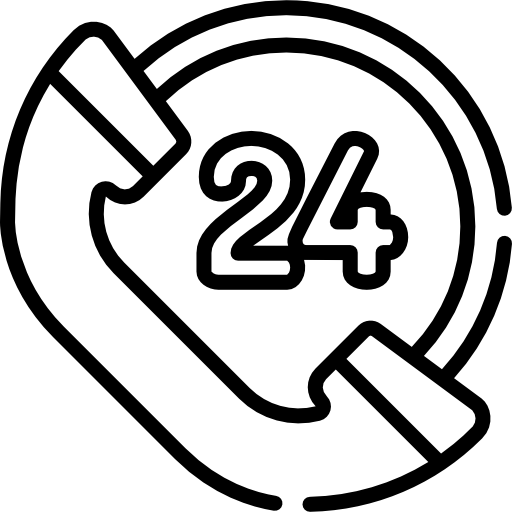
Usługa online
Nasi doświadczeni specjaliści ds. obsługi klienta oraz inżynierowie zajmą się Twoimi potrzebami i rozwiążą wszystkie Twoje problemy w ciągu 24 godzin, udzielając odpowiedzi na pytania i prowadząc zdalną rozmowę wideo.
Często zadawane pytania
Finding a truly reliable pharmaceutical blister card packaging machine can be a major headache for manufacturers. Common frustrations like poor sealing, product misalignment, and electrical safety concerns lead to wasted materials, rejected batches, operational downtime, and compliance risks. At Ruidapacking, we engineer our blister card machines to eliminate these exact problems, ensuring consistent quality, maximum efficiency, and uncompromised safety. Discover how our precision design solves the industry’s top three paper card packaging challenges.
1. Weak Sealing & High Reject Rates
The Industry Pain Point: Many blister card machines struggle with inconsistent or weak heat sealing. This results in blister packs detaching from the paperboard, compromised product integrity, and unacceptably high reject rates – directly hitting your bottom line through wasted materials and lost production time.
The Ruidapacking Solution: Our machines feature a heavy-duty heat sealing station engineered for perfection:
Massive, Controlled Pressure: We apply over 100 kN (10+ tons) of precisely calibrated pressure across the sealing area.
Premium Teflon-Coated Tooling: Sealing surfaces feature advanced Teflon (PTFE) coating, ensuring exceptional smoothness, consistent heat distribution, and preventing material sticking.
Result: Bonds are exceptionally strong and uniform every time. Dramatically reduced reject rates protect your profitability and ensure batch consistency.
2. Misaligned Cards & Poor Aesthetics
The Industry Pain Point: Achieving perfect alignment between the top and bottom paperboards is critical. Misaligned cards look unprofessional, can hinder functionality (e.g., hang holes blocked), and lead to consumer complaints or retailer rejections. Manual adjustments are time-consuming and often ineffective.
The Ruidapacking Solution: Precision alignment is built into our core design:
Dowel Pin Positioning System: We utilize a robust dowel pin location system within the tooling.
Guaranteed Registration: This system securely fixes each paperboard in its exact correct position on the mold before the heat sealing station begins.
Result: Perfect, consistent overlap of top and bottom cards every single cycle. Your finished packs look professional, function flawlessly, and meet the highest aesthetic standards.
3. Electrical Safety Hazards
The Industry Pain Point: Concerns about electrical safety, including potential leakage currents or unreliable components, are serious. These hazards endanger operators, violate strict cGMP and workplace safety regulations (like CE, UL), and create significant liability risks. Downtime for electrical repairs is costly.
The Ruidapacking Solution: Safety and reliability are non-negotiable:
World-Class Electrical Components: We exclusively integrate premium, globally recognized electrical brands (e.g., Siemens, Schneider Electric) known for their reliability and stringent safety certifications.
Robust Wiring & Grounding: Our machines are built with high-grade wiring harnesses and meticulous grounding practices exceeding international safety standards.
Result: Operators work with confidence. You achieve full compliance with cGMP and essential safety directives (CE marked), eliminate electrical hazard risks, and benefit from drastically reduced electrical failure downtime.
Wniosek
Stop battling unreliable blister card machines that compromise your quality, efficiency, and safety. Ruidapacking’s pharmaceutical paper card packaging machines are engineered from the ground up to solve the most persistent problems plaguing the industry. Our commitment to robust construction (100kN+ sealing), precision alignment (dowel pin system), and absolute electrical safety (premium components) delivers:
Higher Profitability: Slash reject rates and minimize costly downtime.
