Capsules Packaging plays a crucial role in ensuring product safety, stability, and efficiency in the pharmaceutical industry. Whether you are looking for blister packaging, capsule counting, bottling, or other packaging solutions, understanding each method is essential. This guide will help you make informed decisions tailored to your production needs.
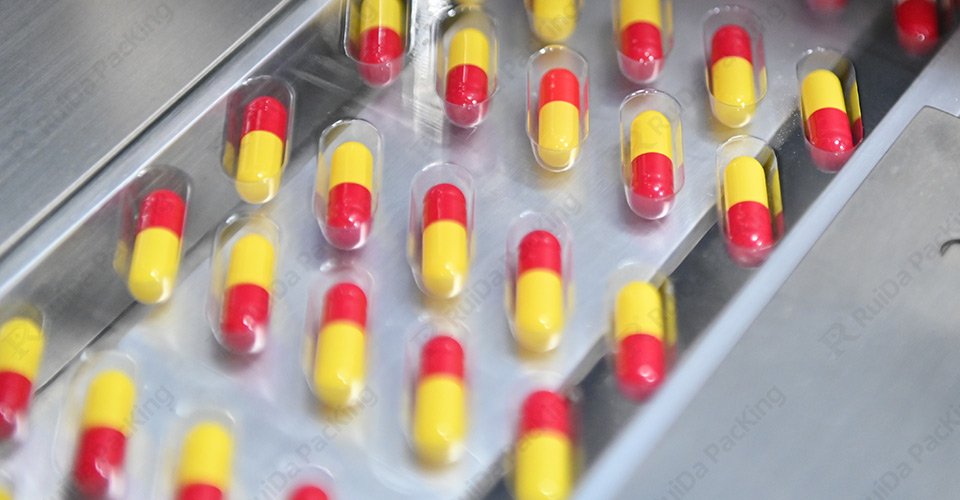
Importance of Capsules Packaging
Packaging is more than just an aesthetic or logistical choice; it directly impacts product integrity, consumer trust, and regulatory compliance. Proper capsules packaging prevents contamination, ensures accurate dosage, and extends shelf life. Additionally, choosing the right packaging method enhances production efficiency and cost-effectiveness.
Common Capsules Packaging Methods
1. Blister Packaging for Capsules
Blister packaging is one of the most widely used methods for packaging capsules. This method involves sealing capsules in pre-formed cavities (blisters) made from plastic, often PVC, or other materials such as aluminum foil. The capsule is placed in the cavity, and a sealing film is applied to form a protective barrier.
Blister packs offer several benefits, including superior protection from moisture, light, and air, which helps maintain the capsule’s potency. They also allow for individual dosage convenience, reducing the risk of contamination. This type of packaging is commonly used for pharmaceutical products, as it is tamper-evident and offers a clear view of the capsule inside. Blister packaging is available in different configurations, such as thermoformed blisters, cold-formed blisters, and pre-formed blisters, depending on the material and process.
Φόντα:
- Moisture and air protection
- Tamper-proof
- Clear visibility of contents
- Compact and convenient for consumers
- Cost-effective for mass production
Disadvantages:
- May be more costly than simple bottles for small batches
- Less suitable for products that require high humidity protection
When implementing blister packaging, you need to consider several crucial factors:
- Επιλογή Υλικού
- PVC (Polyvinyl Chloride): Standard option with basic moisture barrier
- PVDC (Polyvinylidene Chloride): Enhanced moisture protection
- COC (Cyclic Olefin Copolymer): Superior barrier properties
- Aluminum: Maximum protection against moisture and light
- Forming Process
- Cold forming (aluminum-based)
- Thermoforming (plastic-based)
- Deep-draw capabilities for larger capsules
Blister Packaging Machines
Blister packaging machines automate the process, improving efficiency and accuracy. These machines can handle various capsule sizes and materials, ensuring a seamless production workflow.
2. Capsule Counting and Bottling
Bottle packaging is another popular method for capsule packaging. Capsules are placed in bottles made from materials like PET, HDPE, or glass. This method is typically used for large-volume packaging and is often combined with desiccant inserts or cotton padding to protect the contents from moisture.
