You’re working with a natural protein substance derived primarily from collagen. Pharmaceutical gelatin comes from specially processed collagen extracted from bovine or porcine sources. The material undergoes rigorous purification and standardization to meet strict pharmaceutical requirements.
The composition typically includes:
– Type A gelatin (acid-processed) or Type B gelatin (alkaline-processed)
– Purified water
– Preservatives (when necessary)
– Colorants (if required)
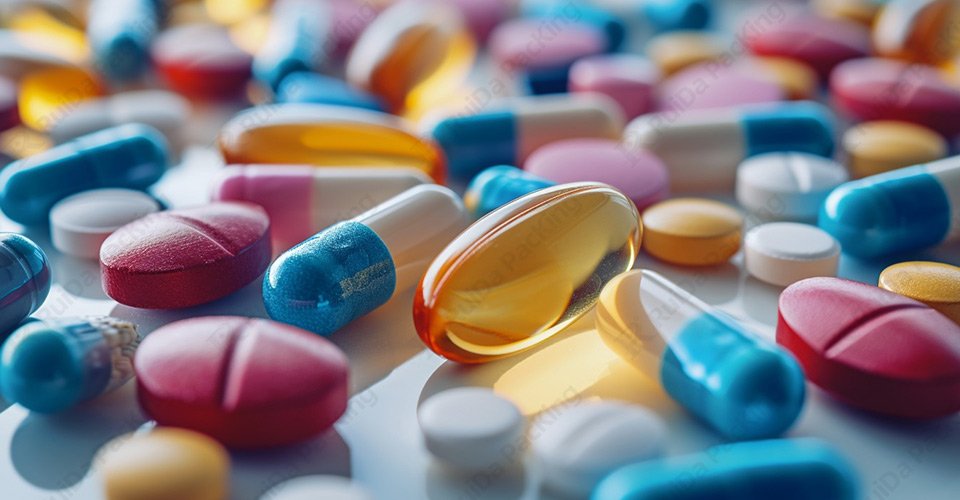
Types of Gelatin Capsules
You’ll encounter three main types of gelatin capsules in pharmaceutical applications:
These two-piece capsules give you flexibility in filling operations and are ideal for powders, granules, and small pellets. Available in sizes ranging from 000 (largest) to 5 (smallest), they offer you various capacity options.
- Weichgelatinekapseln
When you’re working with liquids, oils, or suspensions, these one-piece sealed capsules provide excellent containment and stability. They can be manufactured in various shapes and sizes to meet your specific needs.
- Modified Release Capsules
These specialized capsules allow you to control the release profile of your active ingredients through various mechanisms, including enteric coating or modified shell composition.
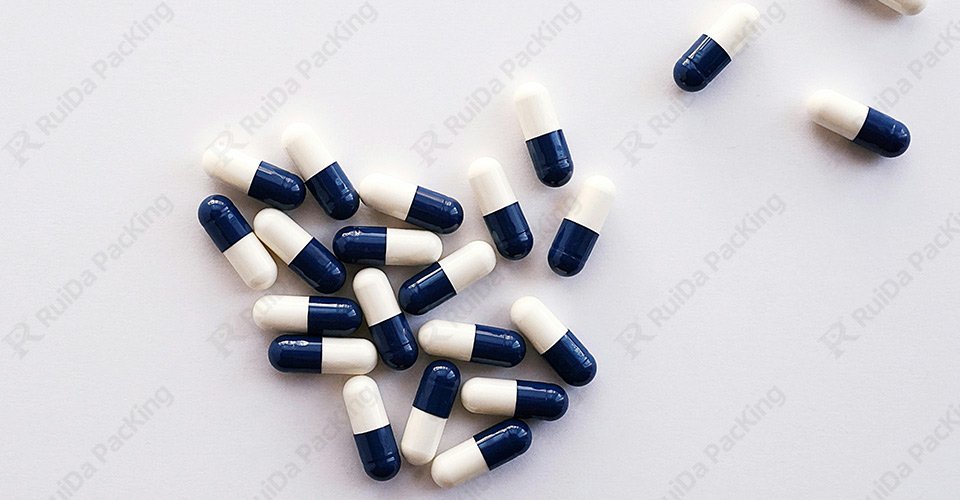
Herstellungsprozess
Raw Materials
Your success in capsule manufacturing starts with selecting the right materials:
Quality Requirements:
– Bloom strength: 150-280 grams
– Viscosity: 2.5-6.0 millipoise
– Moisture content: 9-16%
– Ash content: <2%
– Heavy metals: <10 ppm
Additional ingredients you might need include:
– Plasticizers (glycerin, sorbitol)
– Preservatives (sulfur dioxide, methyl paraben)
– Colorants (approved food dyes)
– Opacity modifiers (titanium dioxide)
Production Methods
Hard Capsule Production
Your manufacturing process typically involves:
- Gelatin Solution Preparation
– Precise temperature control (60-70°C)
– Careful mixing to avoid air incorporation
– Exact concentration control
- Dipping Process
– Temperature-controlled pin dipping
– Controlled dwell time
– Uniform film formation
- Drying and Cutting
– Controlled environmental conditions
– Precise cutting operations
– Size verification
Soft Capsule Production
The rotary die process includes:
- Gelatin ribbon formation
- Fill material encapsulation
- Sealing and shape forming
- Drying and conditioning
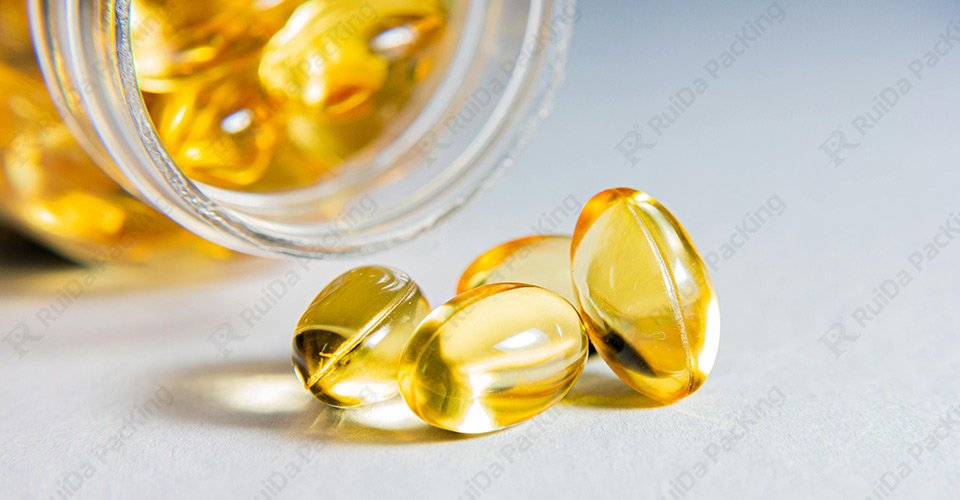
Key Properties and Characteristics
Physical Properties
You need to monitor these critical parameters:
- Shell Thickness
– Hard capsules: 0.095-0.115mm
– Soft capsules: 0.110-0.150mm
- Dissolution Properties
– Typical dissolution time: 15-30 minutes
– pH-dependent behavior
– Temperature sensitivity
- Mechanical Characteristics
– Tensile strength
– Elasticity
– Impact resistance
Chemical Properties
Understanding these properties helps you maintain product stability:
- pH Stability
– Optimal range: 2.5-7.5
– Buffer capacity
– Acid/base interaction potential
- Cross-linking Prevention
– Temperature control
– Humidity management
– Excipient compatibility
Applications and Uses
Pharmaceutical Applications
You can utilize gelatin capsules for:
- Prescription Medications
– Immediate release formulations
– Modified release systems
– Combination products
- Over-the-counter Products
– Vitamins and minerals
– Pain relievers
– Cold and flu medicines
Dietary Supplement Applications
Your supplement options include:
- Vitamin Formulations
