블리스터 포장기 are essential in the pharmaceutical and consumer goods industries, ensuring that products are securely packaged and protected. Proper installation and maintenance of these machines are crucial for efficient and uninterrupted operations. In this guide, we’ll walk you through the steps for installing a blister packing machine, as well as the key maintenance practices to keep it running smoothly.
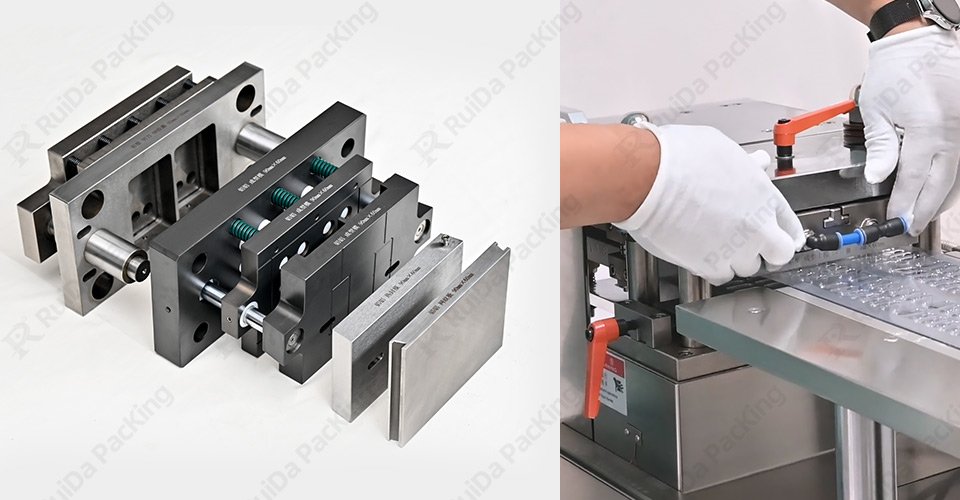
Understanding Blister Packing Machines
Before diving into the installation and maintenance processes, it’s important to understand the basic components and functions of a blister packing machine. These machines are designed to form, fill, and seal blister packs, which are commonly used for packaging tablets, capsules, and other small items. The machine typically consists of the following components:
형성 스테이션
The forming station is the initial and foundational step in the blister packaging process. This station uses either thermoforming or cold forming techniques to create blister cavities from a plastic film or aluminum foil. These cavities are designed to hold the individual products securely. In thermoforming, the plastic film is heated until it becomes pliable and then molded into the desired shape using a forming die. Cold forming, on the other hand, involves shaping softer materials without the use of heat. The precision and consistency of the forming station are crucial for ensuring that each blister is identical, providing both protection and a professional appearance for the packaged products.
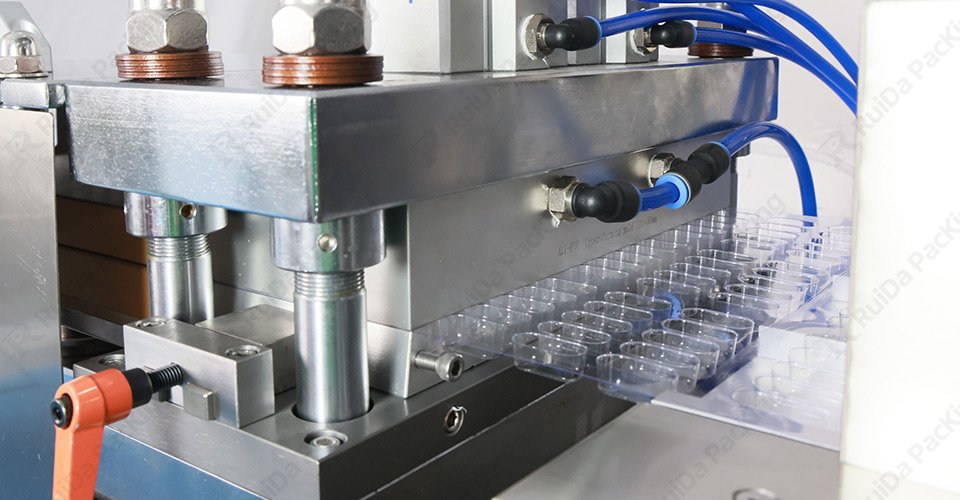
Feeding Station
The feeding station is responsible for accurately placing products into the formed blister cavities. This process can be either manual or automated, depending on the design of the machine and the nature of the products being packaged. Automated feeding systems typically use conveyors, vibratory feeders, or robotic arms to position and dispense the products into the blisters with high precision. The accuracy and efficiency of the feeding process are essential because any misalignment or missing product can compromise the integrity and quality of the final packaging.