Flawless Quality: Guarantee perfectly aligned, professionally sealed packs.
Uncompromised Safety & Compliance: Meet cGMP and stringent electrical safety standards with confidence.
W przypadku linii pakujących gotowe torebki, kluczowa decyzja o wyborze wagi wielogłowicowej lub maszyny liczącej kapsułki tabletkowe jako sprzętu pomocniczego zależy od atrybutów obsługiwanego materiału. Te dwie technologie oferują wyraźne zalety i są dostosowane do konkretnych zastosowań. Wybór niewłaściwej maszyny może prowadzić do obniżenia wydajności, niewystarczającej dokładności, dużego marnotrawstwa materiału, a nawet awarii operacyjnej.
Poniżej szczegółowo analizujemy kryteria doboru, mocne strony i ograniczenia każdego urządzenia na podstawie kluczowych cech materiałowych:
1. Właściwości materiału
Forma fizyczna
Granulki, płatki, pałeczki, kawałki (regularne/nieregularne ciała stałe): Możliwymi opcjami są zarówno waga wielogłowicowa, jak i maszyna napełniająca licząca; ostateczny wybór zależy od innych właściwości.
Drobne cząstki: Zwykle lepiej nadają się do maszyn liczących.
Proszki, pasty, płyny, materiały lepkie: Ani wielogłowicowa napełniarka wagowa, ani automatyczne maszyny liczące nie są odpowiednie. Wymagają one sprzętu do napełniania objętościowego (napełniacze ślimakowe, napełniacze tłokowe, napełniacze do cieczy) lub wag netto.
Waga/rozmiar indywidualny
Duża i stosunkowo jednolita waga jednostkowa: (duże ciasteczka, tabliczki czekolady, całe owoce, części zabawek) Wielogłowicowe wagi kombinowane zazwyczaj oferują zalety w zakresie wydajności i opłacalności.
Bardzo mała lub bardzo zmienna waga jednostkowa: (małe pigułki, nasiona, żelki, mały sprzęt) Automatyczne elektroniczne maszyny liczące wyróżniają się precyzją i minimalizacją odpadów. Wagi wielogłowicowe mają problemy z kontrolą dokładności w przypadku bardzo lekkich przedmiotów, a małe przedmioty są podatne na utratę poprzez „odlatywanie” (napowietrzanie) w pojemnikach ważących podczas pracy.
2. Wagi wielogłowicowe
Materiał jest rozprowadzany z głównego podajnika wibracyjnego do wielu (zwykle 8–24) niezależnych wiader wagowych (lejów wagowych). System komputerowy stale odczytuje wagę w każdym wiadrze i używa algorytmu łączonego ważenia, aby szybko zidentyfikować grupę wiader, których łączna waga jest najbliższa wadze docelowej. Wybrane wiadra są rozładowywane jednocześnie do leja zbiorczego poniżej, kierując materiał do woreczka opakowaniowego.
Zalety
Duża prędkość: Zasada łączonego ważenia umożliwia wyjątkowo dużą prędkość ważenia (zwykle 100–200 torebek/minutę, przy czym modele o dużej prędkości przekraczają 300 torebek/minutę), co sprawia, że jest to preferowany wybór w celu maksymalizacji wydajności produkcji.
Wysoka dokładność: W przypadku materiałów sypkich o umiarkowanej wadze jednostkowej wagi wielogłowicowe osiągają bardzo wysoką dokładność ważenia (±0,1 g do ±1 g lub lepszą, w zależności od materiału i wagi docelowej). Algorytm łączony skutecznie kompensuje indywidualne wahania wsadu.
Szeroki zakres wagowy: Możliwość obsługi opakowań o wadze od kilku gramów do kilku kilogramów poprzez dostosowanie docelowej wagi i rozmiaru wiadra, co zapewnia dużą wszechstronność.
Idealny do materiałów sypkich: umożliwia płynne i wydajne przetwarzanie granulek, płatków, brył i innych materiałów sypkich.
Relatywnie łatwe czyszczenie i konserwacja: Posiada stosunkowo standaryzowaną konstrukcję; części mające kontakt z materiałem (podajnik wibracyjny, pojemniki) są zazwyczaj odłączalne w celu czyszczenia.
Wady
Problemy z materiałami o słabym przepływie: Materiały podatne na przywieranie, zbrylanie, tłuste lub wilgotne mogą łatwo zatykać podajnik wibracyjny, zasobniki buforowe lub pojemniki wagowe, co prowadzi do nierównomiernego podawania, zmniejszenia dokładności, a nawet zatrzymania maszyny.
