- Thuis
- Blisterkaartverpakkingsmachine
Blisterkaartverpakkingsmachine
Blister card packing machine, often called cardboard packaging machine or blister card machines, automate the process of securely sealing products to pre-printed paperboard cards, typically combined with clear alu pvc blister, alu alu blister, or formed plastic trays. The main function is to protect the blister plate from being damaged. Key applications span diverse industries: pharmaceuticals (tablets, capsules), consumer goods (toys, electronics accessories, batteries), hardware & tools (fasteners, small hand tools), health & beauty (razors, cosmetics, oral care) and automotive parts. These machines efficiently handle product loading, card folding, blister sealing (heat or ultrasonic), and final closure. They are essential for creating tamper-evident, shelf-appealing packaging that enhances brand presence, provides product information, and protects items during shipping and handling. Ideal for medium to high-volume production of durable and display-oriented packages.
Sollicitatie:
Paper card packing machine can pack tablet blisters, capsule blisters and other items.

Werkingsprincipe
Paperboard Packaging Machine uses an automated process to place the blister sheet containing the tablets between two cardboards and then seals them, mainly to protect the blister sheet from being damaged.
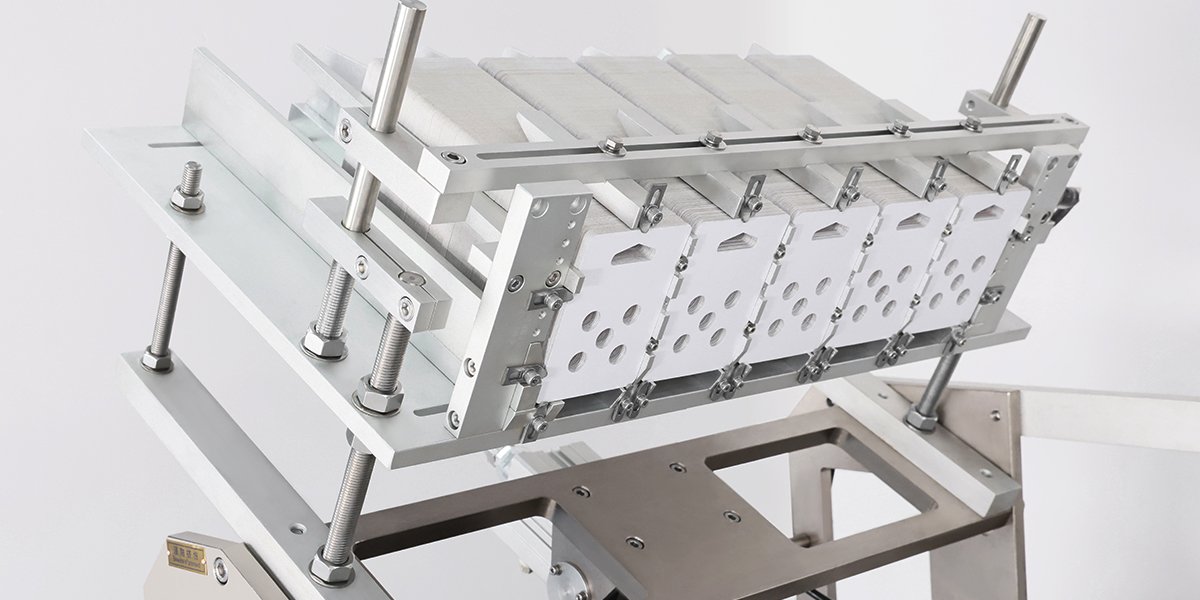
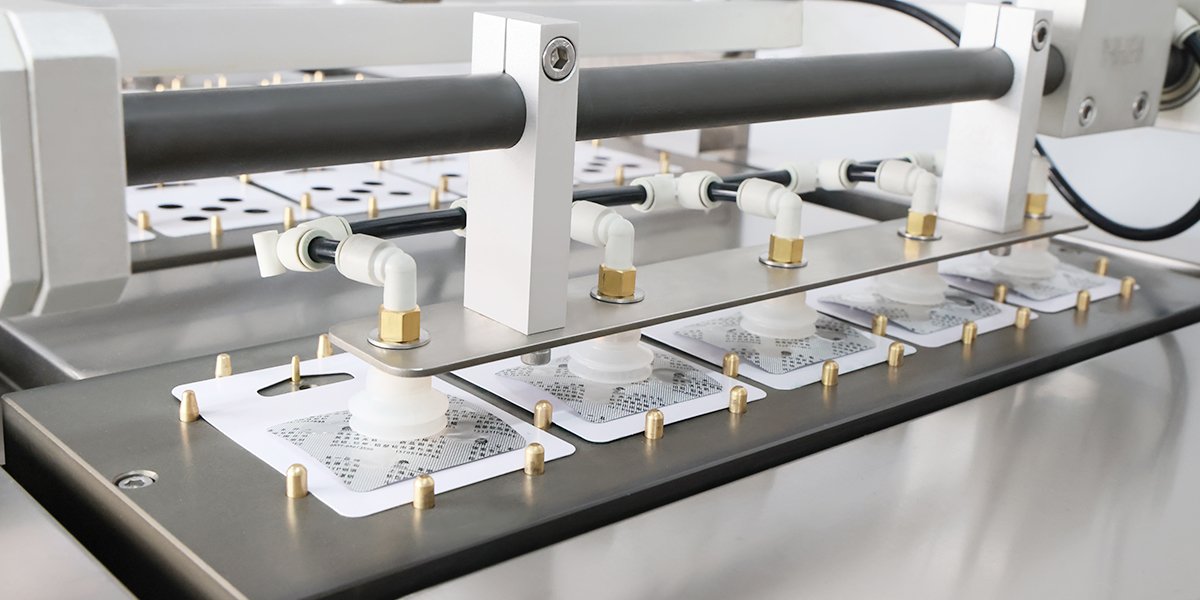
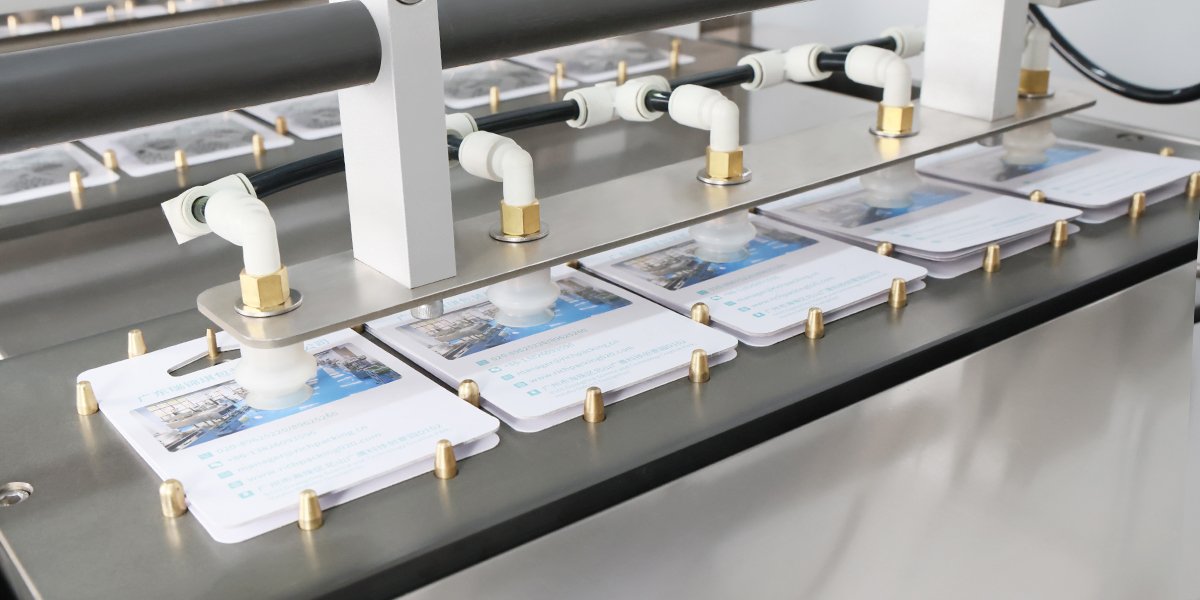
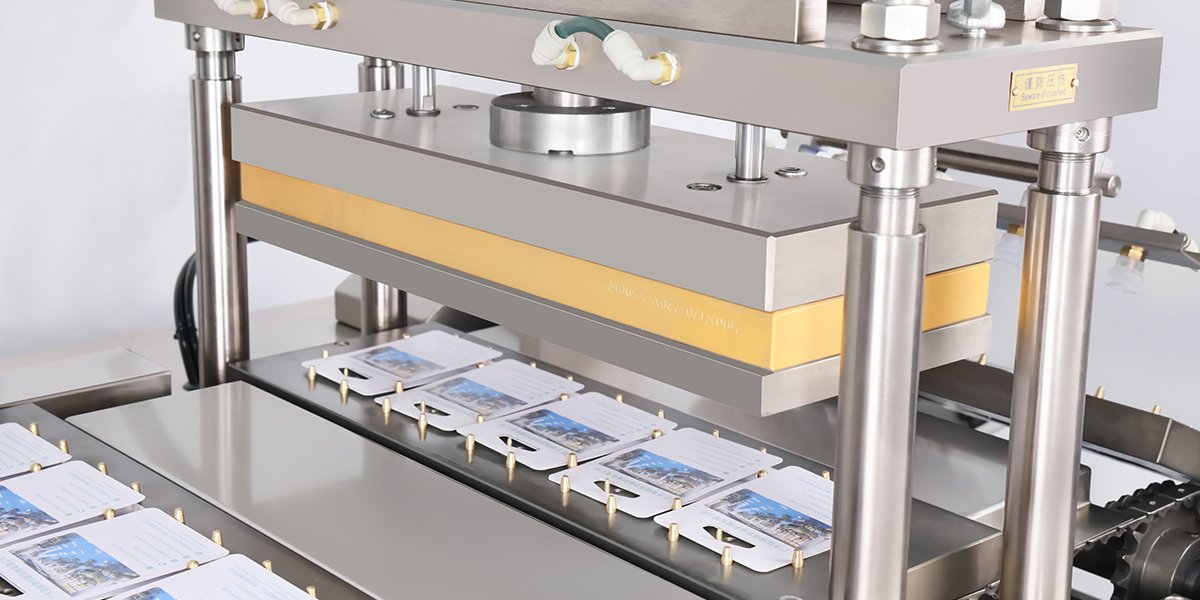
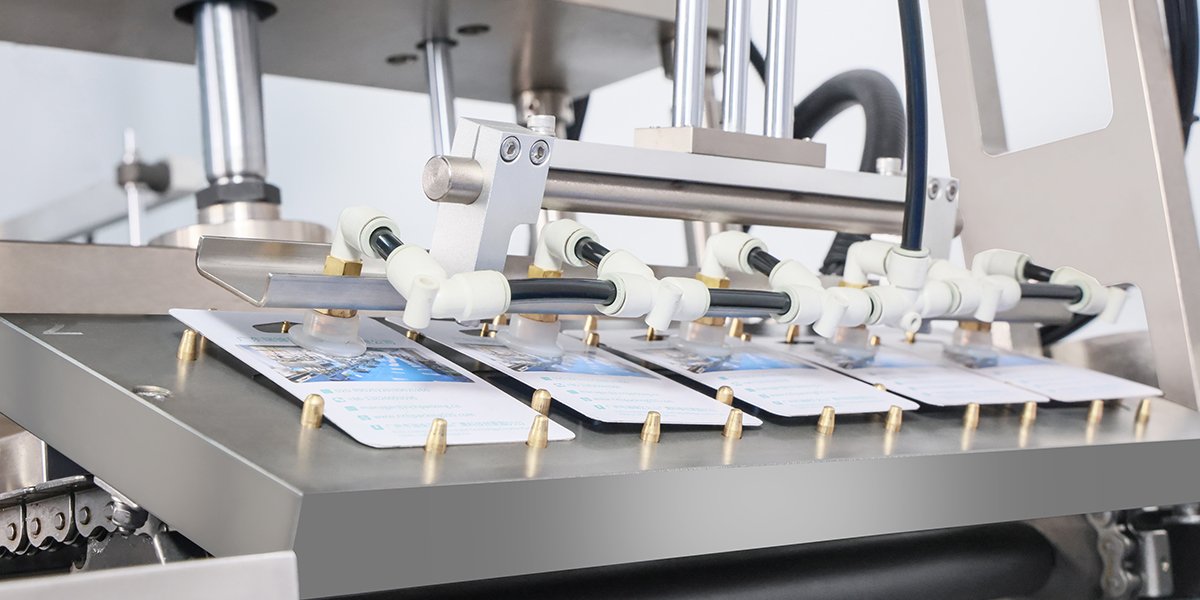
Technische parameters
Kies de beste machine op basis van de grootte van de zakjes.