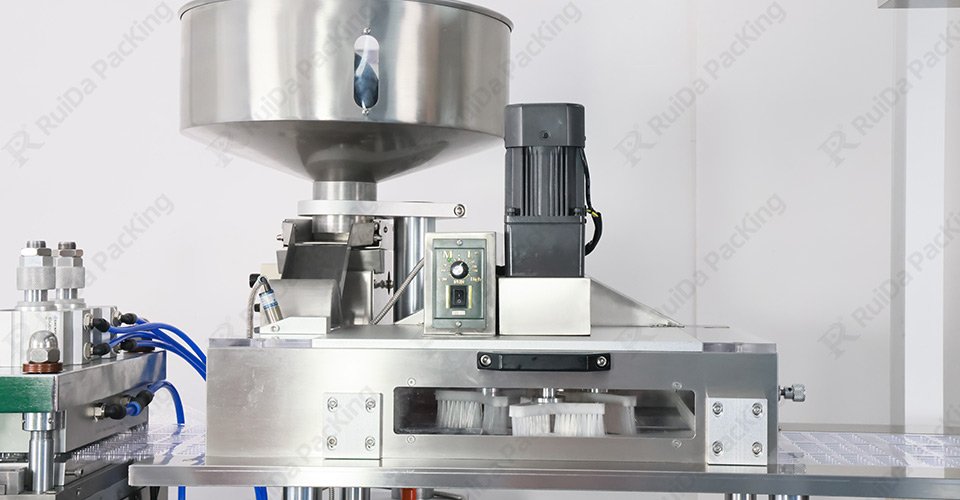
Sealing Station
At the sealing station, the filled blisters are sealed with a lidding material, usually aluminum foil. This sealing process can be achieved through heat sealing or cold sealing methods, depending on the materials and desired seal strength. Heat sealing uses heated elements to fuse the lidding material to the plastic blister, while cold sealing employs a pressure-sensitive adhesive. The sealing station must be precisely controlled in terms of temperature, pressure, and speed to ensure a strong and airtight seal that protects the product from environmental factors such as moisture and contamination.
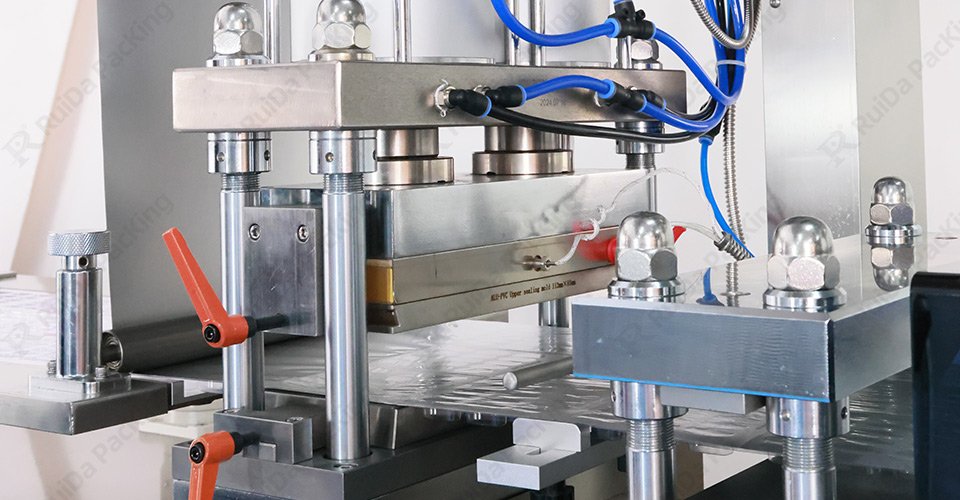
Cutting Station
The cutting station is the final step in the blister packaging process. Here, the sealed blister packs are cut into individual units for distribution and use. This cutting process requires high precision to ensure that each pack has clean, uniform edges. Various cutting techniques can be employed, including mechanical cutting, laser cutting, and die-cutting, depending on the machine’s design and the material’s properties. An efficient cutting station enhances production speed and ensures that each package maintains a professional appearance.