Wyzwania związane z małymi/bardzo lekkimi materiałami: Ekstremalnie małe lub lekkie przedmioty (drobne nasiona, małe pigułki) są podatne na rozproszenie przepływu powietrza („odlatywanie”) w pojemnikach ważących, co powoduje utratę materiału. Zalety dokładności również maleją w przypadku bardzo małych wag docelowych.
Możliwe uszkodzenia delikatnych produktów: Ruch obrotowy podajnika wibracyjnego i pojemnika wyładowczego może powodować uderzenia i tarcie, co może prowadzić do uszkodzenia bardzo delikatnych produktów (chipsy ziemniaczane).
Trudności z materiałami o nieregularnym/splątanym kształcie: Długie, płaskie lub włókniste przedmioty mogą zaplątać się lub zablokować w prowadnicach podajnika wibracyjnego lub wlotach pojemników.
Podaje wagę, nie liczbę: Wyprowadza docelową wagę, a nie dokładną liczbę sztuk. Nieodpowiednie do zastosowań wymagających dokładnych ilości (przedmioty sprzedawane według liczby sztuk).
3. Elektryczny Maszyny liczące
Maszyny do butelkowania zliczają poszczególne elementy, wykorzystując separację fizyczną lub technologię rozpoznawania obrazu, i je liczą. Typowe typy obejmują:
Maszyna licząco-napełniająca: Przedmioty ustawiają się w kolejce na wibrujących szynach i są liczone za pomocą czujników fotoelektrycznych.
Maszyna inspekcyjna z kamerą CCD i funkcją liczenia: Szybkie kamery rejestrują obrazy spadających przedmiotów, a oprogramowanie do przetwarzania obrazu identyfikuje i liczy poszczególne jednostki.
Zalety
Zapewnia dokładną liczbę sztuk: Jedyne rozwiązanie dla zastosowań wymagających precyzyjnej liczby (produkty farmaceutyczne, żelki, cukierki, komponenty elektroniczne).
Doskonała obsługa materiałów o słabym przepływie: ogólnie rzecz biorąc przewyższa wagi wielogłowicowe w przetwarzaniu materiałów wilgotnych, oleistych lub lepkich, przy zmniejszonym ryzyku zatykania.
Doskonale sprawdza się w przypadku małych granulek: Idealnie nadaje się do precyzyjnego i mało marnowanego liczenia małych tabletek, nasion i cukierków.
Skuteczne radzenie sobie z nieregularnymi kształtami: Zaawansowani liczniki wzrokowe potrafią dokładnie identyfikować i liczyć przedmioty o zróżnicowanej i trudnej geometrii.
Małe straty materiału: Liczenie zazwyczaj pozwala uniknąć odwracania pojemnika wagowego, minimalizując straty spowodowane „odlatywaniem” lub resztkami produktu.
Niski poziom hałasu: Mniejsza liczba elementów wibracyjnych w porównaniu do wag wielogłowicowych zazwyczaj przekłada się na niższy poziom hałasu.
Wady
Niższa prędkość: Prędkość absolutna jest zazwyczaj niższa niż w przypadku wag wielogłowicowych (szczególnie w przypadku małych przedmiotów). Szybkie liczniki wizyjne mogą osiągać 100-150 sztuk, ale przekłada się to na niższe prędkości pakowania (60-90 saszetek/minutę dla opakowań po 100 sztuk) w porównaniu z szybkimi wagami.
Dokładność wagi zależy od jednorodności jednostki: Dokładność liczenia wynosi 100%, ale dokładność wagi paczki zależy wyłącznie od spójnej wagi poszczególnych przedmiotów. Znaczne wahania wagi (nieregularne rozmiary suszonych owoców, orzechów) powodują duże wahania wagi paczki.
Wrażliwość na zlepianie się przedmiotów: Jeśli dwa lub więcej przedmiotów skleja się ze sobą i jest liczone jako jeden, następuje zaniżenie wyniku. (Przykład rozwiązania: Nasz specjalistyczny licznik słodyczy radzi sobie z zlepianiem się dzięki 4 kluczowym cechom:)
Mieszadło z kolcami do podawania żelków: zapobiega układaniu się żelków w pionie.
Wałek rozprowadzający zapobiegający zbrylaniu: zapewnia równomierne rozprowadzanie partii materiału, zapobiegając przywieraniu.