Machine Mold | RD-BCP-350Pro | RD-BCP-500Pro | RD-BCP-650Pro |
Productiecapaciteit | 3,600 Plates/h | 5,400 Plates/h | 6,400 Plates/h |
Max. Forming Area | 330*210*65mm | 470*220*65mm | 630*220*65mm |
Paper Card Size | 350*220*0.5mm | 500*300*.05mm | 650*300*0.5mm |
Totaal vermogen | 11.8 kW | 12.8 kW | 15.8 kW |
Ondersteunende producten
NJP-3800D Automatische capsule-vulmachine
De NJP-3800D automatische capsule-vulmachine werkt door automatisch lege capsules aan te voeren, ze te vullen met poeder, ze te sluiten en ze af te geven voor verpakking.
Blister Packing Machine Manufacturer
Blister packing machine manufacturer offer various type machines that boosts output while lowering labor costs and material waste.
Tablet Compression Machine
Tablet compression machine is essential equipment for producing solid tablets by compacting powdered or granular materials.
Fortune 500 kwaliteitsleverancier
Features Advantage
Ruidapacking streeft ernaar machines te produceren met superieure kwaliteit die voldoen aan de GMP-normen en die tegelijkertijd efficiënte en praktische functies bieden.
Full Servo Control
The stroke can be accurate to 0.1mm, which is convenient for the alignment of paper cards and aluminum-plastic panels. The adjustment of the pulling distance of the product can be completed with one click on the touch screen.
Stronger Pressure Resistance
The heat sealing station mold is treated with Teflon, with better surface smoothness and pressure exceeding 100 kN.
Hard Anodized Molds
The 28-piece mold is made of high-grade aluminum alloy, the draw-out slot design allows mold changes within 15 minutes.
Wij staan voor u klaar met uitgebreide service
Wij staan u bij gedurende het gehele proces, van het kiezen van de juiste machine tot het goed onderhouden ervan gedurende uw hele leven.
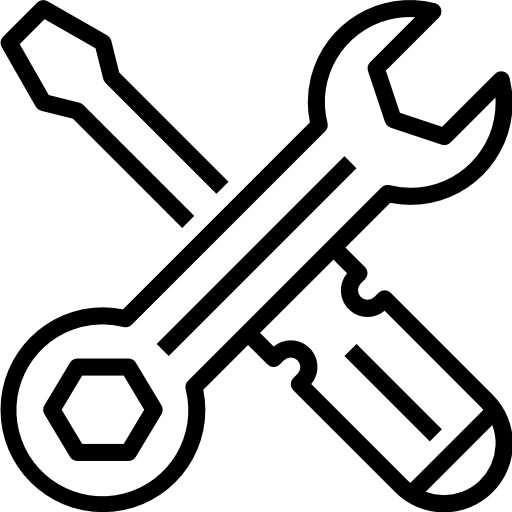
Levenslange garantie
Om langdurig optimale prestaties te garanderen, bieden we gratis reparatie binnen 3 jaar en gratis reserveonderdelen binnen 1 jaar. Daarna beloven we levenslang gratis technisch advies.
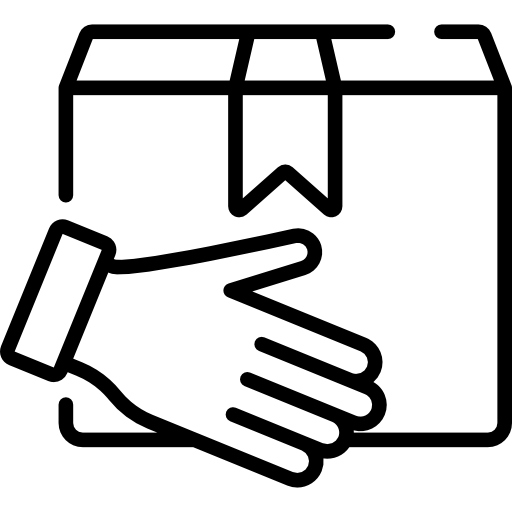
Snelle levering binnen 7 dagen
95% van onze standaardmachines hebben we op voorraad. In dat geval kan de levering binnen 7 dagen plaatsvinden. Voor producten op maat geldt een levertijd van slechts 20 dagen.
