- Hogar
- Máquina empacadora de blísters
Máquina empacadora de blísters
Blister card packing machine, often called cardboard packaging machine or blister card machines, automate the process of securely sealing products to pre-printed paperboard cards, typically combined with clear alu pvc blister, alu alu blister, or formed plastic trays. The main function is to protect the blister plate from being damaged. Key applications span diverse industries: pharmaceuticals (tablets, capsules), consumer goods (toys, electronics accessories, batteries), hardware & tools (fasteners, small hand tools), health & beauty (razors, cosmetics, oral care) and automotive parts. These machines efficiently handle product loading, card folding, blister sealing (heat or ultrasonic), and final closure. They are essential for creating tamper-evident, shelf-appealing packaging that enhances brand presence, provides product information, and protects items during shipping and handling. Ideal for medium to high-volume production of durable and display-oriented packages.
Solicitud:
Paper card packing machine can pack tablet blisters, capsule blisters and other items.

Principio de funcionamiento
Paperboard Packaging Machine uses an automated process to place the blister sheet containing the tablets between two cardboards and then seals them, mainly to protect the blister sheet from being damaged.
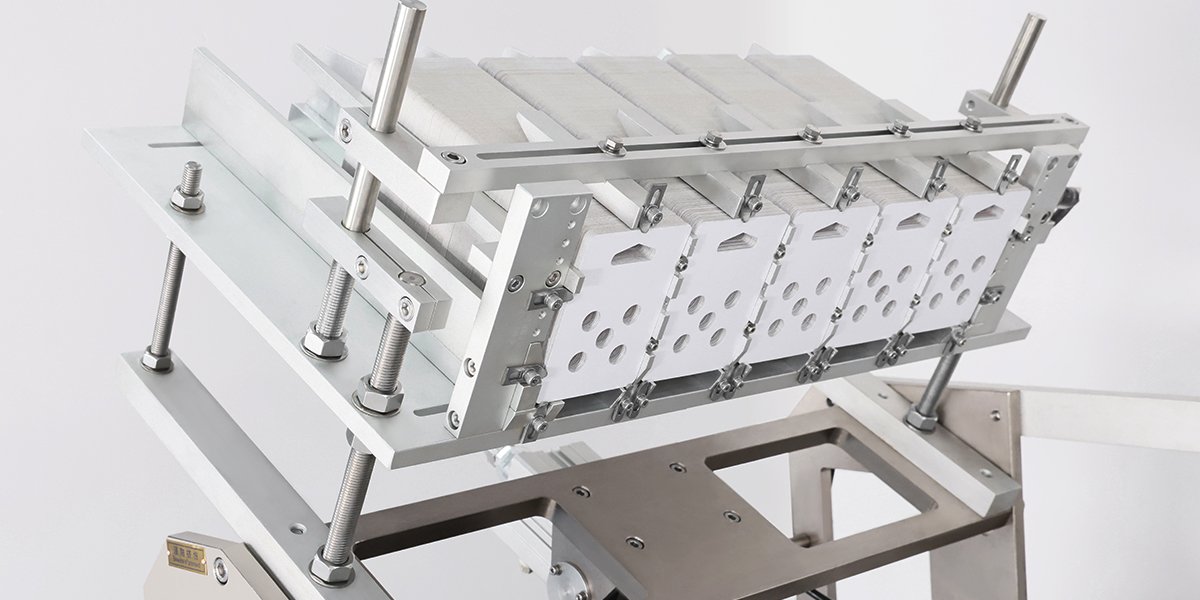
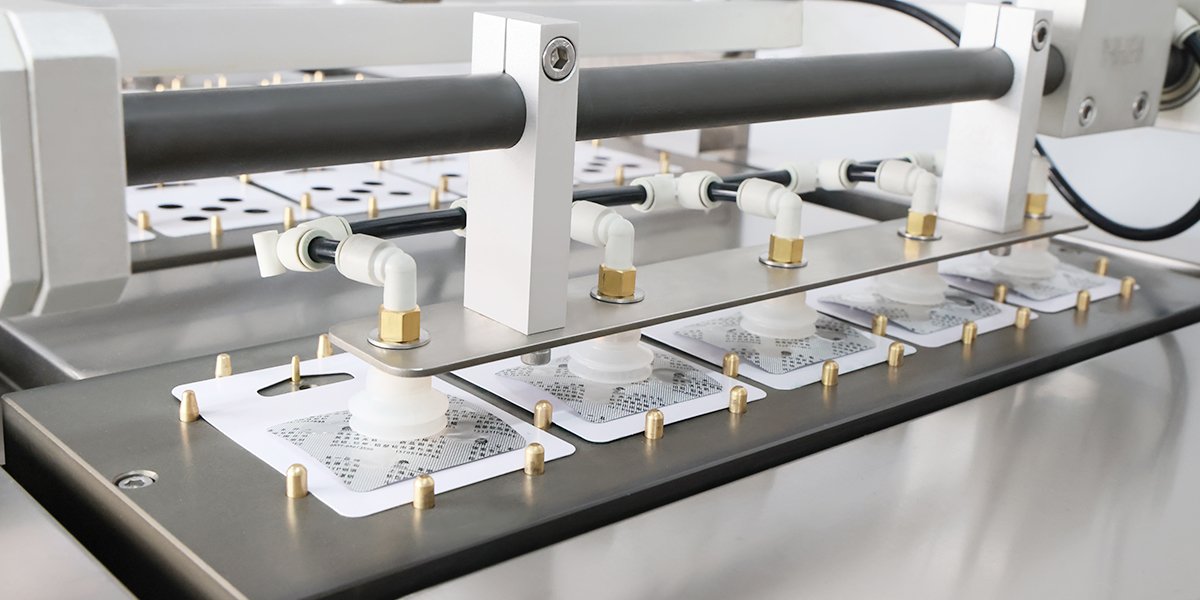
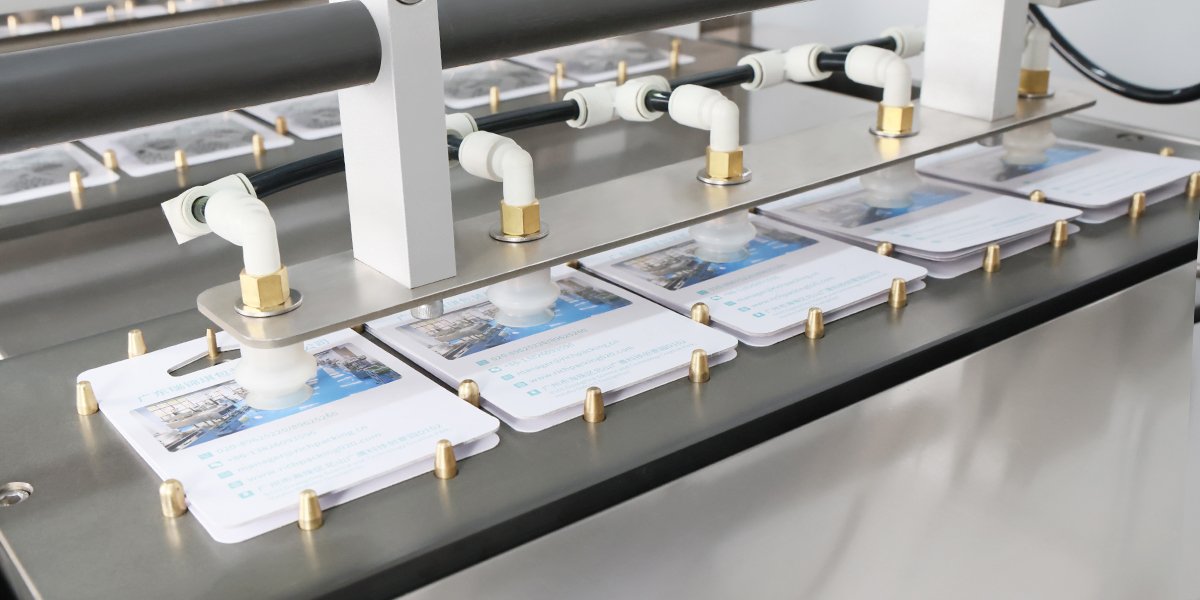
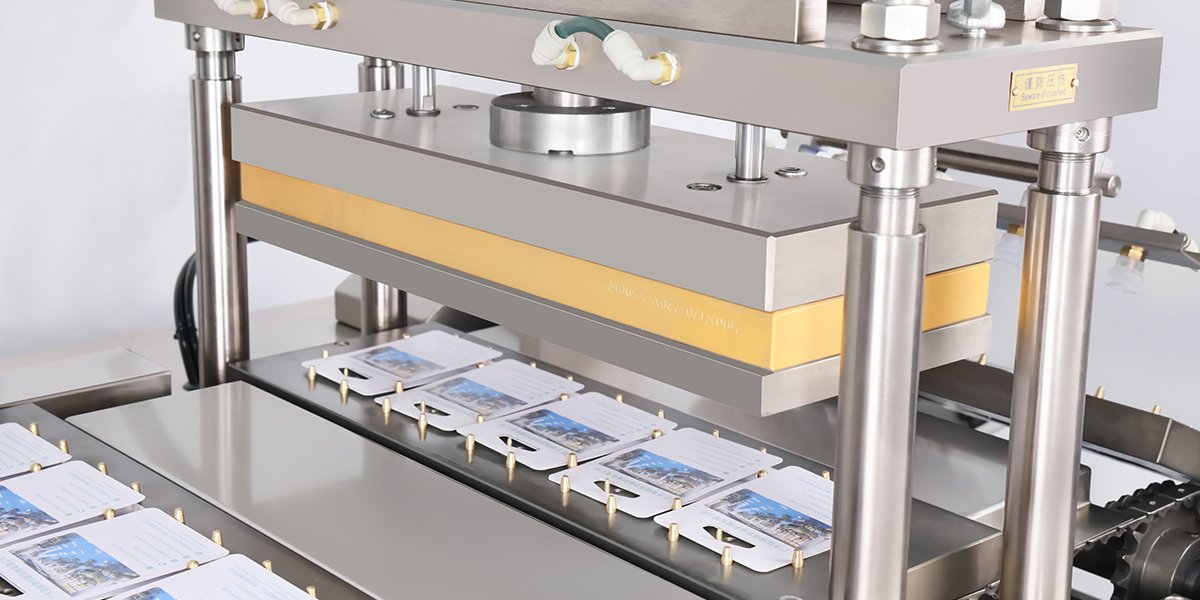
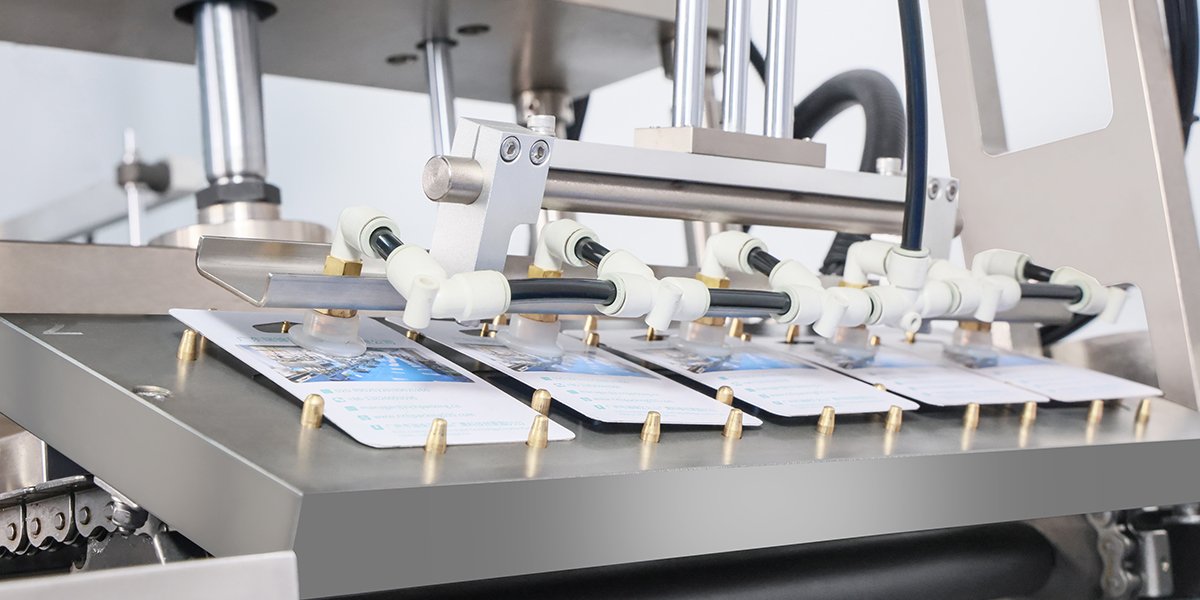
Parámetros técnicos
Elija la mejor máquina según el tamaño de las bolsas.