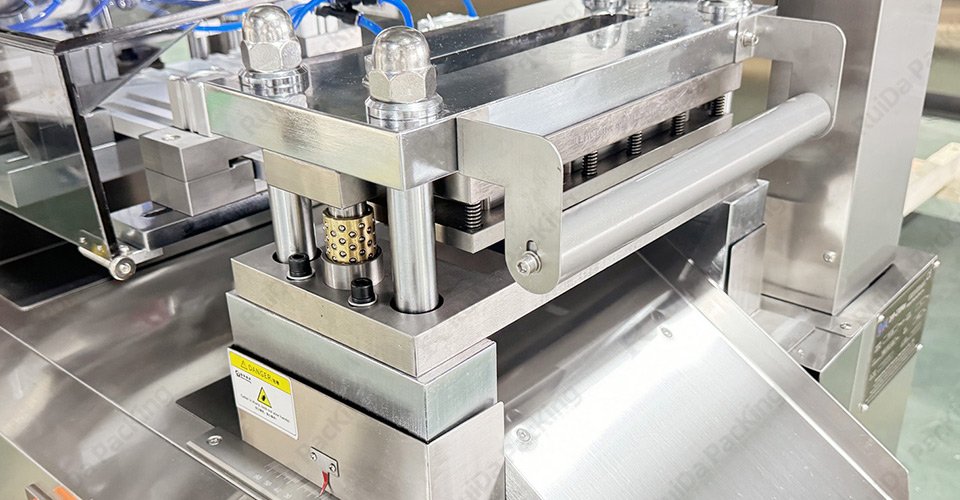
Control Panel
The control panel serves as the central interface for operating and monitoring the blister packing machine. It allows the operator to set and adjust parameters such as temperature, pressure, speed, and feed rate. Additionally, the control panel provides real-time monitoring and displays the machine’s operational status and any error alerts. Modern control panels often feature touchscreens with user-friendly interfaces, making it easier for operators to manage the machine. By using the control panel, operators can ensure precise control over the entire packaging process, maintaining consistent quality across all batches.
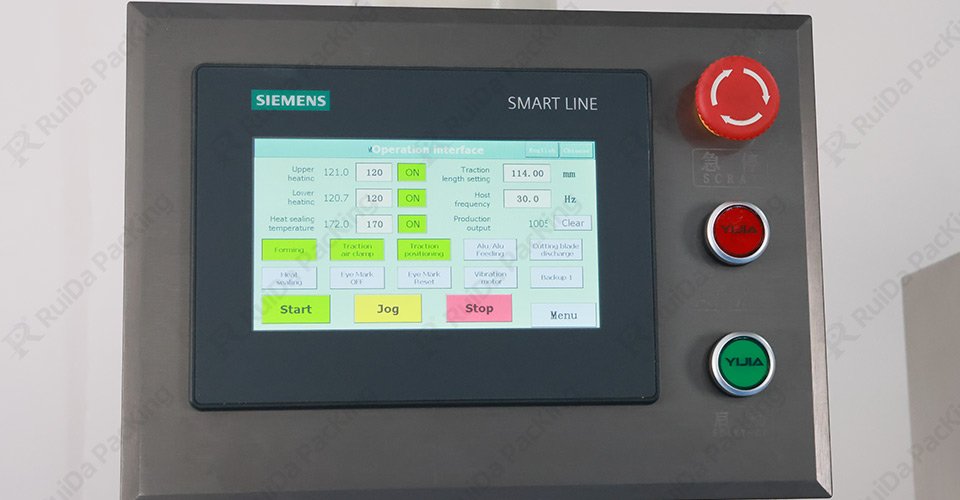
Installation of Blister Packing Machine
1. Site Preparation
The first step in installing a blister packing machine is preparing the site. Ensure that the location is clean, well-ventilated, and free from dust and contaminants. The area should also have adequate lighting and be spacious enough to accommodate the machine and allow for easy movement around it.
2. Utility Connections
Blister packing machines require various utilities to operate effectively. Ensure that the following connections are available and properly installed:
– Electricity: Confirm that the power supply meets the machine’s specifications, typically requiring a stable voltage and proper grounding.
– Compressed Air: The machine may require a source of compressed air for certain functions. Ensure that the air supply is clean, dry, and at the correct pressure.
