В производстве таблеток таблеточный пресс Это критически важный элемент оборудования. Его работа напрямую влияет на качество таблеток, эффективность производства и общее соответствие требованиям. Однако использование таблеточного пресса иногда может вызывать различные проблемы, такие как закрытие таблеток, прилипание, ламинирование и неравномерная масса таблеток. Эти проблемы не только снижают производительность, но и увеличивают затраты из-за отходов. Для решения этих распространённых проблем с таблетками важно понимать их причины и внедрять правильные решения для обеспечения более плавного рабочего процесса и повышения качества продукции.
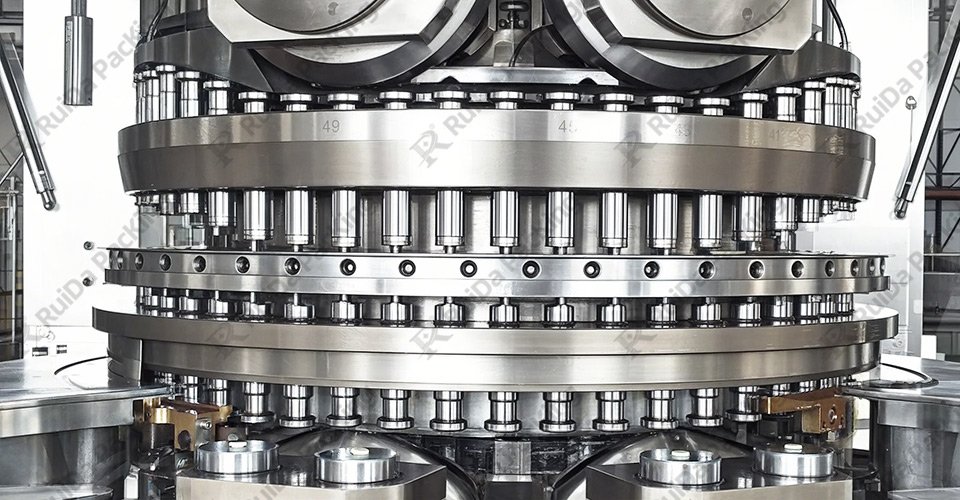
Обзор распространенных проблем с планшетами
При эксплуатации таблеточный прессТакие проблемы, как залипание, прилипание, расслоение, сколы и колебания веса, встречаются часто. Эти проблемы могут возникнуть из-за неправильной настройки оборудования, несоответствия исходных материалов или изменений в производственной среде. Каждая из этих проблем может повлиять на внешний вид, стабильность и эффективность таблетки. К счастью, многие из этих проблем можно решить, корректируя параметры производства, оптимизируя состав материалов и обеспечивая надлежащее обслуживание оборудования.
Проблемы с ограничением
Отслоение происходит, когда верхний слой таблетки отделяется или трескается после прессования, часто из-за неравномерного распределения давления или недостаточного содержания связующих веществ в составе. Эта проблема — одна из наиболее распространённых при производстве таблеток и обычно проявляется в процессе выталкивания или вскоре после него.
Решения:
– Отрегулируйте параметры давления таблеточного пресса, чтобы обеспечить равномерное распределение давления во время прессования.
– Увеличьте долю связующих веществ в рецептуре, чтобы улучшить сцепление частиц и снизить вероятность слеживания.
– Улучшить гладкость штампов для уменьшения сопротивления при выталкивании.
Внедрив эти изменения, вы можете значительно свести к минимуму возникновение отложений и гарантировать сохранение структурной целостности таблеток.
Проблемы с застреванием
Прилипание происходит, когда материал таблетки прилипает к поверхности пуансона или матрицы, что может привести к образованию шероховатостей на поверхности таблетки или даже к её разрушению. Прилипание часто связано с высоким содержанием влаги в материале или проблемами со вспомогательными веществами, используемыми в составе.
Решения:
– Контролируйте влажность материала таблеток, используя осушители или улучшая условия хранения материала для снижения избыточной влажности.
– Регулярно очищайте и полируйте пуансоны и матрицы, чтобы они оставались гладкими и свободными от остатков.
– Чтобы уменьшить прилипание, добавьте в рецептуру антиадгезионные агенты, такие как тальк или стеарат магния.
Правильный контроль влажности и обслуживание пресс-формы имеют решающее значение для предотвращения прилипания, а оптимизация рецептуры еще больше снизит вероятность возникновения этой проблемы.
