- Heim
- Blisterkarten-Verpackungsmaschine
Blisterkarten-Verpackungsmaschine
Blister card packing machine, often called cardboard packaging machine or blister card machines, automate the process of securely sealing products to pre-printed paperboard cards, typically combined with clear alu pvc blister, alu alu blister, or formed plastic trays. The main function is to protect the blister plate from being damaged. Key applications span diverse industries: pharmaceuticals (tablets, capsules), consumer goods (toys, electronics accessories, batteries), hardware & tools (fasteners, small hand tools), health & beauty (razors, cosmetics, oral care) and automotive parts. These machines efficiently handle product loading, card folding, blister sealing (heat or ultrasonic), and final closure. They are essential for creating tamper-evident, shelf-appealing packaging that enhances brand presence, provides product information, and protects items during shipping and handling. Ideal for medium to high-volume production of durable and display-oriented packages.
Anwendung:
Paper card packing machine can pack tablet blisters, capsule blisters and other items.

Funktionsprinzip
Paperboard Packaging Machine uses an automated process to place the blister sheet containing the tablets between two cardboards and then seals them, mainly to protect the blister sheet from being damaged.
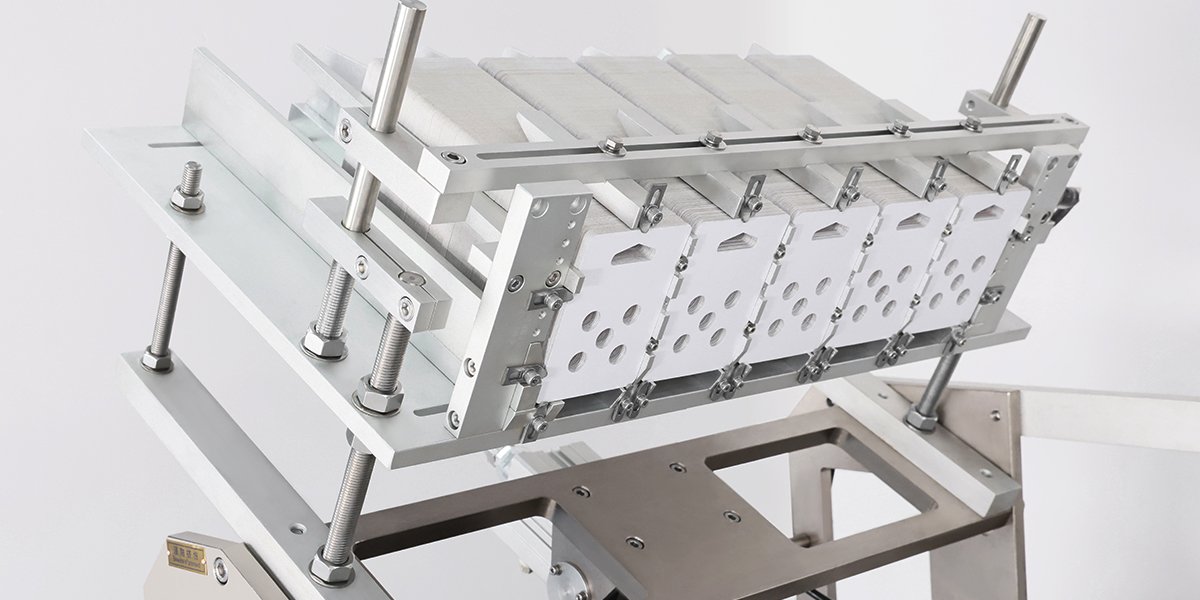
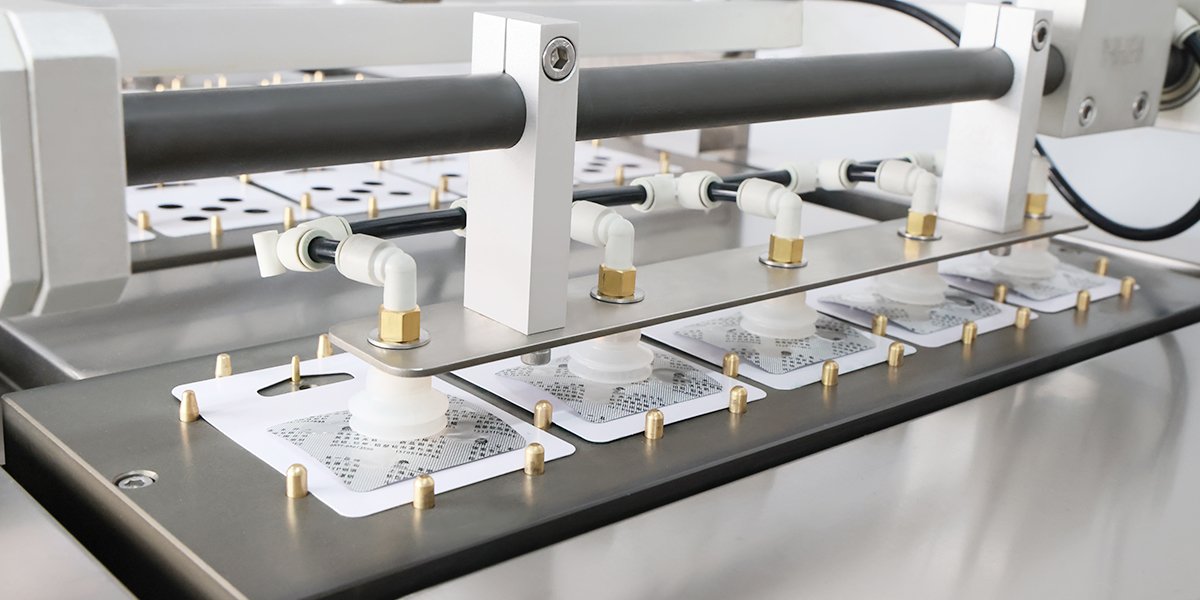