Machine Mold | RD-BCP-350Pro | RD-BCP-500Pro | RD-BCP-650Pro |
Capacidad de producción | 3,600 Plates/h | 5,400 Plates/h | 6,400 Plates/h |
Max. Forming Area | 330*210*65mm | 470*220*65mm | 630*220*65mm |
Paper Card Size | 350*220*0.5mm | 500*300*.05mm | 650*300*0.5mm |
Potencia total | 11.8 kW | 12.8 kW | 15.8 kW |
Productos de apoyo
Máquina automática de llenado de cápsulas NJP-3800D
La máquina llenadora automática de cápsulas NJP-3800D funciona alimentando automáticamente las cápsulas vacías, llenándolas con polvo, cerrándolas y preempacándolas.
Blister Packing Machine Manufacturer
Blister packing machine manufacturer offer various type machines that boosts output while lowering labor costs and material waste.
Tablet Compression Machine
Tablet compression machine is essential equipment for producing solid tablets by compacting powdered or granular materials.
Proveedor de calidad de Fortune 500
Features Advantage
Ruidapacking se compromete a fabricar máquinas con una calidad superior para cumplir con los estándares GMP con características eficientes y útiles.
Full Servo Control
The stroke can be accurate to 0.1mm, which is convenient for the alignment of paper cards and aluminum-plastic panels. The adjustment of the pulling distance of the product can be completed with one click on the touch screen.
Stronger Pressure Resistance
The heat sealing station mold is treated with Teflon, with better surface smoothness and pressure exceeding 100 kN.
Hard Anodized Molds
The 28-piece mold is made of high-grade aluminum alloy, the draw-out slot design allows mold changes within 15 minutes.
Le respaldamos con un servicio integral
Le acompañamos durante todo el proceso, desde la elección de la máquina adecuada hasta su cuidado de por vida.
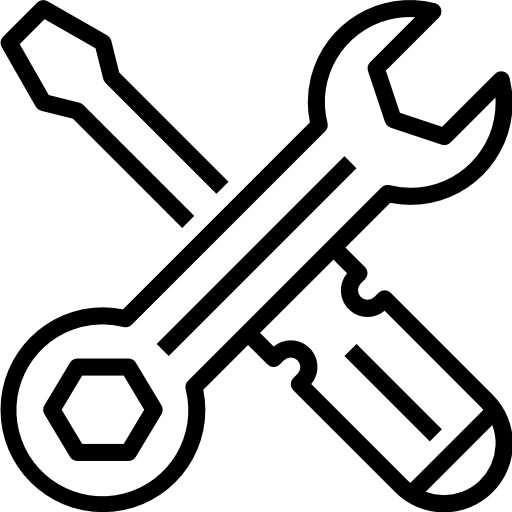
Garantía de por vida
Para garantizar un rendimiento óptimo durante mucho tiempo, ofrecemos reparaciones gratuitas durante 3 años y repuestos gratuitos durante 1 año. Posteriormente, le garantizamos asesoramiento técnico gratuito de por vida.
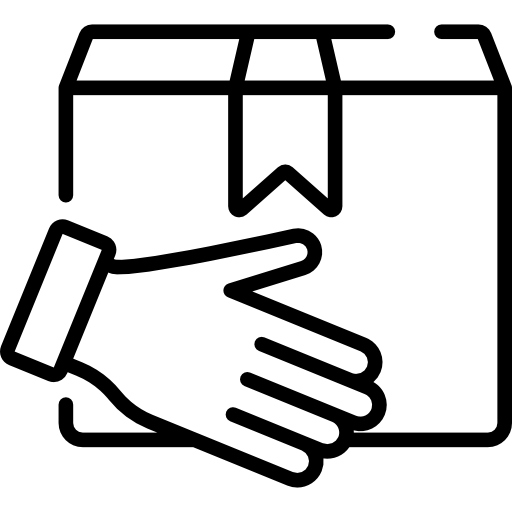
Entrega rápida en 7 días
Disponemos de 95% de nuestras máquinas estándar en stock. En este caso, el envío puede tardar 7 días. Para productos personalizados, el plazo de entrega es de tan solo 20 días.
