O processo de enchimento de cápsulas exige precisão e eficiência, o que pode ser alcançado com o uso de máquinas de enchimento de cápsulas líquidas. Neste post, exploraremos os vários aspectos do domínio dessas máquinas, desde a compreensão de seus fundamentos até a exploração de recursos avançados e considerações de custo.
O que são máquinas de enchimento de cápsulas líquidas?
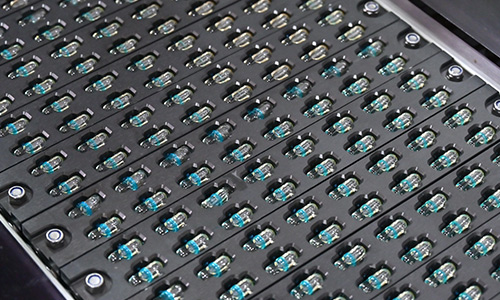
As máquinas de envase de cápsulas líquidas são equipamentos automatizados projetados para envasar formulações líquidas em cápsulas vazias de forma eficiente e precisa. Essas máquinas eliminam a necessidade de trabalho manual tedioso e garantem uma dosagem consistente. As máquinas de envase de cápsulas líquidas funcionam primeiro separando as cápsulas vazias em seus componentes individuais, ou seja, o corpo e a tampa. A formulação líquida é então dispensada com precisão em cada corpo usando um sistema de bomba de pistão ou peristáltica. A tampa é então selada no corpo, completando o enchimento da cápsula.
Componentes e estrutura de máquinas de enchimento de cápsulas líquidas
As máquinas de enchimento de cápsulas líquidas consistem em vários componentes, incluindo um carregador de cápsulas, funil, sistema de dosagem, sistema de selagem e painel de controle. Cada componente desempenha um papel vital no processo de enchimento e contribui para a eficiência geral da máquina.- Importância de cada componente no processo de enchimento
- O carregador de cápsulas garante o fornecimento suave e contínuo de cápsulas vazias, permitindo que a máquina opere sem interrupções.
- O funil retém a formulação líquida e a alimenta ao sistema de dosagem, que mede com precisão a quantidade desejada de líquido.
- O sistema de vedação veda com segurança as cápsulas cheias, evitando qualquer vazamento ou contaminação.
As máquinas de envase de cápsulas líquidas são normalmente projetadas com uma estrutura compacta e ergonômica para otimizar o aproveitamento do espaço. São fabricadas com materiais de alta qualidade e resistentes à corrosão, garantindo a longevidade da máquina. As máquinas também são equipadas com interfaces fáceis de usar e controles intuitivos para facilitar a operação.
Tipos de cápsulas líquidas e sua aplicação
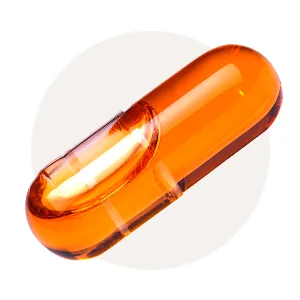
As cápsulas líquidas estão disponíveis em vários formatos, incluindo cápsulas gelatinosas cápsulas, Cápsulas de HPMC (hipromelose), e cápsulas de gelatina.
- Cápsulas de gelatina mole são amplamente utilizados e conhecidos por sua fácil deglutição.
- Cápsulas de HPMC são adequados para produtos vegetarianos e veganos.
- Cápsulas de gelatina são comumente usados em aplicações farmacêuticas.
Cápsulas líquidas encontram aplicações em diferentes indústrias, incluindo farmacêutica, nutracêutica e cosmecêutica. São usadas para encapsular diversos líquidos, como vitaminas, extratos de ervas, óleos essenciais e suplementos alimentares.
Ao selecionar o tipo de cápsula líquida apropriado, fatores como compatibilidade com a formulação líquida, perfil de liberação desejado e preferências do consumidor-alvo devem ser considerados. Compreender esses fatores ajudará na escolha do tipo de cápsula mais adequado para um produto específico.
Como funcionam as máquinas de enchimento de cápsulas líquidas?
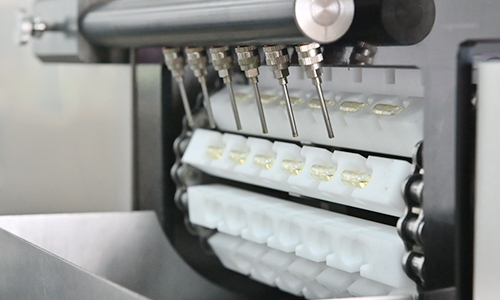
Máquinas de enchimento de cápsulas líquidas são equipamentos essenciais na indústria farmacêutica para a fabricação eficiente e precisa de cápsulas líquidas. Essas máquinas são compostas por diversos componentes e passam por uma série de etapas para garantir o enchimento seguro e preciso do líquido nas cápsulas. Vamos entender como essas máquinas funcionam:
Alimentação por cápsula
O processo começa com a introdução de cápsulas vazias na máquina de envase. Essas cápsulas geralmente são feitas de gelatina ou de uma alternativa vegetariana, que se dissolve facilmente no corpo.