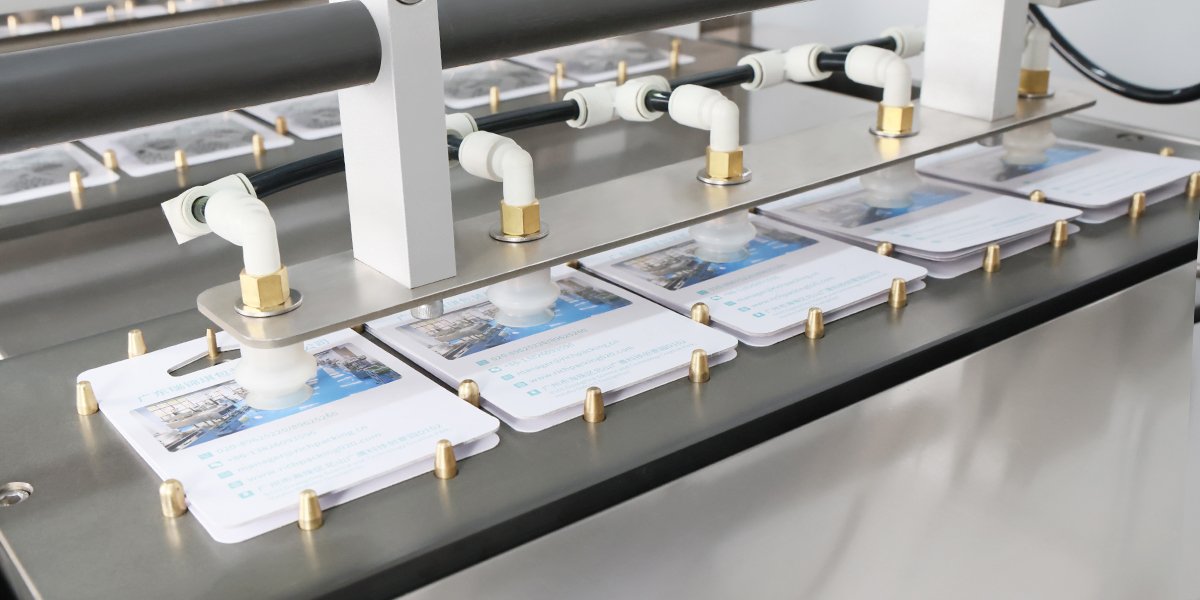
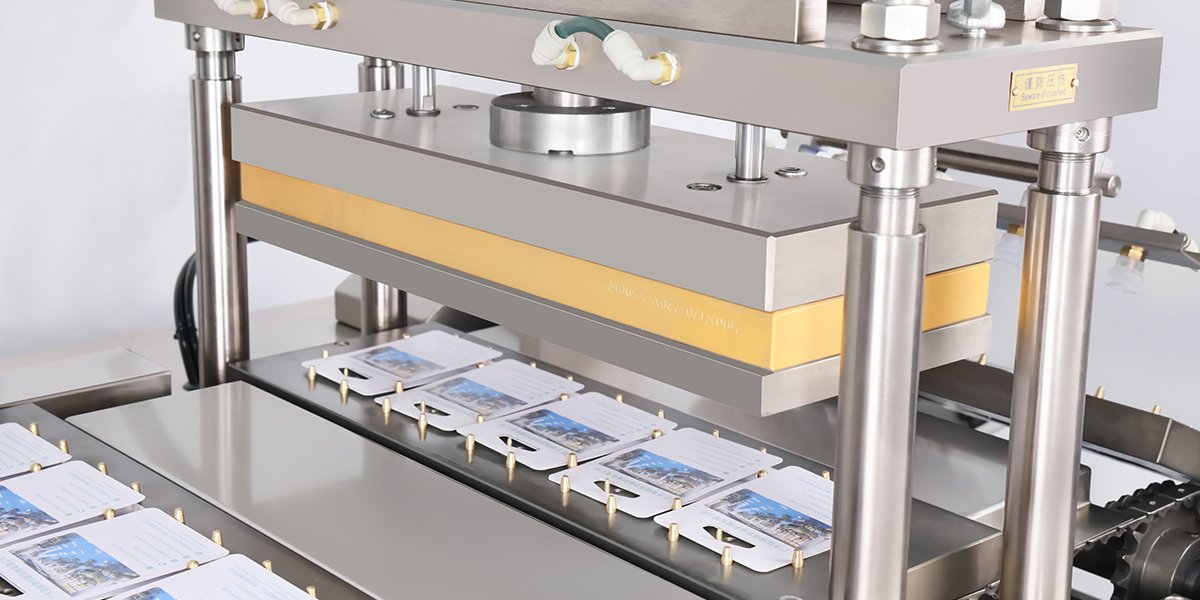
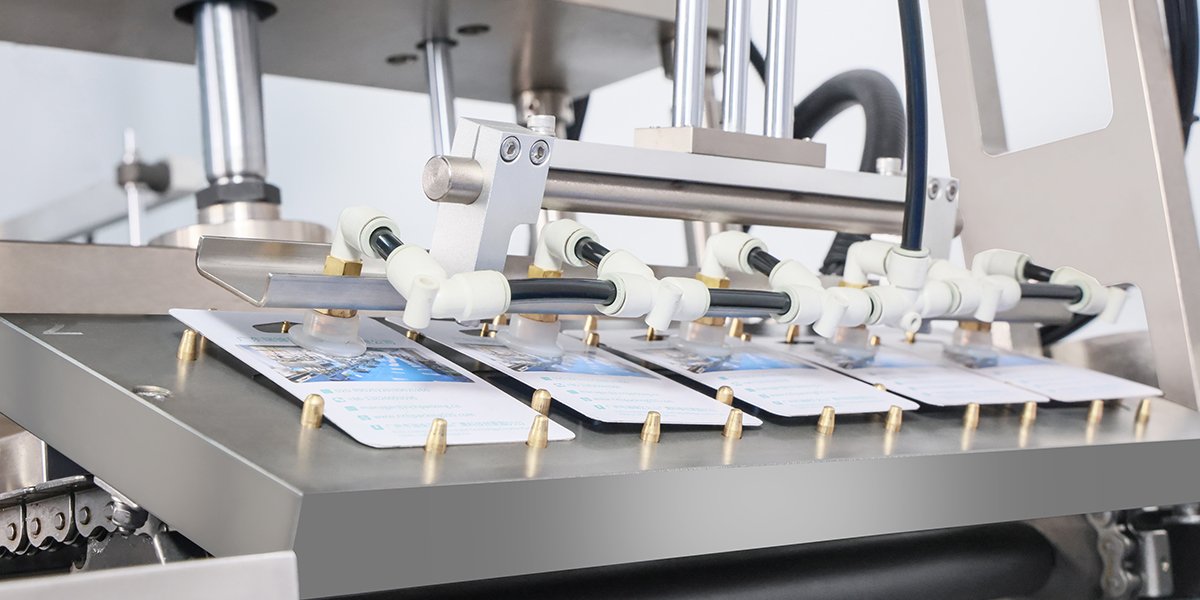
Technische Parameter
Wählen Sie die beste Maschine entsprechend der Beutelgröße aus.
Machine Mold | RD-BCP-350Pro | RD-BCP-500Pro | RD-BCP-650Pro |
Produktionskapazität | 3,600 Plates/h | 5,400 Plates/h | 6,400 Plates/h |
Max. Forming Area | 330*210*65mm | 470*220*65mm | 630*220*65mm |
Paper Card Size | 350*220*0.5mm | 500*300*.05mm | 650*300*0.5mm |
Gesamtleistung | 11.8 kW | 12.8 kW | 15.8 kW |
Unterstützende Produkte
NJP-3800D Automatische Kapselfüllmaschine
Die automatische Kapselfüllmaschine NJP-3800D führt leere Kapseln automatisch zu, füllt sie mit Pulver, verschließt sie und gibt sie zur Verpackung aus.