– Single vitamins
– Multivitamin complexes
– Mineral combinations
- Specialty Products
– Herbal extracts
– Essential oils
– Enzyme preparations
Storage and Handling
Storage Requirements
Maintain these conditions for optimal stability:
Temperature:
– Ideal range: 15-25°C
– Maximum fluctuation: ±3°C
Humidity:
– Relative humidity: 35-65%
– Monitoring requirements
– Humidity control systems
Handling Guidelines
Follow these best practices:
- Environmental Control
– Clean room conditions
– Air filtration
– Temperature monitoring
- Personnel Requirements
– Proper training
– Protective equipment
– Documentation procedures
Qualitätskontrolle und Prüfung
Quality Parameters
Your testing program should include:
- Physical Tests
– Dimensional analysis
– Weight variation
– Disintegration time
– Dissolution profile
- Chemical Analysis
– Moisture content
– Heavy metals
– Residual solvents
– Content uniformity
Einhaltung gesetzlicher Vorschriften
Ensure compliance with:
- FDA Requirements
– GMP guidelines
– Documentation requirements
– Validation protocols
- International Standards
– Ph.Eur. specifications
– USP requirements
– JP standards
Advantages and Limitations
Vorteile
You gain these advantages:
- Enhanced Bioavailability
– Rapid dissolution
– Consistent absorption
– Improved efficacy
- Manufacturing Efficiency
– High production speeds
– Cost-effectiveness
– Process reliability
Limitations
Consider these challenges:
- Environmental Sensitivity
– Temperature effects
– Humidity impact
– Storage requirements
- Material Restrictions
– Vegetarian limitations
– Religious considerations
– Cost factors
Troubleshooting Common Issues
Herstellungsprobleme
Address these common problems:
- Shell Formation
– Thickness variations
– Brittleness
– Soft spots
- Sealing Problems
– Incomplete closure
– Leakage
– Deformation
Storage and Stability Issues
Monitor for:
- Physical Changes
– Brittleness
– Softening
– Discoloration
- Chemical Degradation
– Cross-linking
– Content deterioration
– Dissolution changes
Market Trends and Future Developments
Current Market Trends
Stay aware of:
- Verbraucherpräferenzen
– Natural ingredients
– Clean label demands
– Sustainability concerns
- Industry Developments
– Automation advances
– Quality improvements
– Cost optimization
Innovation and Development
Watch for these advances:
- New Technologies
– Smart capsule systems
– Novel coating methods
– Advanced manufacturing
- Sustainable Practices
– Bio-based materials
– Reduced energy consumption
– Waste minimization
Best Practices
Follow these guidelines for optimal results:
- Quality Maintenance
– Regular testing
– Environmental monitoring
– Documentation control
- Process Optimization
– Parameter control
– Efficiency improvement
– Cost management
Safety Considerations
Maintain:
- Material Safety
– Supplier qualification
– Testing protocols
– Contamination prevention
- Process Safety
– Equipment validation
– Personnel training
– Emergency procedures
Abschluss
Your success with gelatin capsules depends on understanding and controlling all aspects of their production and use. This comprehensive guide provides you with the essential knowledge needed to work effectively with these versatile drug delivery systems. Remember to stay updated with current regulations and maintain strict quality control for optimal results.
For more specific information or technical support, consider consulting with capsule manufacturers or pharmaceutical experts who can provide detailed guidance for your particular applications.