Separação
Após o enchimento das cápsulas vazias, a máquina separa as metades superior e inferior, preparando-as para o processo de enchimento. Essa separação garante que o líquido seja dispensado com precisão em cada cápsula.
Posto de gasolina
As cápsulas separadoras seguem para a estação de envase, onde a máquina as enche com a formulação líquida desejada. O sistema de envase pode utilizar diversos mecanismos, incluindo bombas, bombas peristálticas ou envasadoras de pistão, dependendo dos requisitos da máquina específica.
Dosagem de precisão
As máquinas de envase de cápsulas líquidas garantem a dosagem precisa da formulação líquida em cada cápsula. Máquinas avançadas são equipadas com sensores e controles que regulam o processo de envase, garantindo consistência e precisão na quantidade de líquido dispensado.
Resselagem
Após o enchimento das cápsulas, a máquina fecha novamente as metades superior e inferior para encapsular o líquido. Esse processo de selagem precisa ser eficiente para evitar vazamentos ou contaminação.
Polimento
Algumas máquinas incluem uma etapa de polimento, onde o excesso de pó ou líquido ao redor das cápsulas é removido, deixando cápsulas limpas e adequadamente preenchidas.
Ejeção
Por fim, as cápsulas cheias e seladas são ejetadas da máquina, prontas para processamento posterior, como fechamento, rotulagem ou embalagem.
Perguntas frequentes sobre problemas comuns encontrados durante o enchimento de cápsulas líquidas
P: O que são processos de enchimento de cápsulas líquidas?
R: Os processos de envase de cápsulas líquidas envolvem o encapsulamento de líquidos, semissólidos e substâncias farmacêuticas em suspensão em cápsulas de gelatina dura ou mole. Isso é feito por meio de máquinas especiais para envase de cápsulas.
P: Quais são os problemas comuns encontrados durante o enchimento de cápsulas líquidas?
R: Problemas comuns incluem vazamento durante o encapsulamento, enchimento de dosagem incorreta, endurecimento da cápsula, instabilidade do ingrediente ativo e danos ou deformação das cápsulas.
P: O que causa vazamento durante o encapsulamento no enchimento de cápsulas líquidas?
R: O vazamento pode ocorrer devido a fatores como mudanças de temperatura ou pressão, o que leva à quebra do invólucro da cápsula, ou devido à vedação inadequada durante o processo de enchimento.
P: Como podemos evitar o preenchimento incorreto da dosagem no enchimento de cápsulas líquidas?
R: Manter e calibrar regularmente a máquina de envase e garantir que as especificações e instruções corretas sejam seguidas pode evitar o envase com dosagem incorreta.
P: O que pode causar o endurecimento da cápsula?
R: O endurecimento da cápsula pode ocorrer devido à alta temperatura, baixa umidade do ambiente ou uso de composição incorreta da cápsula de gelatina.
P: Como a instabilidade do ingrediente ativo é um problema no enchimento de cápsulas líquidas?
R: Se o ingrediente ativo não for estável, ele pode se degradar ou mudar ao longo do tempo, levando a variações na eficácia ou até mesmo problemas de segurança no produto final.
P: Por que ocorre o dano ou a deformação das cápsulas?
R: Danos ou deformações podem ser causados por manuseio inadequado, condições inadequadas de armazenamento ou por defeitos na máquina de enchimento de cápsulas.
P: Como é possível evitar danos ou deformações nas cápsulas?
R: A manutenção regular e adequada do equipamento de enchimento, o manuseio cuidadoso das cápsulas e as condições adequadas de armazenamento podem ajudar a evitar danos ou deformações das cápsulas.
P: Quais são algumas soluções para combater os problemas comuns encontrados durante o enchimento de cápsulas líquidas?
R: O treinamento adequado do pessoal, o uso de materiais de alta qualidade, a manutenção programada e a calibração do equipamento, além de seguir meticulosamente o protocolo, podem ajudar a evitar ou minimizar esses problemas comuns.
Conclusão
No mundo acelerado da fabricação farmacêutica, dominar a máquina de envase de cápsulas líquidas é essencial para alcançar eficiência e manter a alta qualidade do produto. Exploramos os fundamentos dessas máquinas, suas vantagens, componentes e tipos de cápsulas líquidas. Discutimos considerações sobre técnicas de envase, materiais das cápsulas, controle de qualidade, solução de problemas, automação, análise de custos e melhores práticas para um envase ideal.