Blister Packing Machine Manufacturer
Blister packing machine manufacturer offer various type machines that boosts output while lowering labor costs and material waste.
Tablet Compression Machine
Tablet compression machine is essential equipment for producing solid tablets by compacting powdered or granular materials.
Fortune 500-Qualitätslieferant
Features Advantage
Ruidapacking hat sich zum Ziel gesetzt, Maschinen höchster Qualität herzustellen, die den GMP-Standards entsprechen und gleichzeitig über effiziente und praktische Funktionen verfügen.
Full Servo Control
The stroke can be accurate to 0.1mm, which is convenient for the alignment of paper cards and aluminum-plastic panels. The adjustment of the pulling distance of the product can be completed with one click on the touch screen.
Stronger Pressure Resistance
The heat sealing station mold is treated with Teflon, with better surface smoothness and pressure exceeding 100 kN.
Hard Anodized Molds
The 28-piece mold is made of high-grade aluminum alloy, the draw-out slot design allows mold changes within 15 minutes.
Wir unterstützen Sie mit umfassendem Service
Wir stehen Ihnen während des gesamten Prozesses zur Seite, von der Auswahl der geeigneten Maschine bis hin zu ihrer lebenslangen Pflege.
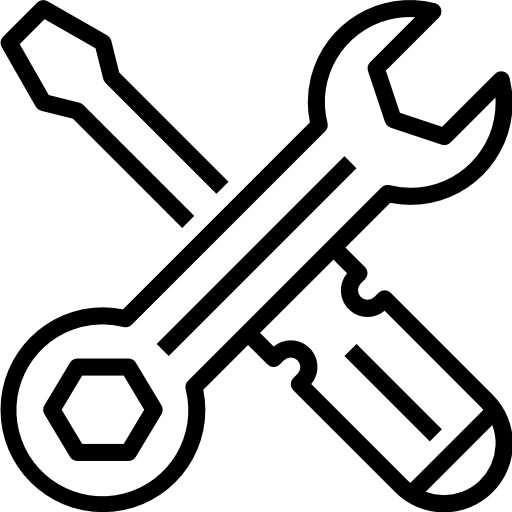
Lebenslange Garantie
Um Ihnen langfristig erstklassige Leistung zu garantieren, bieten wir Ihnen innerhalb von drei Jahren kostenlose Reparaturen und innerhalb eines Jahres kostenlose Ersatzteile. Danach versprechen wir Ihnen lebenslang kostenlose technische Beratung.
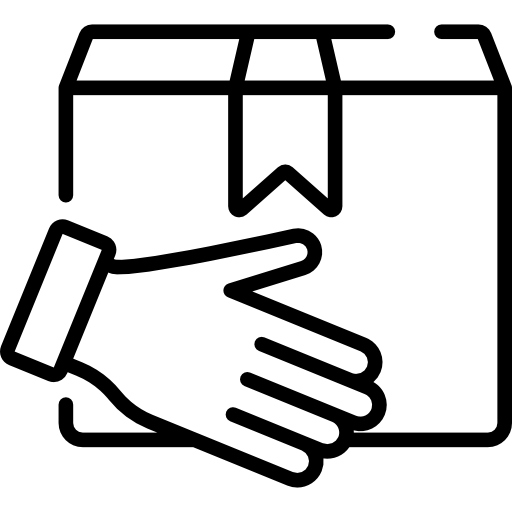
Schnelle Lieferung in 7 Tagen
95% unserer Standardmaschinen sind auf Lager. In diesem Fall kann der Versand innerhalb von 7 Tagen erfolgen. Bei stark kundenspezifischen Produkten beträgt die Lieferzeit nur 20 Tage.
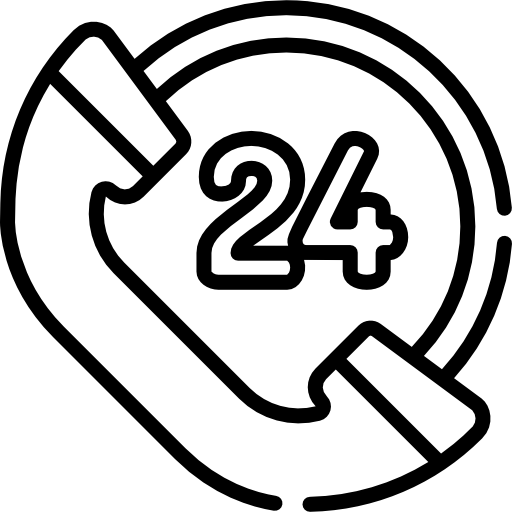
Online-Service
Unsere kompetenten Kundenexperten und Techniker gehen auf Ihre Bedürfnisse ein und lösen alle Ihre Probleme innerhalb von 24 Stunden, einschließlich, aber nicht beschränkt auf die Beantwortung von Fragen und Remote-Video.