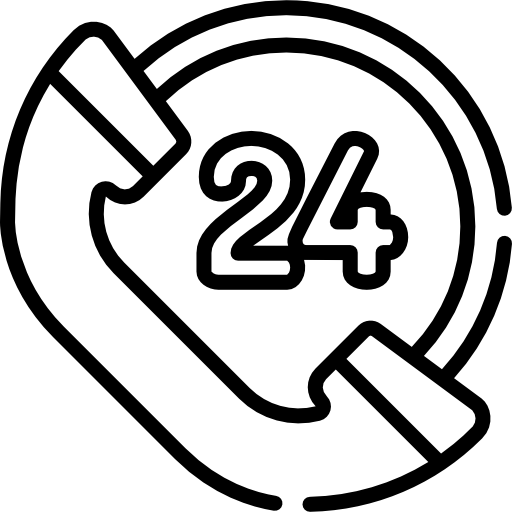
Servicio en línea
Nuestros expertos e ingenieros expertos en atención al cliente se centrarán en sus necesidades y resolverán todos sus problemas en un plazo de 24 horas, lo que incluye, entre otros, responder preguntas y realizar video remoto.
Preguntas frecuentes
Finding a truly reliable pharmaceutical blister card packaging machine can be a major headache for manufacturers. Common frustrations like poor sealing, product misalignment, and electrical safety concerns lead to wasted materials, rejected batches, operational downtime, and compliance risks. At Ruidapacking, we engineer our blister card machines to eliminate these exact problems, ensuring consistent quality, maximum efficiency, and uncompromised safety. Discover how our precision design solves the industry’s top three paper card packaging challenges.
1. Weak Sealing & High Reject Rates
The Industry Pain Point: Many blister card machines struggle with inconsistent or weak heat sealing. This results in blister packs detaching from the paperboard, compromised product integrity, and unacceptably high reject rates – directly hitting your bottom line through wasted materials and lost production time.
The Ruidapacking Solution: Our machines feature a heavy-duty heat sealing station engineered for perfection:
Massive, Controlled Pressure: We apply over 100 kN (10+ tons) of precisely calibrated pressure across the sealing area.
Premium Teflon-Coated Tooling: Sealing surfaces feature advanced Teflon (PTFE) coating, ensuring exceptional smoothness, consistent heat distribution, and preventing material sticking.
Result: Bonds are exceptionally strong and uniform every time. Dramatically reduced reject rates protect your profitability and ensure batch consistency.
2. Misaligned Cards & Poor Aesthetics
The Industry Pain Point: Achieving perfect alignment between the top and bottom paperboards is critical. Misaligned cards look unprofessional, can hinder functionality (e.g., hang holes blocked), and lead to consumer complaints or retailer rejections. Manual adjustments are time-consuming and often ineffective.
The Ruidapacking Solution: Precision alignment is built into our core design:
Dowel Pin Positioning System: We utilize a robust dowel pin location system within the tooling.
Guaranteed Registration: This system securely fixes each paperboard in its exact correct position on the mold before the heat sealing station begins.
Result: Perfect, consistent overlap of top and bottom cards every single cycle. Your finished packs look professional, function flawlessly, and meet the highest aesthetic standards.
3. Electrical Safety Hazards
The Industry Pain Point: Concerns about electrical safety, including potential leakage currents or unreliable components, are serious. These hazards endanger operators, violate strict cGMP and workplace safety regulations (like CE, UL), and create significant liability risks. Downtime for electrical repairs is costly.
The Ruidapacking Solution: Safety and reliability are non-negotiable:
World-Class Electrical Components: We exclusively integrate premium, globally recognized electrical brands (e.g., Siemens, Schneider Electric) known for their reliability and stringent safety certifications.