– Water Supply: Some machines may need a water supply for cooling purposes. Ensure that the water is clean and free from contaminants.
3. Machine Placement
Carefully position the blister packing machine in the prepared site. Use a level to ensure that the machine is perfectly horizontal, as an uneven surface can cause operational issues. Secure the machine to the floor if necessary, following the manufacturer’s instructions.
4. Initial Setup
Once the machine is in place, follow these steps for the initial setup:
– Check Connections: Verify that all utility connections (electricity, compressed air, and water) are properly attached and secure.
– Lubricate Moving Parts: Apply the recommended lubricant to all moving parts to ensure smooth operation.
– Install Tooling: Install the necessary tooling for the specific product you will be packaging. This includes the forming, sealing, and cutting tools.
– Load Materials: Load the plastic film and lidding material into their respective holders.
5. Calibration and Testing
After setting up the machine, it’s crucial to calibrate and test it to ensure that it’s functioning correctly:
– Calibrate Sensors: Adjust the machine’s sensors to accurately detect and process the materials and products.
– Test Run: Conduct a test run with a small batch of products to ensure that the machine is operating correctly. Check for any issues with forming, filling, sealing, or cutting.
– Adjust Settings: Make any necessary adjustments to the machine’s settings based on the test run results. This may include adjusting the temperature, pressure, and speed.
Maintenance of Blister Packing Machine
1. Routine 점검
Regular inspections are essential to identify and address potential issues before they become major problems. Establish a routine inspection schedule, and include the following tasks:
– Check for Wear and Tear: Inspect all moving parts for signs of wear and tear. Replace any worn parts to prevent malfunctions.
– Inspect Seals and Gaskets: Ensure that seals and gaskets are intact and not leaking. Replace them if necessary.
– Monitor Sensors and Electrical Components: Verify that all sensors and electrical components are functioning correctly. Check for loose connections or damaged wires.
2. Cleaning
Keeping the blister packing machine clean is vital for maintaining its performance and preventing contamination. Follow these cleaning practices:
– Daily Cleaning: Wipe down the exterior of the machine with a damp cloth to remove dust and debris.
– Weekly Cleaning: Thoroughly clean the forming, feeding, sealing, and cutting stations. Use appropriate cleaning agents and follow the manufacturer’s guidelines.
– Deep Cleaning: Periodically perform a deep cleaning of the entire machine, disassembling parts as necessary. Ensure that all components are thoroughly cleaned and dried before reassembly.
3. 매끄럽게 하기
Proper lubrication of moving parts is essential to prevent friction and wear. Follow these lubrication practices:
– Daily Lubrication: Apply lubricant to high-usage parts daily, following the manufacturer’s recommendations.
– Periodic Lubrication: Lubricate other moving parts on a weekly or monthly basis, depending on the machine’s usage and the manufacturer’s guidelines.
4. Preventive 유지
Implement a preventive maintenance schedule to keep the blister packing machine in optimal condition. This should include:
– Regularly Replacing Consumables: Replace consumable parts, such as belts and filters, at regular intervals to prevent unexpected breakdowns.
– Scheduled Servicing: Arrange for professional servicing of the machine at regular intervals. This ensures that any hidden issues are identified and addressed by experienced technicians.
5. Troubleshooting
Despite regular maintenance, issues can still arise. Knowing how to troubleshoot common problems can help minimize downtime:
– Jamming: If the machine jams, stop it immediately and identify the cause. This could be due to misaligned materials, incorrect settings, or worn parts.
– Inconsistent Sealing: Inconsistent sealing can be caused by incorrect temperature settings, worn sealing tools, or contamination. Adjust the temperature, replace worn tools, and ensure that the materials are clean.
– Product Misfeed: Misfeeding can result from incorrect settings, sensor issues, or worn feeding mechanisms. Check the settings, calibrate sensors, and replace any worn parts.
결론
Proper installation and maintenance of a 블리스터 포장기 are crucial for ensuring efficient and reliable operation. By following the guidelines outlined in this comprehensive guide, you can maximize the performance and longevity of your machine. Remember to consult the manufacturer’s manual for specific instructions and recommendations tailored to your model.
By taking a proactive approach to installation and maintenance, you can minimize downtime, reduce repair costs, and ensure that your blister packing machine continues to meet your production needs. Keep your machine running smoothly and efficiently, and you’ll reap the benefits of reliable and high-quality packaging for years to come.