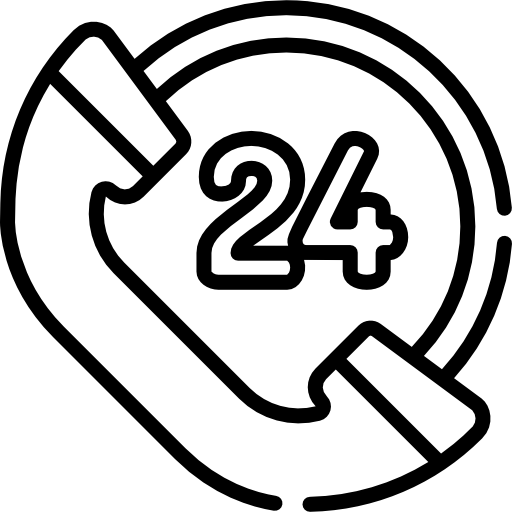
Online dienst
Onze deskundige klantexperts en technici richten zich op uw behoeften en lossen al uw problemen binnen 24 uur op, inclusief maar niet beperkt tot het beantwoorden van vragen en videogesprekken op afstand.
Veelgestelde vragen
Finding a truly reliable pharmaceutical blister card packaging machine can be a major headache for manufacturers. Common frustrations like poor sealing, product misalignment, and electrical safety concerns lead to wasted materials, rejected batches, operational downtime, and compliance risks. At Ruidapacking, we engineer our blister card machines to eliminate these exact problems, ensuring consistent quality, maximum efficiency, and uncompromised safety. Discover how our precision design solves the industry’s top three paper card packaging challenges.
1. Weak Sealing & High Reject Rates
The Industry Pain Point: Many blister card machines struggle with inconsistent or weak heat sealing. This results in blister packs detaching from the paperboard, compromised product integrity, and unacceptably high reject rates – directly hitting your bottom line through wasted materials and lost production time.
The Ruidapacking Solution: Our machines feature a heavy-duty heat sealing station engineered for perfection:
Massive, Controlled Pressure: We apply over 100 kN (10+ tons) of precisely calibrated pressure across the sealing area.
Premium Teflon-Coated Tooling: Sealing surfaces feature advanced Teflon (PTFE) coating, ensuring exceptional smoothness, consistent heat distribution, and preventing material sticking.
Result: Bonds are exceptionally strong and uniform every time. Dramatically reduced reject rates protect your profitability and ensure batch consistency.
2. Misaligned Cards & Poor Aesthetics
The Industry Pain Point: Achieving perfect alignment between the top and bottom paperboards is critical. Misaligned cards look unprofessional, can hinder functionality (e.g., hang holes blocked), and lead to consumer complaints or retailer rejections. Manual adjustments are time-consuming and often ineffective.
The Ruidapacking Solution: Precision alignment is built into our core design:
Dowel Pin Positioning System: We utilize a robust dowel pin location system within the tooling.
Guaranteed Registration: This system securely fixes each paperboard in its exact correct position on the mold before the heat sealing station begins.
Result: Perfect, consistent overlap of top and bottom cards every single cycle. Your finished packs look professional, function flawlessly, and meet the highest aesthetic standards.
3. Electrical Safety Hazards
The Industry Pain Point: Concerns about electrical safety, including potential leakage currents or unreliable components, are serious. These hazards endanger operators, violate strict cGMP and workplace safety regulations (like CE, UL), and create significant liability risks. Downtime for electrical repairs is costly.
The Ruidapacking Solution: Safety and reliability are non-negotiable:
World-Class Electrical Components: We exclusively integrate premium, globally recognized electrical brands (e.g., Siemens, Schneider Electric) known for their reliability and stringent safety certifications.
Robust Wiring & Grounding: Our machines are built with high-grade wiring harnesses and meticulous grounding practices exceeding international safety standards.
Result: Operators work with confidence. You achieve full compliance with cGMP and essential safety directives (CE marked), eliminate electrical hazard risks, and benefit from drastically reduced electrical failure downtime.
Conclusie
Stop battling unreliable blister card machines that compromise your quality, efficiency, and safety. Ruidapacking’s pharmaceutical paper card packaging machines are engineered from the ground up to solve the most persistent problems plaguing the industry. Our commitment to robust construction (100kN+ sealing), precision alignment (dowel pin system), and absolute electrical safety (premium components) delivers:
Higher Profitability: Slash reject rates and minimize costly downtime.