Häufig gestellte Fragen
Finding a truly reliable pharmaceutical blister card packaging machine can be a major headache for manufacturers. Common frustrations like poor sealing, product misalignment, and electrical safety concerns lead to wasted materials, rejected batches, operational downtime, and compliance risks. At Ruidapacking, we engineer our blister card machines to eliminate these exact problems, ensuring consistent quality, maximum efficiency, and uncompromised safety. Discover how our precision design solves the industry’s top three paper card packaging challenges.
1. Weak Sealing & High Reject Rates
The Industry Pain Point: Many blister card machines struggle with inconsistent or weak heat sealing. This results in blister packs detaching from the paperboard, compromised product integrity, and unacceptably high reject rates – directly hitting your bottom line through wasted materials and lost production time.
The Ruidapacking Solution: Our machines feature a heavy-duty heat sealing station engineered for perfection:
Massive, Controlled Pressure: We apply over 100 kN (10+ tons) of precisely calibrated pressure across the sealing area.
Premium Teflon-Coated Tooling: Sealing surfaces feature advanced Teflon (PTFE) coating, ensuring exceptional smoothness, consistent heat distribution, and preventing material sticking.
Result: Bonds are exceptionally strong and uniform every time. Dramatically reduced reject rates protect your profitability and ensure batch consistency.
2. Misaligned Cards & Poor Aesthetics
The Industry Pain Point: Achieving perfect alignment between the top and bottom paperboards is critical. Misaligned cards look unprofessional, can hinder functionality (e.g., hang holes blocked), and lead to consumer complaints or retailer rejections. Manual adjustments are time-consuming and often ineffective.
The Ruidapacking Solution: Precision alignment is built into our core design:
Dowel Pin Positioning System: We utilize a robust dowel pin location system within the tooling.
Guaranteed Registration: This system securely fixes each paperboard in its exact correct position on the mold before the heat sealing station begins.
Result: Perfect, consistent overlap of top and bottom cards every single cycle. Your finished packs look professional, function flawlessly, and meet the highest aesthetic standards.
3. Electrical Safety Hazards
The Industry Pain Point: Concerns about electrical safety, including potential leakage currents or unreliable components, are serious. These hazards endanger operators, violate strict cGMP and workplace safety regulations (like CE, UL), and create significant liability risks. Downtime for electrical repairs is costly.
The Ruidapacking Solution: Safety and reliability are non-negotiable:
World-Class Electrical Components: We exclusively integrate premium, globally recognized electrical brands (e.g., Siemens, Schneider Electric) known for their reliability and stringent safety certifications.
Robust Wiring & Grounding: Our machines are built with high-grade wiring harnesses and meticulous grounding practices exceeding international safety standards.
Result: Operators work with confidence. You achieve full compliance with cGMP and essential safety directives (CE marked), eliminate electrical hazard risks, and benefit from drastically reduced electrical failure downtime.
Abschluss
Stop battling unreliable blister card machines that compromise your quality, efficiency, and safety. Ruidapacking’s pharmaceutical paper card packaging machines are engineered from the ground up to solve the most persistent problems plaguing the industry. Our commitment to robust construction (100kN+ sealing), precision alignment (dowel pin system), and absolute electrical safety (premium components) delivers:
Higher Profitability: Slash reject rates and minimize costly downtime.
Flawless Quality: Guarantee perfectly aligned, professionally sealed packs.
Uncompromised Safety & Compliance: Meet cGMP and stringent electrical safety standards with confidence.
Bei vorgefertigten Beutelverpackungslinien hängt die Entscheidung für eine Mehrkopfwaage oder eine Tablettenkapsel-Gummizählmaschine als Zusatzgerät von den Eigenschaften des zu verarbeitenden Materials ab. Diese beiden Technologien bieten deutliche Vorteile und eignen sich für spezifische Anwendungen. Die Wahl der falschen Maschine kann zu Effizienzeinbußen, ungenügender Genauigkeit, hohem Materialabfall oder sogar Betriebsausfällen führen.
