As a pharmaceutical manufacturer or a decision-maker in the packaging process, you know that choosing the right packaging solution for your product is critical. You want to ensure that the packaging is not only functional but also enhances the integrity, safety, and appeal of your product. Cold formed blister pack are a popular choice in the pharmaceutical industry, offering unique benefits for certain types of products. But are they the right option for you? Let’s take a closer look at cold-formed blister packaging, its benefits, potential drawbacks, and whether it aligns with your needs.
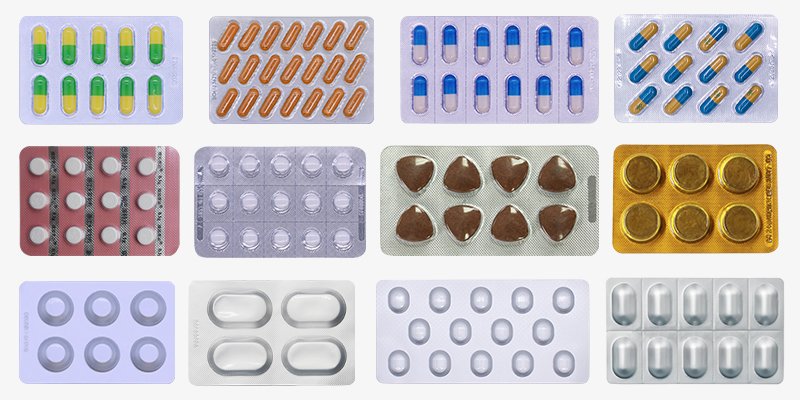
What Is Cold Formed Blister Packaging?
Cold-formed blister packaging is a method where the blister cavity is created by applying pressure to a metal foil (often aluminum) and PVC film without using heat. This process is different from traditional blister packaging, which involves heating plastic to form cavities.
Aluminum foil: The primary material used in cold-forming, providing a strong barrier to protect products from moisture, light, and oxygen.
PVC film: Provides a flexible but durable casing for the product inside.
Cold-formed blister packaging is commonly used in industries where product stability is essential, such as the pharmaceutical, nutraceutical, and healthcare sectors. The ability to block out environmental factors makes it an excellent choice for moisture-sensitive or light-sensitive products.
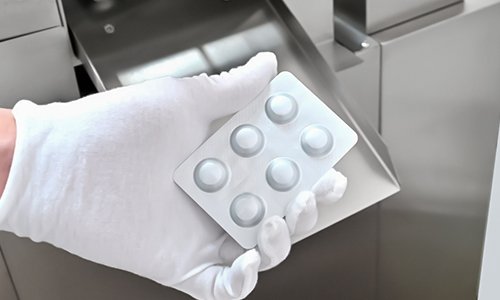
Key Benefits of Cold Formed Blister Packs
If you’re considering cold-formed blister packaging, you’re likely wondering about the advantages it offers. Let’s explore some key reasons why this type of packaging could be the best choice for your product.
Característica | Cold Formed Blister Packs | Traditional Blister Packs |
Protection Against Moisture | Alto: Aluminum provides an excellent moisture barrier. | Moderado: PVC or PET films are less effective. |
Light and Oxygen Barrier | Excelente: The foil provides complete protection from light and oxygen. | Limitado: Often only a partial barrier depending on materials used. |
Tamper-Evident | Superior: Strong seal ensures tamper-evidence. | Moderado: Tamper-evident seals are less secure. |
Duración | Longer: Preserves the product’s potency for longer periods. | Shorter: The product may degrade more quickly. |
Visual Appeal | De primera calidad: The clear, shiny foil gives a sleek, high-end look. | Básico: Less visually appealing. |
1. Superior Protection for Sensitive Products
Cold-formed blister packs are ideal for packaging moisture-sensitive, light-sensitive, o oxygen-sensitive products. The aluminum foil offers a robust shield against moisture, light, and air, ensuring the contents remain protected and potent throughout the product’s shelf life. If you’re packaging pharmaceutical drugs, vitamins, o medical devices that are prone to degradation, cold-formed blisters are a reliable solution.