Flawless Quality: Guarantee perfectly aligned, professionally sealed packs.
Uncompromised Safety & Compliance: Meet cGMP and stringent electrical safety standards with confidence.
Binnen de verpakkingslijnen voor kant-en-klare zakjes hangt de keuze voor een meerkopsweger of een machine voor het tellen van capsules en tabletten als ondersteunende apparatuur voornamelijk af van de eigenschappen van het te verwerken materiaal. Deze twee technologieën bieden duidelijke voordelen en zijn geschikt voor specifieke toepassingen. Het kiezen van de verkeerde machine kan leiden tot verminderde efficiëntie, onvoldoende nauwkeurigheid, veel materiaalverspilling of zelfs operationele storingen.
De selectiecriteria, sterke punten en beperkingen van elk apparaat worden hieronder in detail geanalyseerd, op basis van de belangrijkste materiaaleigenschappen:
1. Materiaaleigenschappen
Fysieke vorm
Granulaat, vlokken, staafjes, brokken (gewone/onregelmatige vaste stoffen): Zowel een multiheadweger als een tel- en vulmachine zijn mogelijke opties; de uiteindelijke keuze hangt af van andere eigenschappen.
Fijnstof: Meestal beter geschikt voor telmachines.
Poeders, pasta's, vloeistoffen, viskeuze materialen: noch meerkops weegvulmachines, noch automatische telmachines zijn geschikt. Hiervoor zijn volumetrische vulapparatuur (vijzelvullers, zuigervullers, vloeistofvullers) of nettogewichten nodig.
Individueel gewicht/maat
Grote en relatief uniforme individuele wegingen: (grote koekjes, chocoladerepen, heel fruit, speelgoedonderdelen) Combinatiewegers met meerdere koppen bieden over het algemeen voordelen op het gebied van efficiëntie en kosteneffectiviteit.
Zeer klein of sterk variabel individueel gewicht: (kleine pillen, zaden, gummibeertjes, kleine hardware) Automatische elektronische telmachines blinken uit in precisie en minimaliseren verspilling. Multi-head wegers hebben moeite met de nauwkeurigheid van zeer lichte artikelen, en kleine artikelen zijn gevoelig voor verlies door "wegvliegen" (beluchting) in de weegbakken tijdens gebruik.
2. Meerkopswegers
Het materiaal wordt vanuit een trilgoot verdeeld over meerdere (meestal 8-24) onafhankelijke weegbakken (weeghoppers). Een computersysteem meet continu het gewicht in elke bak en gebruikt een gecombineerd weegalgoritme om snel de groep bakken te identificeren waarvan het gecombineerde gewicht het dichtst bij het streefgewicht ligt. De geselecteerde bakken lossen gelijktijdig in een opvangtrechter eronder en voeren het materiaal naar de verpakkingszak.
Voordelen
Hoge snelheid: het gecombineerde weegprincipe maakt uitzonderlijk hoge weegsnelheden mogelijk (meestal 100-200 zakjes/minuut, bij modellen met een hoge snelheid meer dan 300 zakjes/minuut). Dit is de voorkeurskeuze voor het maximaliseren van de productieoutput.
Hoge nauwkeurigheid: Voor vrijstromende materialen met een gemiddeld individueel gewicht bereiken multi-headwegers een zeer hoge weegnauwkeurigheid (±0,1 g tot ±1 g of beter, afhankelijk van het materiaal en het doelgewicht). Het combinatie-algoritme compenseert effectief individuele toevoervariaties.
Breed gewichtsbereik: Kan verpakkingsspecificaties verwerken van een paar gram tot meerdere kilo's door het doelgewicht en de emmergrootte aan te passen, en biedt daardoor een grote aanpasbaarheid.
Ideaal voor vrijstromende materialen: verwerkt korrels, vlokken, brokken en andere vrijstromende materialen soepel en efficiënt.
Relatief eenvoudig te reinigen en onderhouden: Heeft een relatief gestandaardiseerde structuur; onderdelen die in contact komen met het materiaal (vibratiegoot, emmers) kunnen doorgaans worden losgemaakt voor reiniging.