Robust Wiring & Grounding: Our machines are built with high-grade wiring harnesses and meticulous grounding practices exceeding international safety standards.
Result: Operators work with confidence. You achieve full compliance with cGMP and essential safety directives (CE marked), eliminate electrical hazard risks, and benefit from drastically reduced electrical failure downtime.
Conclusión
Stop battling unreliable blister card machines that compromise your quality, efficiency, and safety. Ruidapacking’s pharmaceutical paper card packaging machines are engineered from the ground up to solve the most persistent problems plaguing the industry. Our commitment to robust construction (100kN+ sealing), precision alignment (dowel pin system), and absolute electrical safety (premium components) delivers:
Higher Profitability: Slash reject rates and minimize costly downtime.
Flawless Quality: Guarantee perfectly aligned, professionally sealed packs.
Uncompromised Safety & Compliance: Meet cGMP and stringent electrical safety standards with confidence.
En las líneas de envasado de bolsas prefabricadas, la decisión fundamental de seleccionar una pesadora multicabezal o una máquina contadora de tabletas, cápsulas y gomitas como equipo auxiliar depende de las características del material que se manipula. Estas dos tecnologías ofrecen ventajas distintivas y son adecuadas para aplicaciones específicas. Seleccionar la máquina incorrecta puede reducir la eficiencia, reducir la precisión, generar un alto desperdicio de material o incluso provocar fallos operativos.
A continuación se analizan en detalle los criterios de selección, las fortalezas y las limitaciones de cada dispositivo, en función de las características clave del material:
1. Propiedades del material
Forma física
Gránulos, copos, barras, trozos (sólidos regulares/irregulares): Tanto la pesadora multicabezal como la máquina llenadora contadora son opciones posibles; la selección final depende de otras propiedades.
Partícula fina: generalmente más adecuada para máquinas contadoras.
Polvos, pastas, líquidos y materiales viscosos: Ni las dosificadoras de pesaje multicabezal ni las máquinas contadoras automáticas son adecuadas. Estas requieren equipos de llenado volumétrico (dosificadoras de sinfín, dosificadoras de pistón, dosificadoras de líquidos) o básculas de peso neto.
Peso/tamaño individual
Peso individual grande y relativamente uniforme: (galletas grandes, barras de chocolate, frutas enteras, piezas de juguetes) Las pesadoras combinadas de múltiples cabezales generalmente ofrecen ventajas en eficiencia y rentabilidad.
Peso individual muy pequeño o muy variable: (pastillas pequeñas, semillas, ositos de goma, artículos pequeños). Las máquinas contadoras electrónicas automáticas destacan por su precisión y minimizan el desperdicio. Las básculas multicabezal tienen dificultades para controlar la precisión de artículos muy ligeros, y los artículos pequeños son propensos a perderse por aireación dentro de las cubetas de pesaje durante el funcionamiento.
2. Pesadoras multicabezal
El material se distribuye desde un alimentador vibratorio principal a múltiples tolvas de pesaje independientes (normalmente de 8 a 24). Un sistema informático lee continuamente el peso de cada tolva y utiliza un algoritmo de pesaje combinado para identificar rápidamente el grupo de tolvas cuyo peso combinado se aproxima más al peso objetivo. Las tolvas seleccionadas se descargan simultáneamente en un embudo de recolección inferior, dirigiendo el material a la bolsa de envasado.
Ventajas
Alta velocidad: El principio de pesaje combinado permite velocidades de pesaje excepcionalmente altas (normalmente 100-200 bolsas/minuto, con modelos de alta velocidad que superan las 300 bolsas/minuto), lo que lo convierte en la opción preferida para maximizar la producción.
Alta precisión: Para materiales de flujo libre con pesos individuales moderados, las básculas multicabezal alcanzan una precisión de pesaje muy alta (de ±0,1 g a ±1 g o superior, según el material y el peso objetivo). El algoritmo de combinación compensa eficazmente las variaciones individuales de alimentación.
Amplio rango de peso: Capaz de manejar especificaciones de embalaje que van desde unos pocos gramos a varios kilogramos ajustando el peso objetivo y el tamaño del cucharón, ofreciendo una gran adaptabilidad.