Проблемы с ламинированием
Ламинирование — это разделение таблетки на отдельные слои, которое может произойти из-за недостаточного давления при прессовании или некачественной грануляции. Ламинированные таблетки могут легко ломаться, что снижает качество продукта.
Решения:
– Увеличьте давление на таблеточный пресс, чтобы обеспечить плотное прессование гранул в твердую форму.
– Проверьте процесс грануляции, чтобы убедиться, что размер частиц однороден и гранулы имеют хорошие свойства текучести.
– Ввести в рецептуру более качественные связующие вещества для улучшения сцепления таблеток и предотвращения расслоения.
Выполняя эти корректировки, вы можете гарантировать, что ваши таблетки будут правильно формироваться во время сжатия и что не будет происходить расслоения.
Проблемы с чипированием
Сколы возникают, когда края таблеток отламываются или повреждаются, что часто вызвано чрезмерной твёрдостью таблеток или неправильным обращением с ними после прессования. Это может привести к косметическим дефектам и повлиять на стабильность продукта во время упаковки и транспортировки.
Решения:
– Уменьшите твердость таблетки, регулируя давление, прилагаемое во время прессования, гарантируя, что таблетки будут прочными, но не слишком твердыми.
– Улучшить процесс сушки, чтобы таблетки не пересушились, что может привести к их хрупкости и склонности к растрескиванию.
– Нанесите защитное покрытие на поверхность таблетки, чтобы защитить ее от повреждений во время обработки и транспортировки.
Оптимизировав твердость и обеспечив надлежащее обращение, можно предотвратить сколы и сохранить структурную целостность таблеток на протяжении всего процесса производства.
Проблемы с изменением веса
Ещё одной критической проблемой при производстве таблеток является колебание веса таблеток, приводящее к нестабильным дозировкам и потенциальным проблемам с нормативными требованиями. Эта проблема обычно возникает из-за неравномерного потока материала или нестабильной системы наполнения.
Решения:
– Улучшить последовательность работы системы подачи, чтобы гарантировать подачу одинакового количества материала на каждую таблетку.
– Используйте материалы с лучшей текучестью, чтобы обеспечить равномерное распределение в полости матрицы.
– Регулярно калибруйте таблеточный пресс, чтобы поддерживать точность процессов наполнения и прессования.
Обеспечение постоянного потока материала и надлежащей калибровки машины снизит колебания веса, что приведет к получению более однородных таблеток и повышению качества продукции.
Предотвращение распространенных проблем с таблетировочными прессами
Чтобы предотвратить распространённые проблемы с таблетками, необходимо принимать профилактические меры. Регулярное техническое обслуживание оборудования, поддержание его в чистоте, контроль производственной среды (особенно влажности и температуры) и использование высококачественного сырья — всё это важные шаги для обеспечения бесперебойного производства таблеток. Правильное обслуживание оборудования и контроль производства сократят время простоя, повысят его эффективность и обеспечат стабильное качество каждой партии.
Таблица профилактических мер
Общая проблема | Профилактические меры |
Укупорка | Отрегулируйте давление, улучшите гладкость штампа, увеличьте долю связующего |
Прилипание | Контролируйте влажность, очищайте и полируйте штампы, увеличивайте антиадгезионные свойства |
Ламинирование | Увеличьте давление, оптимизируйте грануляцию, добавьте лучшие связующие вещества |
Сколы | Уменьшить твердость, контролировать высыхание, нанести защитное покрытие |
Изменение веса | Улучшить систему подачи, использовать более сыпучие материалы, регулярно калибровать оборудование |
Проводя регулярные проверки, обслуживая оборудование и оптимизируя методы производства, вы можете значительно сократить возникновение этих проблем с таблетками и повысить общую эффективность производства.
Заключение
Такие распространённые проблемы с таблетками, как залипание, слипание, расслоение, сколы и изменение веса, могут создавать трудности при производстве таблеток, но у каждой проблемы есть свои причины, которые можно устранить с помощью целенаправленных решений. Регулярное обслуживание оборудования, мониторинг производственной среды и оптимизация состава таблеток позволят повысить качество продукции и сократить время простоя. Контроль производственного процесса — ключ к обеспечению соответствия каждой таблетки требуемым стандартам качества.