2. Tamper-Evident and Secure
One of the most compelling reasons to use cold-formed blister packs is the tamper-evident feature. The strong seal that results from cold-forming provides a more secure barrier than traditional blister packs, making it easier for consumers to notice if a product has been tampered with. This is crucial for meeting regulatory standards and ensuring consumer safety, particularly when dealing with sensitive pharmaceuticals.
3. Vida útil prolongada
If your product requires long-term storage or distribution, cold-formed blister packs are an excellent choice. The airtight seal prevents environmental factors from affecting the product, keeping it fresh y effective for longer. Cold-forming provides better shelf life compared to traditional blister packs, which might not offer the same level of protection.
4. Premium Presentation and Branding
For products that need to project an image of high quality, cold-formed blister packs can elevate your brand’s perception. The smooth, glossy finish of the aluminum foil offers an attractive, premium look that can help set your product apart in a crowded marketplace. If you’re targeting high-end consumers, cold-formed blister packaging can enhance the appeal of your product, making it more desirable.
Potential Drawbacks of Cold Formed Blister Packaging
While cold-formed blister packs offer significant benefits, they may not be the best solution for every product. Here are a few considerations that could impact your decision.
Consideration | Cold Formed Blister Packs | Traditional Blister Packs |
Production Cost | Higher: The materials and machinery are more expensive. | Lower: Generally less costly to produce. |
Velocidad de producción | Slower: Cold-forming requires specialized equipment. | Faster: Easier and quicker to produce. |
Best for Product Types | Moisture and light-sensitive products. | Less sensitive products. |
Impacto ambiental | Moderado: More energy-intensive and resource-demanding. | Lower: Easier to recycle and less wasteful. |
1. Higher Production Costs
Cold-formed blister packs are more expensive to produce compared to traditional blister packs. The machinery required for the cold-forming process can be costly and requires specialized knowledge and expertise. Additionally, the materials used, such as aluminum foil, tend to be more expensive than the plastics used in conventional blister packaging. If your product doesn’t require high protection or if you’re operating on a tight budget, cold-formed blister packaging might not be the most cost-effective option.
2. Slower Production Rates
Cold-forming processes are typically slower than traditional blister packaging due to the precision required in forming the cavities from aluminum. If you’re operating in an environment where speed is critical, cold-formed blister packs may cause production bottlenecks. For smaller production runs or quick-turnaround needs, traditional blister packaging could be a better fit.
3. Limited to Certain Product Types
Cold-formed blister packs are specifically designed for sensitive products. If your product does not require protection from moisture, light, or air, you may not benefit from the added cost of cold-forming. If your product is relatively stable and doesn’t need such a robust barrier, a simpler packaging option might be more suitable.
When Cold Formed Blister Packs Might Not Be the Best Option for You
While cold-formed blister packs are ideal for sensitive, high-value products, they may not be the best choice in every situation.
For Less Sensitive Products
If you’re packaging non-sensitive products, like vitamins or tablets that are stable and not prone to environmental degradation, the cost and complexity of cold-formed blister packaging may not be necessary. In such cases, traditional blister packs made from PVC or PET could provide sufficient protection without the higher cost.
Budget Constraints
For manufacturers operating under budget constraints, the higher costs associated with cold-forming may be a limiting factor. Traditional blister packs are a more affordable alternative for products where extended shelf life and maximum protection are not as critical.
Smaller Production Runs
If your product is in a small production run or you’re just testing a new product, cold-forming may not be the best investment. The specialized machinery and materials may require a higher upfront investment that could be difficult to justify for smaller batches.
Conclusion: Is Cold Formed Blister Packaging Right for You?
Cold-formed blister packaging offers significant advantages for products that require superior protection, long shelf life, y premium presentation. If you’re packaging moisture-sensitive, light-sensitive, o high-value products, then cold-formed blister packs might be the best choice for you. However, the higher cost, slower production rates, y specialized machinery required may not make it suitable for all situations.
Ultimately, the decision will depend on your product’s needs, your production capacity, and your budget. By weighing the pros and cons, you’ll be able to make an informed choice about whether cold-formed blister packaging aligns with your business goals.