Ideal para materiales de flujo libre: procesa gránulos, copos, trozos y otros materiales de flujo libre de manera suave y eficiente.
Limpieza y mantenimiento relativamente fáciles: presenta una estructura relativamente estandarizada; las partes en contacto con el material (alimentador vibratorio, cubos) generalmente son desmontables para su limpieza.
Desventajas
Problemas con materiales que fluyen mal: Los materiales propensos a pegarse, aglutinarse, ser aceitosos o húmedos pueden obstruirse fácilmente en el alimentador vibratorio, las tolvas de almacenamiento o los cubos de pesaje, lo que genera una alimentación desigual, una precisión reducida o incluso la detención de la máquina.
Desafíos con materiales pequeños o muy ligeros: Los objetos extremadamente pequeños o ligeros (como semillas diminutas o pastillas pequeñas) son susceptibles a la dispersión del aire («desplazamiento») dentro de las cubetas de pesaje, lo que provoca pérdida de material. Las ventajas de precisión también disminuyen con pesos objetivo muy pequeños.
Daños potenciales a artículos frágiles: La acción de giro en el alimentador vibratorio y la descarga del balde pueden causar impacto y fricción, dañando potencialmente productos muy frágiles (papas fritas).
Dificultad con materiales irregulares o enredados: Los elementos largos, planos o fibrosos pueden enredarse o atascarse en las pistas del alimentador vibratorio o en las entradas del cangilón.
Indica peso, no recuento: Indica un peso objetivo, no un recuento exacto de piezas. No es adecuado para aplicaciones que requieren cantidades precisas (artículos vendidos por recuento unitario).
3. Eléctrico Máquinas contadoras
Las máquinas de conteo de botellas aíslan los artículos individuales mediante separación física o tecnología de reconocimiento visual y los cuentan. Los tipos más comunes incluyen:
Máquina contadora y llenadora: los artículos se ponen en cola sobre pistas vibratorias y se cuentan mediante sensores fotoeléctricos.
Máquina contadora de inspección con cámara CCD: las cámaras de alta velocidad capturan imágenes de los artículos que caen y el software de procesamiento de imágenes identifica y cuenta las unidades individuales.
Ventajas
Proporciona un recuento exacto de piezas: la única solución para aplicaciones que requieren recuentos precisos (productos farmacéuticos, gomitas, caramelos, componentes electrónicos).
Manejo superior de materiales que fluyen mal: generalmente supera a las pesadoras de múltiples cabezales en el procesamiento de materiales húmedos, aceitosos o pegajosos con un riesgo de obstrucción reducido.
Excelente para contar pastillas pequeñas: ideal para contar con alta precisión y bajo desperdicio pastillas pequeñas, semillas y dulces.
Maneja formas irregulares de manera eficaz: los contadores de visión avanzados pueden identificar y contar con precisión artículos con geometrías diversas y desafiantes.
Baja pérdida de material: el conteo generalmente evita la inversión del balde de pesaje, lo que minimiza las pérdidas por “material suelto” o residuos de producto.
Bajo nivel de ruido: menos componentes vibratorios en comparación con las pesadoras de múltiples cabezales generalmente dan como resultado niveles de ruido más bajos.
Desventajas
Velocidad más baja: La velocidad absoluta suele ser inferior a la de las pesadoras multicabezal (especialmente para artículos pequeños). Las contadoras de visión de alta velocidad pueden alcanzar entre 100 y 150 unidades, pero esto se traduce en velocidades de envasado más bajas (entre 60 y 90 bolsas/minuto para paquetes de 100 unidades) en comparación con las pesadoras de alta velocidad.
La precisión del peso depende de la uniformidad de la unidad: La precisión de conteo es de 100%, pero la precisión del peso del paquete depende completamente de la consistencia del peso individual del artículo. Una variación significativa del peso (frutas secas de tamaño irregular, nueces) provoca grandes fluctuaciones en el peso del paquete.
Sensibilidad a la aglomeración de artículos: Si dos o más artículos se pegan y se cuentan como uno solo, se produce un subconteo. (Ejemplo de solución: Nuestro contador de dulces especializado combate la aglomeración mediante cuatro características clave).