Die Auswahlkriterien, Stärken und Einschränkungen jedes Geräts werden im Folgenden anhand der wichtigsten Materialeigenschaften detailliert analysiert:
1. Materialeigenschaften
Physikalische Form
Granulate, Flocken, Stäbchen, Brocken (normale/unregelmäßige Feststoffe): Sowohl Mehrkopfwaagen als auch Zähl- und Abfüllmaschinen sind mögliche Optionen; die endgültige Auswahl hängt von anderen Eigenschaften ab.
Feine Partikel: Normalerweise besser für Zählmaschinen geeignet.
Pulver, Pasten, Flüssigkeiten, viskose Materialien: Weder Mehrkopf-Abfüllwaagen noch automatische Zählmaschinen sind geeignet. Diese erfordern volumetrische Abfüllanlagen (Schneckendosierer, Kolbendosierer, Flüssigkeitsdosierer) oder Nettowaagen.
Individuelles Gewicht/Größe
Großes und relativ gleichmäßiges Einzelgewicht: (Große Kekse, Schokoriegel, ganze Früchte, Spielzeugteile) Mehrkopf-Kombinationswaagen bieten im Allgemeinen Vorteile hinsichtlich Effizienz und Kosteneffizienz.
Sehr geringes oder stark schwankendes Einzelgewicht: (Kleine Pillen, Samen, Gummibärchen, Kleinteile) Automatische elektronische Zählmaschinen zeichnen sich durch Präzision und minimalen Abfall aus. Mehrkopfwaagen haben bei sehr leichten Artikeln Probleme mit der Genauigkeitskontrolle, und kleine Artikel können während des Betriebs durch „Wegfliegen“ (Lufteintrag) in den Wiegebehältern verloren gehen.
2. Mehrkopfwaagen
Das Material wird von einem Hauptvibrationsförderer in mehrere (typischerweise 8–24) unabhängige Wiegebehälter (Wiegetrichter) verteilt. Ein Computersystem erfasst kontinuierlich das Gewicht jedes Behälters und ermittelt mithilfe eines Kombinationswiegealgorithmus schnell die Behältergruppe, deren Gesamtgewicht dem Zielgewicht am nächsten kommt. Die ausgewählten Behälter entleeren sich gleichzeitig in einen darunterliegenden Auffangtrichter und leiten das Material in den Verpackungsbeutel.
Vorteile
Hohe Geschwindigkeit: Das Kombinationswiegeprinzip ermöglicht außergewöhnlich hohe Wiegegeschwindigkeiten (normalerweise 100–200 Beutel/Minute, bei Hochgeschwindigkeitsmodellen über 300 Beutel/Minute) und ist daher die bevorzugte Wahl zur Maximierung der Produktionsleistung.
Hohe Genauigkeit: Bei frei fließenden Materialien mit moderaten Einzelgewichten erreichen Mehrkopfwaagen eine sehr hohe Wägegenauigkeit (±0,1 g bis ±1 g oder besser, je nach Material und Zielgewicht). Der Kombinationsalgorithmus gleicht individuelle Dosierungsschwankungen effektiv aus.
Breiter Gewichtsbereich: Kann Verpackungsspezifikationen von wenigen Gramm bis zu mehreren Kilogramm verarbeiten, indem das Zielgewicht und die Eimergröße angepasst werden, und bietet so eine hohe Anpassungsfähigkeit.
Ideal für frei fließende Materialien: Verarbeitet Granulate, Flocken, Brocken und andere frei fließende Materialien reibungslos und effizient.
Relativ einfache Reinigung und Wartung: Verfügt über eine relativ standardisierte Struktur; Teile, die mit dem Material in Berührung kommen (Vibrationsförderer, Eimer), sind normalerweise zur Reinigung abnehmbar.
Nachteile
Probleme mit schlecht fließenden Materialien: Materialien, die zum Kleben, Verklumpen, Ölen oder Feuchtigkeit neigen, können leicht im Vibrationsförderer, in Pufferbehältern oder Wiegebehältern verstopfen, was zu ungleichmäßiger Zuführung, verringerter Genauigkeit oder sogar zu einem Maschinenstillstand führt.
Herausforderungen bei kleinen/sehr leichten Materialien: Extrem kleine oder leichte Gegenstände (z. B. winzige Samen, kleine Pillen) neigen dazu, durch den Luftstrom in den Wiegebehältern wegzufliegen, was zu Materialverlust führt. Auch die Genauigkeitsvorteile nehmen bei sehr kleinen Zielgewichten ab.