Bottle packaging offers flexibility in terms of container size, allowing manufacturers to package varying quantities depending on the product’s intended use. It is commonly used for dietary supplements and over-the-counter medications. A major advantage of bottle packaging is that it allows for large batches to be handled at once, making it ideal for bulk production. However, it does not provide the same level of protection as blister packaging, especially in humid or light-exposed environments.
Φόντα:
- Cost-effective for larger quantities
- Easy to label and brand
- Wide range of bottle sizes
- Suitable for bulk orders
Disadvantages:
- Less protection against moisture and contamination
- Higher risk of tampering or contamination once opened
3. Sachet Packaging
Sachet packaging involves sealing individual capsules in small, often foil-based, packets. This method is typically used for single-dose packaging, offering the advantage of portability. Sachets are commonly used in markets that require a convenient, one-time-use product, such as in travel packs or sample products.
Sachet packaging is also beneficial for maintaining product freshness, as the capsules are sealed in an airtight, tamper-evident environment. It is particularly useful for capsules that need to be consumed quickly or as a promotional tool for trial-size products. However, sachets are not typically used for mass-market capsules due to cost considerations and the complexity of packaging automation.
Φόντα:
- Convenient, portable packaging
- Single-dose format
- Effective barrier against external elements
Disadvantages:
- More costly and complex compared to other methods
- Limited capacity, making it unsuitable for bulk packaging
4. Carded Συσκευασία
Carded packaging, which involves attaching capsules to a cardboard backing with a clear plastic blister, is often used for retail products. The capsules are secured to the card with a blister pack, and the card can be branded with essential product information. Carded packaging is often used for small quantities of capsules or trial-size packages.
This method is relatively inexpensive and provides a high degree of visibility for the product. It is commonly used in retail environments where shelf appeal is essential. However, it doesn’t provide the same level of protection as more robust packaging methods like bottle or blister packaging.
Φόντα:
- High product visibility
- Cost-effective for small volumes
- Great for retail environments
Disadvantages:
- Limited protection from external factors like moisture and light
- Less suitable for larger quantities of capsules
Factors to Consider When Choosing a Capsules Packaging Method
1. Product Protection Needs
Consider factors like moisture sensitivity, light exposure, and contamination risks when selecting a packaging method.
2. Κανονιστική Συμμόρφωση
Ensure that your packaging method meets industry regulations such as GMP (Good Manufacturing Practices) and FDA guidelines.
3. Production Scale and Efficiency
Different packaging methods cater to different production scales. Blister packaging suits small to mid-range production, while bottling is ideal for high-volume manufacturing.
4. Cost Considerations
Each packaging method comes with its own cost structure. Blister packaging requires specialized materials, while bottling systems need precision counting machines.
5. Consumer Convenience and Market Trends
User-friendly packaging, such as single-dose blister packs, enhances consumer appeal. Consider emerging market trends when choosing your packaging solution.
Frequently Asked Questions (FAQs)
1. Which packaging method is best for moisture-sensitive capsules?
Blister packaging with aluminum backing is the best choice for moisture-sensitive capsules.
2. Can I use capsule counting machines for different capsule sizes?
Yes, most modern capsule counting machines offer adjustable settings for different capsule sizes.
3. What is the most cost-effective capsule packaging method?
For large-scale production, capsule bottling is the most cost-effective solution.
4. How do I ensure my packaging complies with regulations?
Always choose a method that meets industry standards such as GMP and FDA requirements.
5. What are the advantages of automated packaging machines?
Automation increases efficiency, accuracy, and overall production speed while reducing human error.
Σύναψη
The methods of capsule packaging, whether blister packaging, bottle packaging, sachets, or carded packaging, all offer distinct advantages depending on your needs—whether that be for consumer convenience, product protection, or cost-effectiveness. Similarly, the process of capsule counting plays a critical role in ensuring accurate dosages and meeting compliance requirements, with automated systems being the most efficient choice for large-scale production.
For businesses looking to streamline their capsule packaging processes, understanding these methods and technologies is key to making the right investment decisions.