Agitador de tolva con púas: evita que las gomitas se apilen verticalmente.
Rodillo de distribución antiaglomerantes: garantiza una dispersión uniforme del lote evitando la adherencia.
Paneles con hoyuelos de teflón: separan completamente las gomitas y permiten un deslizamiento suave y rápido.
Puerto de descarga de PTFE agrandado: reduce las obstrucciones y aumenta la velocidad en 58%.
Selección de equipos complejos: los diferentes tipos de contadores varían significativamente en cuanto a la idoneidad del material, lo que requiere conocimientos especializados y pruebas para una selección óptima.
Alto costo de los contadores de visión: la inversión inicial en sistemas de conteo de visión de alto rendimiento puede ser sustancial y a menudo exceder los costos de las pesadoras de múltiples cabezales.
Capacidad limitada para artículos grandes o pesados: contar trozos muy grandes (barras de chocolate enteras, juguetes grandes) suele ser estructuralmente poco práctico, más lento y menos rentable que utilizar pesadoras de múltiples cabezales.
4. Resumen y guía de selección de equipos
Característica | Recomendar pesadora multicabezal | Recomendar máquina de conteo automático |
Requisito básico | El peso objetivo es la prioridad; busque la máxima velocidad y eficiencia. | El recuento preciso de piezas es esencial; de lo contrario, las propiedades del material hacen que el pesaje no sea adecuado |
Fluidez del material | Bueno(seco, fluido) | Pobre/Promedio (oleoso, húmedo, pegajoso, propenso a formar puentes) |
Forma material | Principalmente gránulos, copos y trozos. | Principalmente partículas finas, micropellets, formas irregulares, artículos planos y alargados. |
Peso individual | Partículas medianas a grandes o pequeñas pero uniformes | Artículos muy pequeños o con gran variación de peso que requieren conteo de piezas |
Precisión del embalaje | Alta precisión de peso (±0,1 g – ± 1 g) | Precisión de conteo 100% (La precisión del peso depende de la uniformidad de cada pieza) |
Velocidad | Muy alta (100-300+ bolsas/minuto) | Medio-alto (depende del tamaño del artículo y la tecnología de conteo; generalmente más bajo que las básculas) |
Aplicaciones | Snacks (papas fritas/frutos secos/dulces), alimentos congelados, comida para mascotas, granos de café, ferretería, gránulos químicos | Productos farmacéuticos (tabletas/cápsulas), suplementos, semillas, gomitas, componentes electrónicos, artículos de alto valor vendidos por conteo |
5. Recomendaciones de mejores prácticas para respaldar la selección de productos
Realice rigurosas pruebas de materiales: Envíe muestras reales de material a ruidapacking para su análisis. Compruebe de primera mano la capacidad de procesamiento, la precisión, la velocidad y la pérdida de material del equipo con su producto específico.
Planifique las necesidades de producción futuras: si en el futuro tiene que empaquetar materiales con diferentes propiedades, priorice los equipos que tengan compatibilidad o flexibilidad para manejar diversos productos.
Garantice una integración perfecta en la línea de producción: garantice que el equipo de dosificación elegido se integre sin problemas con los sistemas de alimentación ascendentes (elevadores, contenedores de almacenamiento) y la máquina de envasado descendente.
Rendimiento del partido: verificar la compatibilidad en velocidad e interfaces mecánicas/físicas para evitar cuellos de botella.
Priorizar el soporte y el servicio del proveedor: seleccione un proveedor con sólida experiencia técnica y un historial comprobado de servicio y soporte posventa receptivo y de alta calidad.
Al evaluar cuidadosamente las propiedades clave de su material y comprender completamente las fortalezas y limitaciones principales de las pesadoras de múltiples cabezales y las máquinas contadoras automáticas de botellas, puede seleccionar con confianza la solución de dosificación más adecuada, eficiente y rentable para su línea de envasado de bolsas prefabricadas.
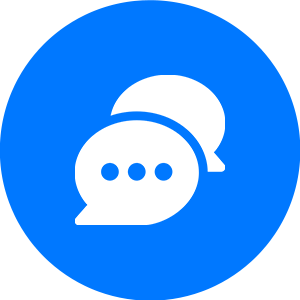