Panele z wgłębieniami teflonowymi: całkowicie oddzielają żelki i umożliwiają płynne, szybkie przesuwanie.
Powiększony otwór wylotowy PTFE: zmniejsza zatykanie, zwiększając prędkość o 58%.
Dobór skomplikowanego sprzętu: Różne typy liczników różnią się znacząco pod względem przydatności materiałów, dlatego dobór optymalnych rozwiązań wymaga specjalistycznej wiedzy i testów.
Wysoki koszt systemów wizyjnych: Początkowa inwestycja w wydajne systemy wizyjnego liczenia może być znacząca i często przekraczać koszty wag wielogłowicowych.
Ograniczone możliwości w przypadku dużych/ciężkich przedmiotów: Liczenie bardzo dużych kawałków (całych tabliczek czekolady, dużych zabawek) jest często niepraktyczne pod względem konstrukcyjnym, wolniejsze i mniej opłacalne niż stosowanie wag wielogłowicowych.
4. Podsumowanie i przewodnik po wyborze sprzętu
Funkcja | Poleć wagę wielogłowicową | Poleć maszynę do automatycznego liczenia |
Wymagania podstawowe | Priorytetem jest docelowa waga; dąż do maksymalnej prędkości i wydajności | Dokładna liczba sztuk jest niezbędna, a właściwości materiału uniemożliwiają ważenie |
Płynność materiału | Dobry (suchy, sypki) | Słaby/średni (tłusty, wilgotny, lepki, podatny na tworzenie się mostków) |
Forma materiału | Głównie granulki, płatki, kawałki | Głównie drobne cząstki, mikrogranulki, kształty nieregularne, płaskie, wydłużone przedmioty |
Waga indywidualna | Cząsteczki średnie do dużych lub małe, ale jednorodne | Bardzo małe przedmioty lub przedmioty o dużej zmienności wagi, wymagające liczenia sztuk |
Dokładność pakowania | Wysoka dokładność pomiaru wagi (±0,1 g – ± 1 g) | Dokładność liczenia 100% (Dokładność ważenia zależy od jednorodności poszczególnych sztuk) |
Prędkość | Bardzo wysokie (100-300+ saszetek/minutę) | Średnio-wysoki (zależy od rozmiaru przedmiotu i technologii liczenia; zwykle niższy niż w przypadku wag) |
Aplikacje | Przekąski (chipsy ziemniaczane/orzechy/słodycze), mrożonki, karma dla zwierząt, ziarna kawy, sprzęt, granulaty chemiczne | Produkty farmaceutyczne (tabletki/kapsułki), suplementy, nasiona, żelki, komponenty elektroniczne, artykuły o dużej wartości sprzedawane na sztuki |
5. Najlepsze zalecenia dotyczące praktyk wspierających wybór produktów
Przeprowadź rygorystyczne testy materiałowe: Przekaż rzeczywiste próbki materiałów do ruidapacking w celu przeprowadzenia testów. Zobacz z pierwszej ręki możliwości przetwarzania sprzętu, dokładność, szybkość i utratę materiału w przypadku konkretnego produktu.
Zaplanuj przyszłe potrzeby produkcyjne: Jeśli w przyszłości będziesz pakować materiały o różnych właściwościach, priorytetem będzie sprzęt kompatybilny lub elastyczny, umożliwiający obsługę różnorodnych produktów.
Zapewnij bezproblemową integrację linii produkcyjnej: Zagwarantuj, że wybrany przez Ciebie sprzęt dozujący będzie płynnie integrował się zarówno z systemami podawania w górnym biegu linii (podnośniki, zasobniki magazynowe), jak i z maszyną pakującą w dolnym biegu linii.
Wydajność meczu: sprawdź zgodność prędkości i interfejsów mechanicznych/fizycznych, aby zapobiec powstawaniu wąskich gardeł.
Priorytetem jest wsparcie i serwis dostawców: Wybierz dostawcę posiadającego duże doświadczenie techniczne i udokumentowaną historię responsywnego, wysokiej jakości serwisu i wsparcia posprzedażowego.
Dzięki starannej ocenie kluczowych właściwości materiału i dogłębnemu zrozumieniu podstawowych zalet i ograniczeń wag wielogłowicowych oraz automatycznych maszyn do liczenia butelek, możesz pewnie wybrać najwłaściwsze, najskuteczniejsze i najbardziej ekonomiczne rozwiązanie dozujące dla Twojej linii pakującej gotowe woreczki.