Mögliche Schäden an zerbrechlichen Produkten: Die Taumelbewegungen im Vibrationsförderer und beim Schaufelauslauf können Stöße und Reibung verursachen und so möglicherweise sehr zerbrechliche Produkte (Kartoffelchips) beschädigen.
Probleme mit unregelmäßigen/sich verwickelnden Materialien: Lange, flache oder faserige Gegenstände können sich in den Vibrationsförderschienen oder Schaufeleinlässen verwickeln oder verklemmen.
Gibt das Gewicht an, nicht die Anzahl: Gibt ein Zielgewicht aus, nicht die genaue Stückzahl. Nicht geeignet für Anwendungen, die genaue Mengen erfordern (Artikel werden nach Stückzahl verkauft).
3. Elektrisch Zählmaschinen
Zähl- und Abfüllmaschinen isolieren einzelne Artikel mithilfe von physischer Trennung oder Bilderkennung und zählen sie. Zu den gängigen Typen gehören:
Zähl- und Abfüllmaschine: Die Artikel werden auf Vibrationsbahnen aufgereiht und über Lichtschranken gezählt.
Inspektionszählmaschine mit CCD-Kamera: Hochgeschwindigkeitskameras erfassen Bilder fallender Gegenstände und eine Bildverarbeitungssoftware identifiziert und zählt einzelne Einheiten.
Vorteile
Liefert genaue Stückzahlen: Die einzige Lösung für Anwendungen, die genaue Stückzahlen erfordern (Pharmazeutika, Gummibärchen, Süßigkeiten, elektronische Komponenten).
Überlegene Handhabung schlecht fließender Materialien: Übertrifft Mehrkopfwaagen im Allgemeinen bei der Verarbeitung feuchter, öliger oder klebriger Materialien bei reduziertem Verstopfungsrisiko.
Hervorragend geeignet für kleine Pellets: Ideal für das hochpräzise und abfallarme Zählen kleiner Pillen, Samen und Süßigkeiten.
Bewältigt unregelmäßige Formen effektiv: Fortschrittliche Bildzähler können Gegenstände mit unterschiedlichen und anspruchsvollen Geometrien genau identifizieren und zählen.
Geringer Materialverlust: Durch das Zählen wird normalerweise das Umkippen des Wiegebehälters vermieden, wodurch Verluste durch wegfliegende Teile oder Produktrückstände minimiert werden.
Geräuscharm: Weniger Vibrationskomponenten im Vergleich zu Mehrkopfwaagen führen normalerweise zu einem niedrigeren Geräuschpegel.
Nachteile
Geringere Geschwindigkeit: Die absolute Geschwindigkeit ist im Allgemeinen geringer als bei Mehrkopfwaagen (insbesondere bei kleinen Artikeln). Hochgeschwindigkeits-Bildzähler können zwar 100–150 Stück erreichen, dies führt jedoch zu geringeren Verpackungsgeschwindigkeiten (60–90 Beutel/Minute für 100er-Packungen) im Vergleich zu Hochgeschwindigkeitswaagen.
Die Gewichtsgenauigkeit hängt von der Einheitlichkeit der Einheiten ab: Die Zählgenauigkeit beträgt 100%, die Genauigkeit des Verpackungsgewichts hängt jedoch ausschließlich vom gleichbleibenden Gewicht der einzelnen Artikel ab. Erhebliche Gewichtsschwankungen (unregelmäßige Trockenfrüchte, Nüsse) führen zu großen Schwankungen des Verpackungsgewichts.
Empfindlichkeit gegenüber Artikelverklumpung: Wenn zwei oder mehr Artikel zusammenkleben und als einer gezählt werden, liegt eine Unterzählung vor. (Lösungsbeispiel: Unsere spezielle Süßigkeitentheke bekämpft Verklumpungen mit vier Schlüsselfunktionen:)
Trichterrührer mit Stacheln: Verhindert, dass sich Gummibärchen vertikal stapeln.
Anti-Klumpen-Verteilerwalze: Sorgt für eine gleichmäßige Verteilung der Charge, indem sie ein Anhaften verhindert.
Teflon-Dimple-Panels: Trennen die Gummis vollständig und ermöglichen ein sanftes, schnelles Gleiten.
Vergrößerter PTFE-Auslassanschluss: Reduziert Verstopfungen und erhöht die Geschwindigkeit um 58%.
Komplexe Geräteauswahl: Die Materialeignung der verschiedenen Thekentypen unterscheidet sich erheblich. Für eine optimale Auswahl sind daher Expertenwissen und Tests erforderlich.