Nadelen
Problemen met slecht stromende materialen: Materialen die snel vastplakken, klonteren, olieachtig of vochtig zijn, kunnen gemakkelijk verstopt raken in de trilgoot, buffertrechters of weegbakken. Dit kan leiden tot ongelijkmatige invoer, een lagere nauwkeurigheid of zelfs tot stilstand van de machine.
Uitdagingen met kleine/zeer lichte materialen: Extreem kleine of lichte items (kleine zaadjes, kleine pillen) zijn gevoelig voor luchtverspreiding ("wegvliegen") in de weegschalen, wat leidt tot materiaalverlies. De nauwkeurigheidsvoordelen nemen ook af bij zeer kleine doelgewichten.
Mogelijke schade aan kwetsbare producten: Door de vallende beweging van de trilgoot en de losbak kunnen er schokken en wrijving ontstaan, waardoor zeer kwetsbare producten (aardappelchips) beschadigd kunnen raken.
Problemen met onregelmatige/verstrengelde materialen: Lange, platte of draderige voorwerpen kunnen verstrengeld raken of vastlopen in de trilgootrails of inlaten van de emmers.
Geeft gewicht, geen aantal: geeft een streefgewicht weer, geen exact aantal stuks. Niet geschikt voor toepassingen waarbij precieze hoeveelheden vereist zijn (artikelen verkocht per eenheid).
3. Elektrisch Telmachines
Telbottelmachines isoleren individuele items met behulp van fysieke scheiding of visuele herkenningstechnologie en tellen ze. Veelvoorkomende typen zijn:
Tel- en vulmachine: De artikelen komen in een rij op trilbanen terecht en worden geteld met behulp van foto-elektrische sensoren.
CCD-camera-inspectietelmachine: Hogesnelheidscamera's leggen beelden vast van vallende voorwerpen, waarna beeldverwerkingssoftware de afzonderlijke eenheden identificeert en telt.
Voordelen
Zorgt voor een nauwkeurig aantal stuks: de enige oplossing voor toepassingen waarbij nauwkeurige tellingen vereist zijn (farmaceutica, gummyberen, snoep, elektronische componenten).
Superieure verwerking van materialen met een slechte doorstroming: presteert over het algemeen beter dan wegers met meerdere koppen bij de verwerking van vochtige, olieachtige of plakkerige materialen met een lager risico op verstopping.
Uitstekend geschikt voor kleine pellets: ideaal voor het uiterst nauwkeurig en verspillingsvrij tellen van kleine pillen, zaden en snoepjes.
Effectief omgaan met onregelmatige vormen: geavanceerde visuele tellers kunnen nauwkeurig items met uiteenlopende en uitdagende vormen identificeren en tellen.
Laag materiaalverlies: door te tellen wordt het omkeren van de weegbak vermeden, waardoor het verlies door wegvliegend materiaal of productresten tot een minimum wordt beperkt.
Laag geluidsniveau: Minder trillende onderdelen vergeleken met wegers met meerdere koppen, wat doorgaans resulteert in een lager geluidsniveau.
Nadelen
Lagere snelheid: De absolute snelheid is over het algemeen lager dan bij wegers met meerdere koppen (vooral voor kleine artikelen). Hogesnelheidstellers met zichtbediening kunnen 100-150 stuks verwerken, maar dit vertaalt zich in lagere verpakkingssnelheden (60-90 zakjes/minuut voor verpakkingen van 100 stuks) in vergelijking met hogesnelheidstellers.
De nauwkeurigheid van het gewicht hangt af van de uniformiteit van de eenheid: de telnauwkeurigheid is 100%, maar de nauwkeurigheid van het pakketgewicht is volledig afhankelijk van het consistente gewicht van het individuele artikel. Aanzienlijke gewichtsvariaties (onregelmatige grootte van gedroogd fruit, noten) veroorzaken grote schommelingen in het pakketgewicht.
Gevoeligheid voor klontering van artikelen: Als twee of meer artikelen aan elkaar plakken en als één worden geteld, treedt er ondertelling op. (Voorbeeld van een oplossing: onze gespecialiseerde snoepteller pakt klontering aan met vier belangrijke kenmerken:)
Spiked Hopper Agitator: voorkomt dat de gummies verticaal opstapelen.
Antiklonterverdeelrol: Zorgt voor een gelijkmatige verdeling van de batch door aanhechting te voorkomen.
Teflon Dimple Panels: Volledig scheidende gomlagen voor soepel en snel glijden.