Hohe Kosten für Bildzähler: Die Anfangsinvestition für leistungsstarke Bildzählsysteme kann beträchtlich sein und übersteigt häufig die Kosten für eine Mehrkopfwaage.
Eingeschränkte Kapazität für große/schwere Artikel: Das Zählen sehr großer Stücke (ganze Schokoriegel, große Spielzeuge) ist strukturell oft unpraktisch, langsamer und weniger kosteneffizient als die Verwendung von Mehrkopfwaagen.
4. Zusammenfassung und Leitfaden zur Geräteauswahl
Besonderheit | Mehrkopfwaage empfehlen | Empfehlen Sie eine automatische Zählmaschine |
Kernanforderung | Das Zielgewicht hat Priorität; streben Sie nach maximaler Geschwindigkeit und Effizienz | Eine genaue Stückzahl ist unerlässlich; oder die Materialeigenschaften machen das Wiegen ungeeignet |
Fließfähigkeit des Materials | Gut (trocken, rieselfähig) | Schlecht/Durchschnittlich (ölig, feucht, klebrig, neigt zur Brückenbildung) |
Materialform | Vorwiegend Granulate, Flocken, Brocken | Vorwiegend Feinpartikel, Mikropellets, unregelmäßig geformte, flache, längliche Gegenstände |
Individuelles Gewicht | Mittlere bis große oder kleine, aber gleichmäßige Partikel | Sehr kleine Artikel oder Artikel mit großen Gewichtsschwankungen, die eine Stückzählung erfordern |
Verpackungsgenauigkeit | Hohe Gewichtsgenauigkeit (±0,1 g – ±1 g) | 100% Zählgenauigkeit (Die Gewichtsgenauigkeit hängt von der Einheitlichkeit der einzelnen Stücke ab |
Geschwindigkeit | Sehr hoch (100–300+ Beutel/Minute) | Mittelhoch (hängt von der Artikelgröße und der Zähltechnik ab; normalerweise niedriger als Waagen |
Anwendungen | Snacks (Kartoffelchips/Nüsse/Süßigkeiten), Tiefkühlkost, Tiernahrung, Kaffeebohnen, Eisenwaren, chemische Granulate | Arzneimittel (Tabletten/Kapseln), Nahrungsergänzungsmittel, Samen, Gummibonbons, elektronische Komponenten, hochwertige Artikel, verkauft nach Stückzahl |
5. Best Practice-Empfehlungen zur Unterstützung der Produktauswahl
Führen Sie strenge Materialtests durch: Senden Sie ruidapacking echte Materialproben zum Testen. Überzeugen Sie sich selbst von der Verarbeitungsleistung, Genauigkeit, Geschwindigkeit und dem Materialverlust der Geräte bei Ihrem spezifischen Produkt.
Planen Sie für zukünftige Produktionsanforderungen: Wenn Sie in Zukunft möglicherweise Materialien mit unterschiedlichen Eigenschaften verpacken, priorisieren Sie Geräte mit Kompatibilität oder Flexibilität zur Handhabung unterschiedlicher Produkte.
Sorgen Sie für eine nahtlose Integration in die Produktionslinie: Stellen Sie sicher, dass sich die von Ihnen gewählte Dosieranlage reibungslos sowohl in die vorgelagerten Zuführsysteme (Aufzüge, Lagerbehälter) als auch in die nachgelagerte Verpackungsmaschine integrieren lässt.
Leistung anpassen: Überprüfen Sie die Kompatibilität hinsichtlich Geschwindigkeit und mechanischer/physischer Schnittstellen, um Engpässe zu vermeiden.
Priorisieren Sie den Support und Service des Lieferanten: Wählen Sie einen Lieferanten mit fundierter technischer Expertise und einer nachgewiesenen Erfolgsbilanz in Bezug auf reaktionsschnellen, hochwertigen Kundendienst und Support.
Durch sorgfältige Bewertung der wichtigsten Eigenschaften Ihres Materials und ein umfassendes Verständnis der wichtigsten Stärken und Schwächen von Mehrkopfwaagen und automatischen Flaschenzählmaschinen können Sie sicher die am besten geeignete, effizienteste und kostengünstigste Dosierlösung für Ihre Verpackungslinie für vorgefertigte Beutel auswählen.
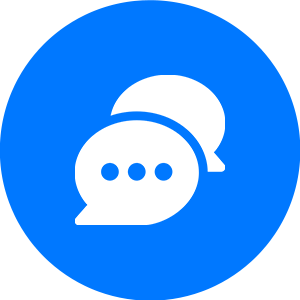