Vergrote PTFE-afvoerpoort: vermindert verstoppingen en verhoogt de snelheid met 58%.
Complexe apparatuurselectie: Verschillende soorten balies verschillen aanzienlijk in geschiktheid van materiaal. Voor een optimale selectie zijn deskundige kennis en tests vereist.
Hoge kosten voor visuele telsystemen: de initiële investering voor krachtige visuele telsystemen kan aanzienlijk zijn en overstijgt vaak de kosten van de multi-head weegmachine.
Beperkte mogelijkheden voor grote/zware artikelen: Het tellen van zeer grote stukken (hele chocoladerepen, groot speelgoed) is vaak structureel onpraktisch, langzamer en minder kosteneffectief dan het gebruik van wegers met meerdere koppen.
4. Samenvatting & Uitrustingsselectiegids
Functie | Aanbevolen multi-head weegmachine | Aanbevolen automatische telmachine |
Kernvereiste | Het streefgewicht is de prioriteit; streef naar maximale snelheid en efficiëntie | Nauwkeurige stuktelling is essentieel; of materiaaleigenschappen maken wegen ongeschikt |
Materiaalvloeibaarheid | Goed (droog, vrij vloeiend) | Slecht/Gemiddeld (Vettig, vochtig, plakkerig, vatbaar voor brugvorming) |
Materiële vorm | Voornamelijk korrels, vlokken, brokken | Voornamelijk fijne deeltjes, micropellets, onregelmatige vormen, platte, langwerpige voorwerpen |
Individueel gewicht | Middelgrote tot grote, of kleine maar uniforme deeltjes | Zeer kleine artikelen of artikelen met een grote gewichtsvariatie waarvoor een stuktelling nodig is |
Verpakkingsnauwkeurigheid | Hoge gewichtsnauwkeurigheid (±0,1 g – ± 1 g) | 100% telnauwkeurigheid (gewichtnauwkeurigheid is afhankelijk van de uniformiteit van het individuele stuk |
Snelheid | Zeer hoog (100-300+ zakjes/minuut) | Medium-hoog (afhankelijk van de grootte van het artikel en de teltechnologie; doorgaans lager dan wegers) |
Toepassingen | Snacks (chips/noten/snoep), diepvriesvoer, dierenvoer, koffiebonen, ijzerwaren, chemische korrels | Geneesmiddelen (tabletten/capsules), supplementen, zaden, snoepgoed, elektronische componenten, waardevolle artikelen verkocht per stuk |
5. Aanbevolen werkwijzen voor het ondersteunen van productselectie
Voer grondige materiaaltests uit: stuur echte materiaalmonsters naar Ruidapacking voor tests. Ervaar zelf de verwerkingscapaciteiten, nauwkeurigheid, snelheid en het materiaalverlies van de apparatuur met uw specifieke product.
Houd rekening met toekomstige productiebehoeften: als u in de toekomst materialen met verschillende eigenschappen wilt verpakken, geef dan prioriteit aan apparatuur die compatibel of flexibel is om uiteenlopende producten te verwerken.
Zorg voor naadloze integratie in de productielijn: Zorg dat de door u gekozen doseerapparatuur naadloos integreert met zowel de stroomopwaartse toevoersystemen (liften, opslagbakken) als de stroomafwaartse verpakkingsmachine.
Matchprestaties: controleer de compatibiliteit op het gebied van snelheid en mechanische/fysieke interfaces om knelpunten te voorkomen.
Geef prioriteit aan leveranciersondersteuning en -service: selecteer een leverancier met sterke technische expertise en een bewezen staat van dienst op het gebied van responsieve, hoogwaardige aftersalesservice en -ondersteuning.
Door de belangrijkste eigenschappen van uw materiaal zorgvuldig te evalueren en de belangrijkste sterke en zwakke punten van multikopwegers en automatische flessentelmachines grondig te begrijpen, kunt u met vertrouwen de meest geschikte, efficiënte en kosteneffectieve doseeroplossing selecteren voor uw verpakkingslijn voor kant-en-klare zakken.
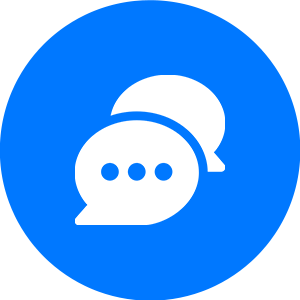